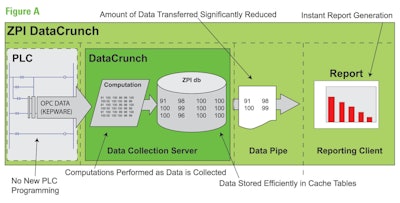
It would certainly appear that the folks at Campbell Soup Co. are firm believers in the old saying that you can’t improve what you can’t measure. They’ve spent about 13 years using and optimizing an automated downtime data collection and review system from ZPI called Enterprise Manufacturing Diagnostics. More recently, they installed Wonderware IntelaTrac from Invensys Operations Management, a centralized mobile workforce and decision support system that greatly improves management of workflow, productivity, and data collection. Wielding these plant intelligence solutions, the firm has maximized real-time visibility into the performance of its manufacturing assets.
Let’s look first at Campbell’s automated data collection and analysis system. According to Campbell’s director of controls and maintenance systems engineering Tom Braydich, it was clear a long time ago that manually capturing performance data on a clip board and sharing that information many days later was an approach that had outlived its usefulness. Some electronic solution was clearly needed. Unfortunately, each plant began searching for its own electronic solution. From a corporate standpoint, this was not a good thing.
“The last thing we wanted was nine different ways of accomplishing the same thing,” says Braydich. “We wanted a common solution that was off the shelf software, not custom. So we brought together people from operations, industrial engineering, IT, and engineering. We asked them to give us the names of vendors who might have what we were looking for.”
This led to a list of seven candidates that was pretty quickly whittled to three. Braydich continues.
“We told the three that we weren’t going to pay them anything but we wanted them to install their product on one of our lines so we could see how well it met our needs. Among the things we monitored closely was how much time they spent in the plant actually getting it up and running. We also measured network traffic, because when you start doing electronic systems you notice how much network draw there is. We watched, too, to see if they had to modify existing PLC programs in our machines. And we wanted to see how invasive their software really was, in other words, could it really get into the PLCs and get the data and give us reports on a screen that we could use. All three of these firms were each asked to do the same line. It was a can line, from filling all the way down to palletizing.”
And the winner is
At the end it was ZPI that was selected. Very appealing was the fact that they were able to install their software without even leaving their offices in Canada. “Also, there were no modifications needed to our PLC or HMI programs running in our plant,” says Braydich. “They satisfied all the criteria of the RFQ.”
Braydich also emphasizes the importance of the software being universal, lightweight, and useful enterprise-wide. By universal he means it can be easily deployed in any Campbell plant around the world regardless of whether the product being made is soup, juice, bread, cookies, or crackers. By lightweight he means that it did not require the layering on of additional code to the plant PLCs. And by useful enterprise-wide, he means he wants to be able to quickly view, from the comfort of his office in New Jersey, a plant anywhere in the Campbell Soup system. “I didn’t want to have to get special permission from the plant, or need some kind of access tool, in order to view the data,” says Braydich.
Finally, the software had to know how to play nice with others. “We didn’t want to be stuck with something that only worked well with PLCs from Brand X or Brand Y,” says Braydich.
As the ZPI software was installed in one plant and then started going out into others, one of the training challenges that had to be dealt with was the tendency for operations people to view it as some kind of goose laying golden eggs. They had to be reminded that software doesn’t fix things. It reveals things that people need to address before anything gets fixed. Once this initial hurdle was overcome, plant personnel began to embrace the tool, and in short order it was operating in all nine Campbell plants.
According to Braydich, the software has increased productivity by about one can per minute per SKU. Looked at another way, it has generated a 20% IRR (Internal Rate of Return), which is right about what ZPI projected in the early days of implementation.
How it works
What ZPI’s software does is crunch data (see Figure A). It connects to the PLCs in a plant via a KEPServerEX communications platform from Kepware. The OPC-compliant Kepware software goes out to the PLCs in the plant, each of which has unique addresses associated with counters, alarms, faults, etc. The software captures data from these addresses and sends it to the ZPI historian.
The KEPServerEX software manages all communication and data manipulation through a single-server platform. This not only helps ensure reliable data, it also minimizes network traffic, data inconsistencies, and device and system resource usage. It’s also notable for its plug-in architecture. Users can add device drivers or client drivers on demand, making it truly scalable.
Braydich is a big fan of the Kepware solution. “With an earlier communications platform we had running, we encountered too much missing data,” he says. “The Kepware platform gives us a much smoother connection between the PLCs and the ZPI data crunch.”
