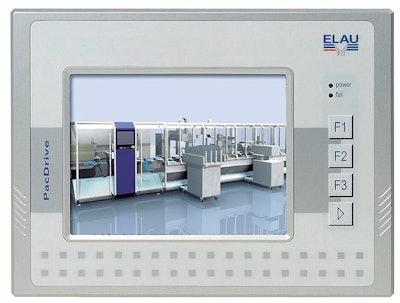
Previously we asked the rhetorical question What’s under the hood of your automation system? More and more control vendors are adopting the IEC 61131-3 programming language standard but that doesn’t make them all equally capable. That makes it important to thoroughly evaluate a control platform before committing to it on your packaging machine.
In this article we provide Functional specification text for PLC and servo capabilities that packagers and machine builders can download and paste into their corporate or site control specification documents.
Before you get to the RFQ stage however here are ten pre-qualifying questions to ask prospective automation suppliers.
1. How do you integrate motion and logic? Is all control done within the same processor or do you still employ a rack-based system?
To be truly integrated motion and logic control should be performed within a single IEC 61131-3 conforming program and on a single processor. Backplanes and multi-card solutions simply slow things down too much.
2. Do you support and conform to all the IEC 61131-3 programming languages?
It’s important to conform to all the languages in the standard and to follow Best Practices in programming using each of the languages to its best advantage. The resulting control architecture will then be modular and clear instead of monolithic and cryptic.
3. What do you provide to help machine builders develop world-class machines as quickly as possible? How many packaging machine functions do you provide?
Not only should a completely open programming environment be mandatory it needs to be supported by a software library containing literally hundreds of pre-tested software objects (IEC Function Blocks) along with routines and programming templates designed specifically for packaging machines.
4. How many servo motors can you control with one system? What is the motion network update rate? How many virtual axes?
The current state of the art is 99 axes per controller with an overall update rate of 1 2 or 4 milliseconds maximum for the entire network not cumulative per axis. An unlimited number of virtual axes should be supported.
5. Are required components such as Ethernet Sercos field buses etc. supplied as additional option cards or as standard equipment? What do I need to access all parameters and other data in the system?
All these features should be standard equipment. Standard methods for interfaces should also include OPC server Web server data/message logger digital oscilloscope and other tools to give you complete control over the data flowing into and out of your machines.
6. What solutions do you have for rotating capping/filling/labeling machines?
Integral motor/drives are key to upgrading rotary machines in some cases doubling throughputs. These motor/drives can be mounted right on a rotating table providing precise control of capping head torque bottle plates and dosing systems.
7. How do you handle electronic camming? Do you still use x-y tables and simple 3rd degree polynomials? Can you change any segment of the cam on the fly?
Insist on 5th degree polynomial cam profiles and the ability to change cams on the fly. Cam tables should never be downloaded to a servo drive this is a last-generation practice before Pentiums that distributed processing tasks at the expense of speed. Cams should be generated mathematically by the controller during operation.
8. What software costs can we expect for our entire group of engineers? How many software components do I have to buy for each engineer?
Hidden software costs can add up quickly but not if you require that the vendor’s software development environment be provided as a site license . . . so all of your engineers can access the tools libraries and templates they need for a fixed cost.
9. What are you doing to reduce the amount of cabinet space on machines?
Do your machine cabinets seem to be getting as big as your packaging machines?
Space-saving controllers and drives can reduce cabinet size by as much as 50% compared to conventional PLCs motion controllers and drives.
10. How many thousands of packaging machines did you equip with servosystems in the last year?
This is a pivotal question. When it comes to domain expertise it’s not how many thousands of PLCs or even servos the company sells it’s how many thousands of packaging machines their servos equip every year.