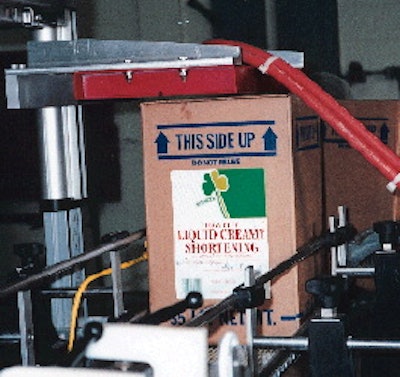
A supplier of shortenings margarines and edible oils to the foodservice industry Brighton CO-based Jensen Foods sought a way to add a tamper-evident inner seal to its 35-lb packs of edible oils. "Other companies seal their products so when customers received our products they wondered why they weren't sealed" explains Jay Edens plant supervisor. Jensen selected Enercon Industries (Menomonee Falls WI) to engineer a custom induction sealing solution since an off-the-shelf induction sealer couldn't be used with Jensen's jug-in-box package. The container is made of high-density polyethylene that's supported by a corrugated case. Jensen uses two sizes a 41/2-gal and 21/4-gal version. Foodservice workers in schools restaurants and hotels typically pour the oil from the package into a deep fryer. The challenge was that the closure and hence inner seal is recessed below the top of the box. (A die-cut in the top of the box permits access to the closure.) As a result a typical tunnel induction coil could not be used. The solution was a custom-engineered sealing head with special ferrites that direct the radio frequency energy down to the cap. The cap is a 63-mm deep-skirted polypropylene closure with Selig's (Oak Brook Terrace IL) standard film/foil inner seal wax-bonded to a pulp insert. The sealing head was also engineered to be flat to allow boxes to pass directly underneath. The coil is powered by Enercon's 2-kilowatt Red-e-System and the system enclosure and mobile cart are constructed of stainless steel that's suited to Jensen's washdown environment. After filling and capping containers pass under the induction sealer. Radio frequency from the induction sealer causes the foil to heat up. Heat from the foil softens the film causing it to adhere to the finish of the container. Containers are manually palletized then automatically shrink wrapped. Product is typically shipped within 24 hours. The induction sealer's small size permitted it to be easily integrated into the line. "That was important for us because of the small physical size of our facility" says Edens. Jensen packs its entire manufacturing operation into only 2 sq' of space though it ships 400 lb of product each week. The induction sealer has provided over a year of trouble-free operation according to Edens who is satisfied with its performance. "And in addition to providing tamper-evidence we've improved our image. It gives our customers more confidence in us."