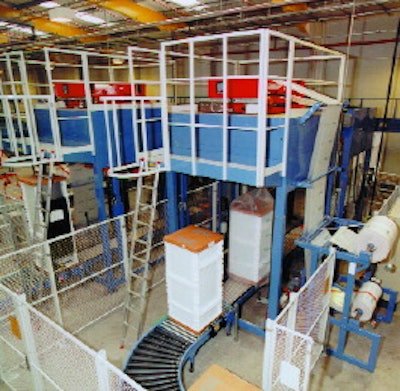
When LEC Refrigeration of Britain recently launched its Era line of refrigerators and freezers aimed at middle-market consumers, it was new territory for the firm. Traditionally, LEC had focused on the lower end of the domestic refrigeration market, where units top out at £300 (US$480) instead of £500 (US$800) like the new line. LEC is headquartered in the West Sussex town of Bognor Regis in England.
With the new products came a brand new $59 million plant in which to manufacture the line and a new way of packaging, as well: shrink wrap in place of corrugated.
"Packaging material cost is higher using shrink wrap compared to a plant where corrugated boxes are used," admits Ian Truin, LEC sales and marketing director. He declines to quantify the cost difference. "But," he continues, "damage is reduced with the shrink-wrap approach, and when these units are more costly to begin with, paying for added protection is a sound investment."
The reduction in damage is due partly to the simple fact that now the expensive white goods are always visible to whoever is handling them. When they're encased in corrugated, it's too easy for a fork lift driver to forget how susceptible to damage a freshly painted refrigerator side panel can be.
Obviously, mishandling can still occur. But when it does, LEC appreciates that it's visible through the shrink wrap. With corrugated, the potential for product with unseen damage reaching the consumer's home is always a concern.
High-volume throughput
LEC needed an automatic shrink-wrapping system capable of sustaining high-volume throughput. It met its requirements by installing two shrink-wrapping systems from KL Lachenmeier, a Danish firm represented in the U.S. by Global Marketing Management (Charlotte, NC). Each machine is capable of wrapping 150 units/hr, 24 hours/day. LEC's throughput is slightly less, but at 125 units/hr each, the combined capacity is everything LEC needed.
Equally important is packaging reliability. Any snafu at the end of the line would seriously undermine LEC's commitment to just-in-time delivery. As Truin puts it, "Getting it right at the end of the line was absolutely essential to fulfilling our promise to the market."
The two high-speed shrink-wrap lines, running since September '97, sit right beside each other at LEC's new plant. Refrigerators, freezers and fridge/freezer combinations come in nine different sizes and styles, and heights range from 58" to 78". Any one of the nine varieties can be wrapped by either of the two Lachenmeier machines. A photocell detects which of the two machines is unoccupied, and the powered roller conveyor diverts the unit to that wrapper.
By the time a finished unit reaches the wrappers, one packaging component is already in place. It's an end cap, made of corrugated and expanded polystyrene, on which the unit sits. Additional pieces added by hand include four EPS corner posts that lock into the bottom end cap, EPS cross members that interlock into the corner posts and a corrugated/EPS top cap that also interlocks with the corner posts.
Shrink wrapping is done in two stages. In the first, 75-micron (3-mil) low-density polyethylene shrink film is drawn from a continuous gussetted tube wound on a roll. First, it's heat-sealed across the film direction so that a hood is formed, open on one end and sealed at the other. Then the hood is cut from the roll and drawn down over the refrigeration unit by a hood application frame. Only in the second stage is the material shrunk down tight.
Multitasking
The hood application frame accomplishes two tasks with each cycle. Pulling the premeasured hood of film down around the refrigeration unit is the obvious task. But at the same time it's covering one appliance, it's measuring the height of the next one. The system's programmable logic controller calculates how long the next hood should be. The PLC then signals the film feed and cutting mechanism to cut the next hood to that length.
A photocell/encoder combination assists the PLC in this process of film measurement. The photocell, mounted on the hood application frame, is aimed at the incoming unit. As the hood application frame strokes down to enclose the lead appliance, the photocell detects the top of the next one.
An encoder monitors the drive shaft powering the hood application frame. The encoder "counts" pulses from the time the hood applicator leaves its home position to when the photocell detects the top of the next unit, relaying this information to the system's PLC. In turn, the PLC converts this into the correct height and signals the heat seal and cut-off station.
Once the hood is in place, the appliance is conveyed out to the next station, where film shrinking is done. First a lifting device elevates the appliance's pallet. The bottom shrinking fan draws the air out of the hood, and the bottom 10 cm (10")of the hood is drawn underneath the pallet. The pallet is then lowered again so that the bottom of the hood is trapped between the pallet and the conveyor.
At the same time, the shrink frame is lowered until it reaches the bottom of the pallet. Gas burners ignite on all four sides of the shrink frame, and it begins to stroke back up so that shrinking begins at the bottom of the pallet. Gas is consumed only during the few seconds that shrinking takes place. When the shrink frame reaches its home position overhead, the burners switch off and the finished pallet is discharged.
The system's ability to rapidly and automatically switch from one appliance height to another means that it can accommodate new models that might be developed in the future. As for LEC's sales and marketing director Truin, he likes what the new machines are doing in the present.
"We have increased the value and quality of the LEC range, and consumers can now expect wrapping that reflects the status of their purchase," says Truin.
Equally pleased with the wrapping operation is LEC project manager Jim Catt. "KL Lachenmeier listened to us and thought through the solution in every possible detail," says Catt. "Their machines are well-built and their support is first class."