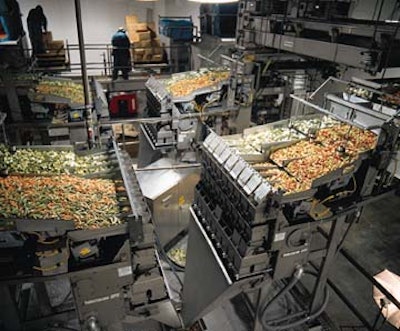
Contract packager National Custom Packing is reportedly the first to use an unusual turnkey “blending” line that can package up to nine different individually quick-frozen vegetables into a single bag sold at retail.
The integrated system, from Triangle Package Machinery (Chicago, IL), employs two of the vendor’s Selectacom Model 918 in-line combination scales that feed product to a single Triangle Advantage Model B2PR vertical form/fill/seal bagger. NCP uses two of these systems, operating side-by-side at the company’s new 20ęŻ sq’ facility in Castroville, CA.
The two systems began running last June, producing packs from 3 oz to 2 lb, at speeds of 70/min per system. The equipment runs on two daily shifts, five days/wk, producing about 60% of the company’s production, according to John Thornton, the contract packager’s president. The new Triangle systems are used for retail-bound IQF vegetable blends that might include broccoli, cauliflower, carrots, peppers, lima beans, etc.
NCP, along with sister company Central Cold Storage, are part of Castroville, CA-based Valley Packing Service. CCS operates a 200ęŻ sq’ refrigerated warehouse at the site.
Thornton admits, “There’s a risk in being the first” to use the equipment, “but we were very comfortable with what Triangle was developing. Parts of the technology have been field-tested and are doing fine. The thing our application does is take two 918s,” and pair them together with a bagger. NCP has other Triangle equipment operating at the plant, as well. The success of that equipment made it easier “being first” with the new system.
How it works
At the plant, temperatures are kept at 32°F to keep products frozen. Thornton explains that when more than four vegetables are filled into one bag, the vegetables are “preblended” on floor-level equipment. Conveyors and bucket elevators deliver these blends up to the “rear feeder” mounted above combination scales. The process works the same for both Triangle systems. Each weigh/feed vf/f/s system is PC-controlled.
Positioned next to one another at a mezzanine level, each 918 combination weigher at NCP is equipped with nine “lanes.” Each lane includes four buckets stacked vertically on top of one another. Product is timed to release from the buckets down through a discharge hopper. Two discharge hoppers, one from each 918, deliver product to the vf/f/s machine below.
“The unique part of the system is that the separate infeeds [bucket elevators] deliver product to the 918s,” says Thornton. “That means there are four separate products weighed for each 918. So, if we’re filling a 16-ounce package and want four different products in each bag, we might fill four ounces of broccoli and four ounces of cauliflower from one 918, and four ounces of carrots and four ounces of lima beans from the other 918.”
When eight or nine products are required for a single bag, they’re preblended so that two vegetables are fed from each bucket elevator infeed into each 918’s five-lane/four-lane configuration.
The computerized system times product to release from the top buckets to the second row where product is weighed. Product is released downward into the third and fourth buckets in each lane. These buckets are actually positioned in a front-and-back configuration. The computerized Triangle Selectech control system scans all chambers on both scales to provide numerous weighing combinations and precise weighment accuracy.
Product is filled into bags formed from rollstock on the Advantage vf/f/s machine. Film is formed around a collar, and a heat-seal is made on the back and bottom. Then product is filled, followed by heat-sealing the top of the bag while simultaneously forming the bottom seal for the next fill. Finally, the filled bag is cut from the web.
Retail and foodservice
Thornton explains that his company buys from a variety of film suppliers. “We run both printed and nonprinted films for different customers. Thicknesses range from two to six mils, but they’re usually 2 ?-mil low-density polyethylene.”
The filled pack is discharged onto a takeaway conveyor for case packing, palletization and stretch wrapping, all done manually. Pallets are stored in the Central Cold Storage warehouse prior to distribution by a common carrier throughout the U.S. Thornton reports that NCP’s customer base is “split 50-50 between retail and foodservice customers.” NCP does not sell any products under its own brand name.
Quick payback
Thornton says the system’s accuracy is superior to previous filling systems used by NCP “With the older volumetric blending systems we used, it would be kind of hit or miss if the exact amount of each product went into the bag. “For example,” he says, “if you wanted five percent of the mix to be red peppers, you might get less than that in one bag, more in another. With this system, the consumer always gets five percent of red peppers. We get consistent weights for each product so that the consumer gets exactly what he or she is buying. And we can better control our costs that way.”
Cost control is a key factor in determining NCP’s payback for the equipment. Thornton explains, “We expect payback on this equipment in less than two years.” Much of that payback is expected to come from reduced product giveaway.
“We’re experiencing less giveaway because of the equipment,” he states. “We’re talking about 40 million pounds of product that runs on this equipment, and we save a little better than one percent of that in giveaway. With this product costing about 75 cents a pound, [the equipment will] save us at least $300ęŻ a year.”
Besides the advantages of speed and reduced product giveway, the Triangle systems are expected to help NCP enter into a promising new product market. To date, NCP has used the new equipment solely for IQF vegetables, but that’s likely to change.
“The stir-fry business and home-meal replacement market is growing so rapidly,” Thornton explains. “There are manufacturers adding meats with vegetables, and that’s really what the equipment was built to handle. We’re working on developing contracts right now to pack frozen meat and vegetable mixes for these markets, and the Triangle equipment we now have in place is able to portion out the meats and vegetables in the right percentages.” So far, he reports, “the equipment is working better than I hoped it would.”