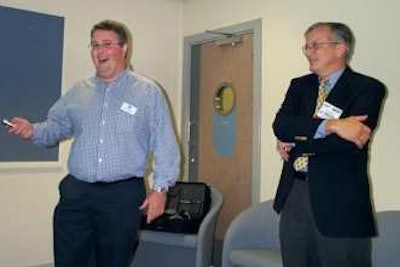
By Wednesday morning, about all that remained of our Journalists' Inward Mission was a quick trip down the aisles of the PPMA Machinery Only show at the National Exhibition Centre in Birmingham. This show will continue to be held annually at the NEC with the exception of every third year, when it will retreat from view and be folded into the Total Processing and Packaging Show.
Also awaiting us at the NEC were two representatives of OMAC, which stands for Open Modular Architecture Controls. The OMAC Packaging Workgroup is in the process of refining its mission to promote commonly accepted guidelines (referred to as Plug-and-Pack™) in an effort to speed advancements in packaging machinery and packaging automation. OMAC co-chair Andrew McDonald of Unilever (photo 1, left) and OMAC executive director Keith Campbell of the Louisiana Center for Manufacturing Sciences treated us to coffee in the press room and an update on the latest doings at OMAC. In an energetic presentation where at any moment either speaker had the floor, the basic point that came across is something like this.
Packaging machinery is undergoing significant technological change, much like the changes visited upon the typewriter or the wristwatch in years gone by. These changes are driven by the business needs of packaging end users and advances in technology. This change should be embraced for the health of the overall packaging community. It's partly a matter of bringing process control concepts to the packaging function. It's also a matter of making packaging machines more intelligent, and as they become more intelligent, they need to express their conditions in the same language. Only by adhering to commonly accepted standards can this happen.
It's not just technology for technology's sake, said McDonald and Campbell. It's really about business benefits. Take the brewing industry, for example. We're seeing more and more variety in primary and secondary packaging. That means packaging machinery has to be more flexible than ever. If the machines are built upon a foundation of commonly accepted standards—where motion, logic, and communications capabilities are all integrated on a plug-and-play basis—flexibility comes automatically without any need for expensive and time-consuming reprogramming. Or look at pharmaceutical manufacturing, where serious streamlining of the validation process is required. Pharma people want a standard machine state model because they know it will result in machines that are easier to validate. If the packaging community can build machines from standardized components that have already been validated, we can cut the time and energy required to validate machines.
It isn't just the brewing industry or the pharmaceutical industry that OMAC is focused on, said McDonald and Campbell. The goal is to look across all industries to find common issues and core requirements and to deliver the message that global guidelines for open architecture and third-generation performance in packaging machinery is the key to the future.
With the conclusion of the OMAC presentation, I was able to walk the aisles of the PPMA show. Time was scarce, as a 2:30 bus to London beckoned. But the brief notes that follow and a few photos taken at the show provide at least a sample of what the show had to offer.
Featured at the stand of Partners In Packaging, which represents the German machinery maker Vepa, was a carton erector capable of a unique 4-corner seal that makes a paperboard carton practically waterproof. R. Twining & Co., the well known marketer of teas, has taken a fancy to this equipment for cartoning its tea bags because it keeps powder or dust from one tea flavor from compromising the flavor of another tea. A Twining carton is shown here (photo 2).
Safeline was showing its T-42 low-energy x-ray inspection system (photo 3). It runs to 400 packs/min depending on pack size and inspects for bone, metal, glass, rock, and other contaminants.
At Automated Packaging Systems, the AB 180 was featured (photo 4). A successor to the Autobag Excel system, the AB 180 offers improved ergonomics, a large operator touch screen, and speeds to 80/min.
At Ishida Europe, on display was a complete, single-source tray-packing line comprising tray denesting, multi-head weighing by a combination scale, tray filling, tray sealing, weigh-price labeling, and pick-and-place case packing (photo 5).
Part 1: How Total came to be: A merger of Pakex and PPMA's Machinery Only show
Part 2: 21st-century packaging machinery trends
Part 3: New developments from U.K. machine builders
Part 4: Off to Sainsbury's--a tour of a U.K. supermarket
Part 5: Coors' new £35 million brewery
>>Part 6: Plug-and-Pack™ update