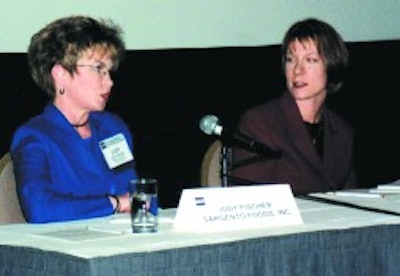
Understanding security hazards and assessing the probability of an incident and its impact were the topics at the Packaging Security Workshop, held in early February in Itasca, IL. Sponsored by the Packaging Machinery Manufacturers Institute (Arlington, VA), the workshop drew more than 140 attendees, from packagers to suppliers to third-party evaluators.
That attendance-in these days of low-turnout conferences-is a strong indicator of the timeliness of the topic. The workshop was created and promoted just a few weeks before the event. But attendees were rewarded by the last-minute appearance of Dr. David J. Armstrong, assistant director of research at the U.S. Food and Drug Administration's Center for Food Safety and Applied Nutrition.
Armstrong was joined by Dr. Chuck Sizer, director of the National Center for Food Safety and Technology, and his associate, Dr. Peter Slade. The three all talked in some detail about FDA's recently issued food safety "preliminary guidances." At the time of the workshop, these proposals were still open for comment by the public and by companies, before FDA finalizes them later this year. That comment period closed just a few weeks later.
Repeatedly stressed throughout the day-long program was that these guidances-even when finalized-will be voluntary rules for companies to employ or not, depending on individual circumstances. The guidances, published Jan. 9, '02 in the Federal Register, are also shown at the agency's Web site, www.fda.gov. Or, suggested Armstrong, copies can be provided by e-mail from [email protected].
Armstrong then moved through a series of slides of the Food Security Preventive Measures Guidance, beginning with a slide that recommends each company review current procedures and make improvements, encourages the commitment of management and employees, acknowledges that all measures are not appropriate for every company, and finally, supports the use of Operational Risk Management so companies can prioritize improvements.
Among the areas the guidance covers, according to Armstrong, are management of food security, the physical facility, employees, computer systems, raw materials and packaging, operations, and finished products. Each company should, he said, work to develop security strategies to include response to tampering or criminal or terrorist events, a recall strategy, and additional steps. Many of the individual recommendations, Dr. Armstrong pointed out, are primarily common-sense initiatives that many companies already employ, such as restricting access to facilities, especially for laboratories or storage of hazardous materials, and screening of employees.
He also recommended that companies should train employees in food security so they not only understand the restrictions but also buy into the program and become extra "sets of security eyes." For raw materials and packaging, FDA recommends that companies tighten up security of shipments, requesting locked and sealed containers, and reconciling the amounts received with the amounts ordered and invoiced, and taking into account any materials that were used for testing.
Risk assessment detailed
Slade and later, Patrick Helm of Lockwood Greene Engineers (Spartanburg, SC), each discussed in detail how a company can look at potential risks, evaluate the consequences, and assign priorities for risk-control measures.
Slade described the process known as Operational Risk Management, a six-step plan to anticipate hazards and reduce the potential for loss. Those steps include identifying the hazards; assessing the severity of them on the company; analyzing control measures; making the risk-control decision; implementing the controls; and finally, supervising and reviewing the plans.
Along with helping minimize the chance for catastrophic consequences to a company, some steps noted by Slade may also have other advantages. For example, the use of cameras to monitor some plant areas for security purposes has actually reduced theft of products and supplies.
Helm's risk-management plan was slightly different, but he presented how to analyze the risks. He went through a typical assessment, where the company identified each risk, then assigned values for probability and severity to learn which risks to control. However, he stressed, risk measurements all changed after Sept. 11. "Probability is the driving factor since 9/11," he told attendees. "The perceived likelihood of something happening is greater, thus driving us to mitigate our risk more often."
Companies must reassess the probability of the risks since 9/11, he said, and companies need to develop programs or technology to control the outcomes and reduce the severity, if or when they occur. In the past, he said, a major company risk was in not getting a product to market on time. Today, he said, the risks threaten loss of life and catastrophe to a company. "However, we can do everything practical to prevent these acts. Moreover, we must assess that which is critical and put measures in place to minimize the risk."
Focusing on packages
Sizer's remarks covered much of the history of package tampering in the United States and reviewed some of the legislative mandates that have helped improve package security. However, he pointed out that "any package can be successfully compromised." But he added that packaging is the first line of defense in protecting food products, and he encouraged attendees to define packaging more broadly than just containers or wrapping. It extends from the farm to the store.
Dr. Sizer reiterated several of the packaging security concepts that FDA had recommended, including secure storage of containers, even down to shipping cases and pallets. However, he pointed out that FDA doesn't really have tamper-evident standards for food packaging. So he offered a test for assessing the tamper evidence for food packages. An FDA handbook, he says, suggests taking six to 12 product samples and attempting to enter the packages surreptitiously using only items that are commonly found in the home.
For food packaging, he strongly endorsed those that have hermetic seals and also display when the package has been compromised. He talked about dagger-type, twist-lock closures on gabletop cartons of juice; full-panel, ring-pull ends on cans; blister packs; vacuum buttons on jars; and sealed paper or plastic flexible packaging.
He also said attention should be paid to secondary packaging by using proprietary tape or seals and accountability for every package. Wrapped pallet loads and more secure trucks were other suggestions.
Panel discussion
The program also featured Jonathan Oakes of Markem Corp. (Keene, NH), who talked about bar coding and other technologies that can secure against counterfeiting and other techniques for package traceability.
The afternoon concluded with a panel discussion that featured Judy Fischer, senior packaging engineer, Sargento Foods, Plymouth, WI, as the only packager. Others on the panel included Michael Richmond, Packaging & Technology Integrated Solutions; Bill Zito, Enercon Industries; Juli Okal, 3M Packaging Systems Div.; Gary Parish, Complete Inspection Systems; John Raterman, Nordson Corp., and Oakes.
At the start, Fischer talked about starch dusting on webs of flexible packaging materials and concern with anthrax contamination. "Our suppliers have moved from light starch dusting to 'slight' starch dusting, and some to none," she said. Fischer also reported that Sargento examined plant security and explained that few visitors are now invited to tour the plant. "Any visitors have to be approved by a vice president," she says, "and they're 100% escorted within the plant."
Later, when asked about a package introduction last year, Fischer reported that the specifications had been in place prior to 9/11, but that they're being reviewed as part of Sargento's risk analysis.
In discussing sealing of shipping cases, Raterman said that most tampering is done through the bottom of the box, which makes it very difficult to see. Now, he said, companies are looking for new technology to provide tamper-evident bottom seals. He related one story about computer products being pilfered from the bottom of the box and replaced with phone books to simulate the original weight of the product.
When asked about security considerations with contract packagers, Sargento's Fischer said her company used co-packers only after a complete audit was performed on their operation. Still, she said, Sargento people are often on-site during production runs. She also described how some ingredients are received double-bagged. That way, she said, the outer bag is removed before the packaged product is sent into the processing area.
Finally, moderator Ben Miyares indicated that PMMI would probably hold similar security workshops in the East and on the West Coast before summer, and the topic would also be part of the program during Pack Expo Intl. this coming November in Chicago.