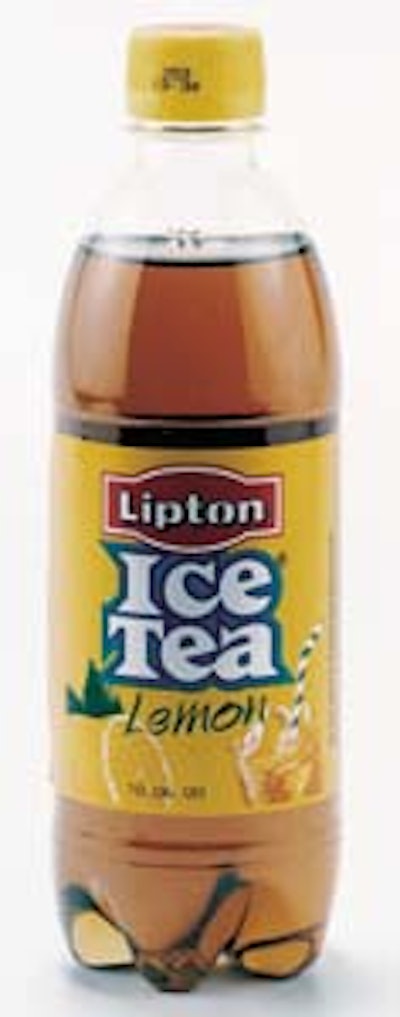
Mineralquelle Eglisau is the first company to operate Krones’ (Franklin, WI) CAF (cold aseptic filling) system, a recently developed aseptic filling system for plastic bottles. Installation at the bottler’s plant in Eglisau, Switzerland, began in April ’99. After rigorous acceptance tests, the company began shipping 1/2- and 1 1/2-L polyethylene terephthalate bottles of Lipton Ice® Tea last October.
Krones’ CAF system is distinguished by its use of a Spirasept immersion sterilizer, which ensures that the inner and outer surfaces of the PET bottles are completely wetted with hydrogen peroxide sterilizing solution. Plastic threaded closures, too, are treated in an immersion sterilizer developed by Krones.
What further distinguishes this line is that it fills nonaseptic carbonated soft drinks as well as fills aseptically beverages like teas. In filling CSD bottles, the Spirasept sterilizer is bypassed, and bottles are conveyed directly into the filling chamber.
Operators program the line for either aseptic filling or CSD beverage filling by making selections at an operator-interface panel. An automated CIP and SIP system makes it possible to switch back and forth from CSD to aseptic filling.
Eglisau technical manager Daniel Boni acknowledges that it’s a bit out of the ordinary to fill aseptically and nonaseptically on the same line. “We do it because we don’t [produce] enough iced tea to occupy the line full time, and we want to produce 24 hours a day on this line,” he explains.
Eglisau is primarily a contract packager handling other companies’ brands. CSD products it runs on the new line are marketed by companies like Pepsi and Schweppes. In tea, however, the company fills only Unilever’s Lipton brand.
Experienced with tea
Eglisau is not new to iced-tea bottling. For four years before the installation of the new line, the firm filled Lipton Ice Tea into PET bottles in a Zurich plant. However, this was not an aseptic operation. The beverage was flash-pasteurized at 70°C for 40 sec and filled at ambient temperature into conventional PET bottles. The bottles then went through a tunnel pasteurizer.
When management decided the Zurich plant had outlived its usefulness and shut it down, iced-tea bottling was diverted to Eglisau. That plant had no room for a 165’x65’ tunnel pasteurizer, so other technology was evaluated. Hot-fillable, heat-set PET was a possibility, but the heavy bottles would have been too costly, says Boni. Aseptic filling was eventually identified as the way to go. The Krones technology was selected for several reasons.
“We needed high speed, we wanted to be able to fill [conventionally] as well as aseptically, and we like the way this system sterilizes the empty bottles,” says Boni. “The Spirasept system puts the whole bottle in a bath. It’s not just a rinse. The entire bottle is submerged for about 40 seconds.”
According to Krones, Eglisau can fill ?-L bottles at 250 to 330/min while running in the aseptic mode and at 660/min for carbonated soft drinks.
Eglisau purchases its bottles from commer-cial blow molders. Both single-use and returnable/refillable bottles are sent through the CAF system in the same manner, and it all begins with automatic depalletizing on a Krones Kettner machine. Bottles are single-filed from a mass flow by line pressure and then fed to an air conveyor that takes them to an infeed worm leading to the Spirasept system.
Arriving on a single track, bottles are gripped by the necks and carried into the bottle carriers that take them through a spiral path in the Spirasept system. Here the bottles are completely submerged and filled with hydrogen peroxide sterilizing solution. After an emptying and drip-dry zone, bottles go through a bath of sterile water that rinses and removes any trace of hydrogen peroxide sterilizing solution. The Spirasept baths act as an air lock separating the sterile filling and capping chamber from the unsterile outside atmosphere.
Emerging from the Spirasept system, bottles are gripped by the neck rings and taken to a 110-valve rotary filler. The bottles are then in a Class 100 sterile chamber that is itself inside a Class 10ęŻ chamber. Operators do not enter the Class 100 chamber, remaining instead in the Class 10ęŻ area. Should there be a jam inside the Class 100 chamber, side panels of the chamber can be opened so an operator can reach inside and clear the problem. As long as the operator doesn’t touch the filling valves themselves, the overpressured air will prevent contamination and maintain aseptic conditions.
Closure sterilizer
Mounted on top of the Class 100 chamber is the closure sterilizer. Like the bottles, the closures are sterilized by immersion in a hydrogen peroxide bath. Then the closures are rinsed with sterile water and passed to a closure-transfer track in a tunnel filled with sterilized air. The closure transfer-track leads the closures down to the newly filled bottles. Each bottle picks up a closure as bottles are conveyed beneath the closure transfer track. Then a 22-spindle capper torques the caps down.
Filled and capped, the bottles exit the Class 100 sterile chamber and the Class 10ęŻ room, as well. After labeling, an ink-jet coder marks the sidewall of each closure with a production date. Shelf life is six months, the same as it was with Eglisau’s previous filling technology. “But we’re testing to see if that can be extended,” says Boni. After a Krones Checkmat inspects for inaccurate fill levels and cocked caps, labeling and palletizing are all that remain.
With almost nine months of commercial production under their collective belt, the folks at Eglisau are confident they made the right move when they replaced in-bottle pasteurization with aseptic filling. “The taste [of the tea] is better because now the product is flash-pasteurized once instead of being pasteurized, bottled and pasteurized again,” says Boni.
Eglisau’s customer is equally pleased by the new technology.
“Aseptic filling gives us the opportunity to market high-quality, preservative-free Lipton Ice Tea in PET bottles,” says David Savage, technical director of Unilever’s Lipton Soft Drink Group. “We’ve seen a lot of development in this area, and we very much welcome and support these industry activities to develop high-speed, low-cost aseptic filling lines. It’s an important part of growing the iced-tea business.”