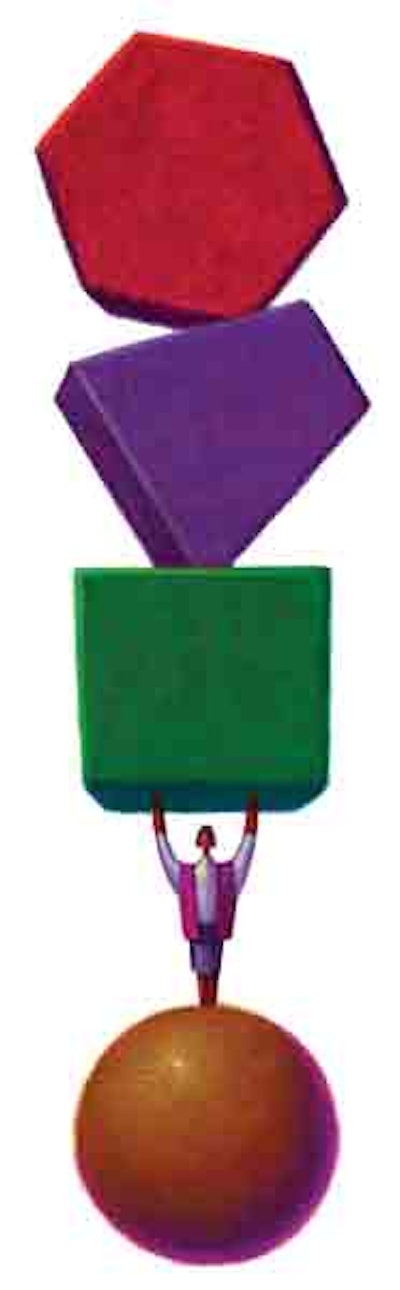
It isn’t your dad’s packaging machinery that’s filling PET bottles of New Age functional beverages at blurring speeds or blister-packaging the latest pharmaceutical products, which, by the way, are inspected by machine vision systems integrated with real-time data collection tools capable of sending instant e-mail alerts of problems.
Welcome to the amazing, and amazingly challenging, world of packaging in 2007.
Amid today’s proliferation of more sophisticated packaging machinery, there’s a growing concern for educating and training mechanics and operators with the skill sets needed to effectively operate and maintain these modern marvels.
Called "upskilling," this trend is gaining attention, says consultant Keith Campbell of Campbell Management Services, who organized a Workforce Upskilling conference in March. According to Campbell, yesterday’s model of a "model" worker just won’t work.
"Today there are PLCs, servos, device networks, cell networks, enterprise integration, sensors, readers, vision, robotics, and closed-
loop control," Campbell says. "The new model is a skilled operator who can perform basic maintenance and adjustment of multiple machines, who can interpret diagnostics, and who can perform as a mechatronics technician multiskilled in mechanics, electrics and electronics, process control, and computer science."
That’s the technical side of the equation. Compounding the problem are demographic trends that tighten the supply of workers with the needed skill sets. According to Campbell, baby boomers are retiring, Gen Yers (those aged 24 and under) are not swarming into manufacturing, and the unemployment rate nationally is 4.5%, making for a tight jobs market. With packagers having difficulty filling job openings, many are turning to automation, which further increases the need for hard-to-find skilled employees.
Pepperidge’s view
One manager reacting to the need for upskilling is Rob Harrison, plant manager of the 800-employee Pepperidge Farm bakery in Denver, PA. "Upskilling is a concern, and right now there’s a shortage of skilled workers. At this same time, a lot of long-term employees are retiring. Replacing them even as plants are ever increasing in technology is a challenge. We’re looking to find ways to improve our internal talent and recruit more skilled candidates."
Added to plant-level pressures are corporate expectations, according to Harrison, who says today’s environment of technology and competition makes this a crucial period.
"There’s a much greater expectation of excellence on the part of companies," he says, "and the expectation for manufacturing sites to improve efficiencies, minimize waste, and maximize uptime is critical. You need to have informed, educated, intelligent people to do that. You need workers who are problem-solvers, which is why upskilling is so critical."
PMMI’s perspective
The upskilling challenge has also gained the attention of the Packaging Machinery Manufacturers Institute, a trade association that represents more than 500 member companies in the United States and Canada.
Although its membership primarily comprises packaging machinery suppliers, through its Certified Trainer Program, both members and end-user personnel such as line supervisors and operators are trained, according to Maria Ferrante, PMMI’s director of workforce development. "Training skills had been lacking, and because training can have such a significant impact on equipment reliability, productivity and safety, we developed the Certified Trainer Program.
"Not only do our members need to provide quality training, but end users need to develop the internal capability to train. This is an area PMMI has been strong in and has had much success," says Ferrante. "We hope to continue to improve the quality of training throughout the packaging industry through the program."
PMMI says a proliferation of certified trainers results in benefits such as faster start-up curves and reduced downtime and materials waste. The program provides trainers with ongoing support through the resource area of the PMMI Web site, Webinars, and newsletters. Better trainers make for better training. For more information, see www.pmmi.org/certified.
In 2007, PMMI launched a Community of Practice to strengthen communications between equipment suppliers and end users. A group that included companies such as Kroger, Kraft, Pactiv, Anheuser-Busch, Goodman Packaging, PIAB, Mettler-Toledo Safeline, Omega Design, and Rockwell Automation met in February and was set to reconvene in June.
Problem solutions
Meanwhile, companies face staffing challenges small and big. Hershey Foods Co. recently announced plans to cut as many as 3,000 jobs and move some of its candy production to Mexico, which together will save it an estimated $170 million annually. Gerald Cockrell, a professor of electronics and computer technology at Indiana State University, Terre Haute IN, believes that might not sound good for Hershey, PA, but that it might be the only way Hershey Corp. will survive.
"The bottom line is that companies that aren’t automated aren’t competitive," states Cockrell.
He believes the solution is to upskill workers through automation systems training programs at community colleges, universities, and technical schools. He suggests workers enroll in appropriate college-level night classes or online classes.
That advice works even better well before a crisis is reached, which is why Harrison is proactive about involving local or regional schools. In 2007 his Pepperidge Farm plant is sending seven workers to the Reading Area Community College (RACC), Reading, PA, which hosted the upskilling conference and offers a curriculum that includes mechatronics.
"RACC’s program focuses on workers’ core skills—namely the electronics and the mechanical—and their understanding of it, their ability to really fix problems," says Harrison. "I’d rather workers learned to troubleshoot in school rather than on a production line where every minute down is costly." It’s too early to comment on its success, Harrison adds, though he expects the workers to develop their skills to a higher level of achievement and competency.
Harrison balances school-based learning with plant-based training. "We’re learning that you need to work to develop internally your own training group and to work with schools to improve their curricula. That improves the skill sets of students so that they can hit the ground running."
That was heard in responses to Packaging World’s Upskilling survey from early 2007. One question asked about schools curricula, and many of the responses centered on machinery troubleshooting skills; select responses can be read in this sidebar entitled Survey takers speak out.
There are other options, too, as PMMI’s Ferrante points out. She encourages companies to consider all available resources including community colleges and workforce development boards, and notes that there are many grant programs available (PMMI maintains for its members a database of state grant programs). She also suggests checking out the resources at www.pmmi.org.
"We really have to get the word out about upskilling to manufacturing at all levels," states Ken Ryan, director of the Center of Automation and Control at Alexandria Technical College, Alexandria, MN (see sidebar entitled An educator’s ‘standard’ view).