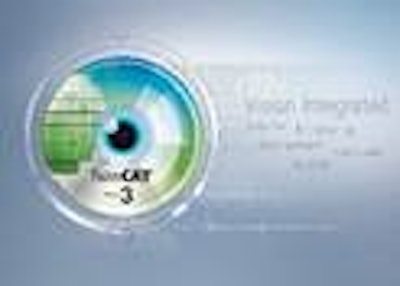
With this level of integration, TwinCATVision eliminates the need for separate vision solutions, often developed by third parties. The software opens up vast innovation potential in machine building, for instance, through consistent real-time synchronization with other automation tasks or support of advanced track-and-trace solutions.
TwinCAT Vision provides the required image processing capabilities in the form of PLC functionality on a universal, end-to-end software platform, complete with a specially developed library of image processing functions and function blocks that are called up directly from the PLC. The flexible runtime system in TwinCAT is capable of executing these functions and function blocks in real time. Integration at this level simplifies engineering significantly, so that PLC programmers can now create machine vision applications themselves without support from outside experts.
GigE Vision compliant cameras of almost any kind are added easily, even in parallel, via standard camera interfaces and configured in TwinCAT Engineering. The cameras can also be calibrated directly, in the engineering environment or mid-process in the runtime system. With TwinCAT Vision, there is no need for specialized tools or programming languages when coding the image processing logic, because the machine vision applications are created in the PLC, using familiar PLC programming languages.