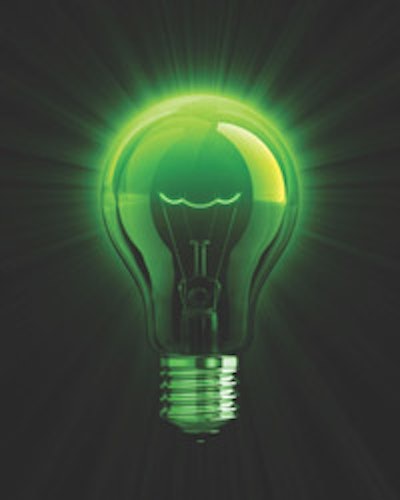
Packworld.comPackaging World
Increasing use of automation, especially robotics.
Implementation of Lean and related production improvements.
Increasing use of automation, especially robotics.
Implementation of Lean and related production improvements.