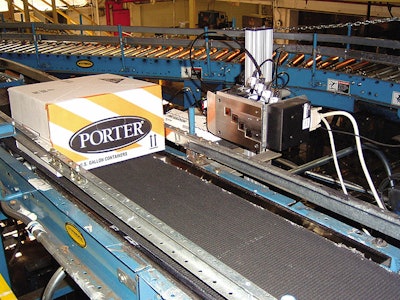
The ability to change codes on cartons often and the need for clean virtually maintenance-free operation were keys in PPG Industries Inc. choice of case coding equipment at its East Point GA plant.
The plant has multiple lines that package paints in quarts and gallons under a range of brand names including Pittsburgh® Paints Olympic® Paints and Stains and Porter® Paints. The paint cans are cased on packers and move along a conveyor to a palletizer.
Downstream of the case packers and before the palletizer each case gets coding information. “We have a large number of codes” says Hugh Bishop plant engineer at PPG Industries. “What’s the color and the brand what are lot and batch codes and what are the customer’s specifications?”
The variety of coding demands dictated a computer-driven coding system such as inkjet technology. But the need for simple maintenance led PPG Industries to adopt PRISM’s JETPACK line of printers using HP thermal inkjet technology. The printers delivered advantages compared to alternative inkjet techniques.
“We were adding a fourth case packer to the plant and we were looking for some alternatives to our earlier inkjet equipment” Bishop explains.
The lines that were already in operation were equipped with other inkjet equipment and maintenance of the print heads was the biggest shortcoming of the equipment according to Bishop. “The print heads would cost between $3 and $5 each and the print quality would degrade through normal use” Bishop explains. “We would have to pull print heads and have them repaired or rebuilt adding to our costs and maintenance requirements”
Human-readable bar code capability
Bishop says plant personnel saw the HP thermal inkjet equipment at a trade show in Atlanta. It was demonstrated by PRISM Incorporated an HP partner in applying thermal inkjet technology for packaging operations. The product is called the JETPACK 5000. It is a product in the JETPACK line of carton marking and coding solutions. The units configured by PRISM feature multiple print heads that can be used in combination to produce both human-readable characters and bar codes up to 2 inches in height.
The technology leverages simple proven thermal inkjet cartridges and adds industrial-grade ink formulations that meet requirement of package coding end users. The low cost of print cartridges allows a packager to replace them on a schedule that fits the packager’s maintenance strategy—changing them even as frequently as when changing ink supplies. It simplifies maintenance and consistently delivers the print quality.
PPG Industries installed the first of the new printers on a line coding cases for quart cans of paint. Guide rails position cases approximately 1?16-inch from the print heads. The print heads are mounted to create codes on the top end flap of each case as it moves down the conveyor to the palletizer. Line speeds vary and the coding equipment speed varies to accommodate changes in conveyor line speed.
Typical codes are two lines with a distance of 11?2 to 2 inches from the top of the top code to the bottom of the bottom code. A typical code has a lot or batch code on the top and human-readable information on the bottom. The four overlapping print heads allow variation in the codes. “Some codes are an inch high and we use two print heads to do that” Bishop says.
The system is networked through a computer that controls all four PRISM printers in the plant. PPG Industries personnel initiate the coding setup by scanning the bar code on a can of paint from the run. The procedure eliminates errors that might be introduced by keying in code information into the printer’s controller. The computer then sends the information to the controller of the appropriate printer.
Controller provides back-up
Each printer has its own controller with a touch screen. Standard operating procedures do not utilize the touch screen at the controller. However Bishop notes “The touch screen allows programming at the controller giving us a back up if we need it.”
Ink feeds to the print heads from a bag-in-box ink supply. Each box holds 370 milliliters of ink. This configuration works best for the PPG Industries operation but other ink supply configurations are available.
The procedure at the East Point plant is to change the print heads when changing the bulk ink supply. The ink supply is connected to the print head with a plastic tube affixed to the print head.
“When you run out of ink you change out the whole thing—the box of ink the tube and the print head” Bishop explains. “The beauty of this is that you can change the print head as fast as you can change the print head in a DeskJet printer. It is just ‘pop out’ and ‘pop in.’
“It got to the point I could change a print head between two boxes coming down the conveyor” Bishop says.
Following the success with the new quart line PPG Industries retrofitted JETPACK 5000 printers on the plant’s existing lines that run quarts and gallons. Printers on lines that run gallons see the most use running three shifts a day.
“There are cost advantages both from the cost of the ink and the maintenance” Bishop continues. “These printers are neat and clean compared to what we were doing. There are a lot of little advantages. Clean up only requires water. And the earlier printers had a tendency to leak on the floor creating a mess.”
All these factors combine to produce a lower total cost of ownership (TCO) than other coding and marking solutions.
See sidebar to this article: PRISM delivers HP inkjet technology with proven advantages