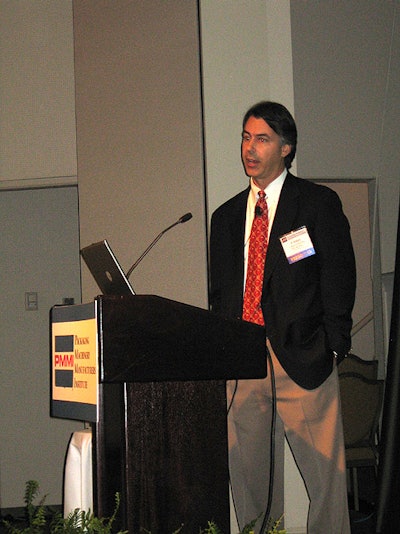
Total Cost to Develop: ELAU offers PMMI members a ‘lean design’ roadmap
WASHINGTON D.C. Monday November 7 2005 – Lead speaker at the Packaging Machinery Manufacturers Institute’s annual meeting ELAU president Christopher Zei gave leaders of North America’s top packaging machine builders a road map to add value and reduce costs by adopting a systematic and modular approach to mechatronic engineering.
The numerous benefits are shared by OEMs and their customers alike and include reductions in engineering and testing time better protection of intellectual property faster delivery smaller footprints new profit centers and lower ongoing software maintenance costs.
A winning perspective
PMMI has embarked on a multifaceted campaign to proactively support its member companies in the increasingly competitive world marketplace. PMMI leaders invited ELAU to brief its members on technology trends based on the company’s demonstrated abilities and global presence.
Zei said “we’re honored to have the opportunity to share some of the technologies that we’re finding packagers to be most interested in exploiting. We look forward to developing these capabilities together with PMMI companies in the year ahead.”
Attack indirect costs achieve ‘generational change’
To describe the benefits Zei has coined the term “Total Cost to Develop” or TCD which corresponds to Total Cost of Ownership (TCO) for end users. While some incremental savings may still be had from direct costs such as materials and labor Zei asserted that only by attacking indirect costs will builders achieve generational change -- both in terms of economies and functionalities.
Don’t let specifications turn OEMs into systems integrators
ELAU which is steadily building market share with visionary PMMI member companies has until recently been best known for its long record of success in the world’s other major centers of packaging machinery development.
“In Europe builders actively seek the best control technology possible. Then they sell their machines worldwide on the resulting merits” Zei explained. “In North America the norm is to accommodate user specifications even when performance may be compromised.
“In so doing we become systems integrators – instead of taking control of the design process. Instead of exploiting the best available automation technology we end up dedicating resources to making less than optimal solutions work – and for the same customers.”
Zei suggested that this is neither the most profitable approach nor the one meeting the needs of global companies.
A world gone “mod”
Zei illustrated the development time performance and maintenance constraints of control hardware architectures that are limited to running monolithic -- or what packagers now describe as “spaghetti” – code instead of modular software.
“Correctly applying modular architecture is a balance between mechanical and software modularity” Zei explained. “One must recognize and work with the other.”
More end users now call for modular standardized approach
Education training and standards initiatives he noted are correcting this mindset in North America. This is why packagers here are beginning to specifying a standardized modular approach to automation software. For example he noted that 1 new ELAU-equipped packaging machines running modular automation software are installed per year in North America.
End user proponents are becoming more vocal in their shift from internal to international standards that enable modularity. They’re doing so as much for its inherent maintainability as its performance advantages.
Virtually Zero Cabinet initiative™ (VZCi) raises eyebrows
Imagine a machine with no control cabinet. Zei recently asked packaging machine specifiers from a major CPG and a major pharma why they weren’t buying more North American machines. Their answer was incredibly simple. They told him they did not have the room in their facilities for the large electrical cabinets. In some instances the control cabinet was actually bigger than the machine itself.
Zei showed how large floor standing cabinets are being reduced first to small top-mounted cabinets to drawers and eventually to a centralized controller mounted in the operator panel.
To accomplish this self-contained servo actuators are becoming increasingly distributed around the machine. Because the motor and drive are integrated they don’t need any cabinet space – and much less wiring. Zei gave the audience a glimpse of the company’s new iSH Series integral motor/drive technology that will be introduced in the coming year.
New technology is purpose-built for packaging
In the past two years ELAU has made rotary fillers cappers and labelers a practical reality with their purpose-built PacDrive SCL integral servo/drive that vastly simplifies implementation on rotating carousels. These applications were the precursor of the Virtually Zero Cabinet intiative™.
Past attempts to integrate drive electronics with motors have always been hampered by the effect of heat generated by the motors on the electronics. ELAU’s breakthrough designs use new motor and electronics technologies with better thermal properties to do the job.
Robotics -- minus ‘black boxes’ -- come on strong
An example of modular software Zei highlighted ELAU’s ready-to-parameterize robotic software object library. The objects known in the IEC 61131-3 standard as Function Blocks contain all the complex kinematics algorithms to control the most popular robot configurations used for pick-and-place carton and case packing and end-of-line. These include Cartesian articulated SCARA portal and gantry designs.
The result is a new profit center for machine builders wishing to embed innovative robot mechanisms into their designs and freedom from supporting ‘black box’ proprietary robot controllers for packagers seeking the ultimate in packaging flexibility.
Zei showed examples of robotic packaging machines introduced at PACK EXPO Las Vegas and at interpack this year. They were a radical departure from conventional cartoners and case packers. These machines have essentially become clusters of robot arms with quick change tooling and servo collating belts.
About ELAU
ELAU a company of $12 billion Schneider Electric equips over $1.5 billion worth of the world’s best machines annually. Currently over 25 PacDrive systems are deployed in packaging machinery worldwide. PacDrive is the first truly integrated automation architecture capable of performing the functions of PLC motion control robotics temperature control PLS MES data interface and more in a single standards-based software environment.
For more information visit www.elau.com or email [email protected].