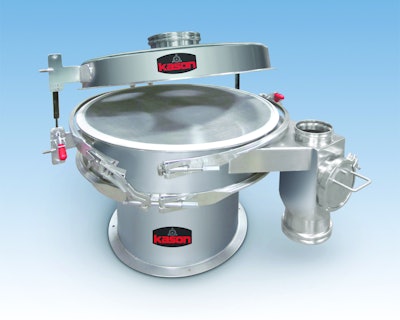
This content was written and submitted by the supplier. It has only been modified to comply with this publication’s space and style.
A new sanitary Vibroscreen® Model K30-1-SS 30 in. (76 cm) screener from Kason Corp. meets cGMP, 3-A, USDA and FDA standards, features sanitary stainless steel construction, gap-free screen frames with quick-disconnect clamps, flexible quick-action connectors at the inlet and outlet, a Clamshell lid, and a removable, sanitary magnet at the discharge spout.
The external, interlocking flange configuration of the screen frame fully envelops the support ring of the screen, allowing the screen’s wire mesh to extend to the interior walls of the frame. The design eliminates the gap between the screen ring and frame wall of conventional screeners, eliminating areas where material would otherwise collect. “The gap-free design dramatically reduces the possibility of contamination due to bacteria growth, and improves sanitizing efficiency, making it suitable for pharmaceutical, food and dairy applications, as well as other applications where cross-contamination is a concern,” says Alamzad.
Screens are mounted to support rings using FDA-approved epoxy and sealed using FDA-approved gasket material, and can be provided with a mesh-tolerance certificate. The wire mesh screening material is offered in 304, 316 and “magnetic” 400-series stainless steel that, if broken, can be captured along with ferrous material contaminants, by a sanitary high-strength magnet at the discharge outlet.