The data collected via the Kepware platform goes next to the ZPI data base, but first a considerable amount of computation takes place. This is a departure from comparable systems.
“We do some of the heavy lifting before putting the data into the data base,” says Chris Hough, senior director of client development at ZPI. “We break down the data and put it in different tables in the data base. We also make good use of caching, a memory tool to store data efficiently in cache tables inside the data base. That’s important because when you’re pulling reports, if you’re pulling them with a traditional historian it has to do a lot of computational work every time you run a report. By us doing a lot of computational work on the front end, when you go to pull a report, not as much ‘thinking’ has to take place. You’re not sending as much data over the network.”
Quick response
The beneficiary of this technology, of course, is Campbell Soup Co. “The way data is stored makes for easy retrieval, so when you actually do run a query against it, the response is very quick,” says Braydich. Delivery of reports are web-based for operators on the plant floor. For Braydich and others at the supervisory level, access is through the Wide Area Network (WAN), so they have much broader capabilities. They can pick any line in the plant and look at line performance or individual machine performance. They can draw comparisons among lines’ performances, recalculate speeds after changeover to a new SKU, or generate trending reports to compare whole shifts.
Real-time production dashboards displaying machine or line conditions are a key deliverable that Campbell gains from the ZPI software. These have evolved somewhat, says Braydich.
“Earlier on we configured them on a per-line basis. But we realized we also needed a broader look that was more supervisory in nature, so that a supervisor could be sitting at his desk and in one glance or on one dashboard he could see how all the lines are running. Efficiencies, most recent major stop, most recent minor stop, mean time between failure, mean time between repairs—all of it is visible at a glance.”
Other benefits gained through the automated data collection system include improved Overall Equipment Effectiveness and better new-project planning and execution. As Braydich puts it, “Hardcore data trumps hearsay any day.”
One last observation on data acquisition software that Braydich offers revolves around ownership. “It’s important to decide upfront who owns it. Some say, ‘It’s software, so IT owns it.’ Others might say ‘It’s all that engineering stuff, so Engineering owns it.’ My preference is to have someone from Industrial Engineering take ownership because a lot of the information being gathered is for new projects, improvements to the line, enhancements to operations, and planning.”
Going mobile
Moving now to Campbell’s adoption of IntelaTrac software and the mobile hand-held computers that feed into it, the goal was pretty much the same as it was with automated data acquisition: replace a paper-based version with an electronic one so that operating parameters can be monitored and adhered to in real time rather than after a lengthy delay. A secondary goal was to cut down on paper.
“We used to generate a lot of paper,” says Braydich. “Between vision inspections, quality samples, HACCP reports, safety checks—you get the idea. And it all has to be reviewed at the end of the day.” He estimates that some 1,200 pages of paper per line have been eliminated annually since the IntelaTrac solution was implemented.
According to Braydich, it all started with a meeting Campbell had with Microsoft and Invensys where ways of improving TPM (Total Preventive Maintenance) were explored. “They asked us about tasks we do in our plants where they might have a hardware or software solution that could be applied. When we mentioned our need for better centerlining and improved autonomous maintenance, that caught their attention. They said that if we bought the InteleTrac software and handheld devices sufficient for one line, they’d do all the integration required on the line and show us how well it worked. We agreed, and ever since we’ve been buying additional handhelds and putting the solution on additional lines.” He estimates that if a plant has five lines, that plant will have about 20 handheld devices. These can come from a number of vendors.
Centerlining, which Braydich defines as a statistical means of keeping machinery operating within optimal parameters, has been greatly improved. Operators and technicians used to receive machine setup parameters on paper and confirm their execution of the setup on the same piece of paper. If a machine’s parameters had to be modified due to, say, a worn machine part or a batch of out-of-spec corrugated trays, these modifications were also noted on paper. Eventually all this information would make its way to an Excel spread sheet so that, eventually, it could be used as a tool to help keep machines as close as possible to true centerline parameters. In reality, as Braydich points out, these paper-based records of operating parameters too often wound up in somebody’s desk drawer where they didn’t do much good at all.
Now the paper documents have been replaced by handheld computers. Operators read setup and changeover parameters from the screen on these mobile devices, and on the same screen the operators record whatever actions they’ve taken. All this information flows immediately into a data base where it can be trended and alarmed—without long delays inherent in a paper-based system.
It’s not just at setup or changeover that the mobile device comes into play. It’s used to monitor machine parameters on an ongoing basis, which makes it a valuable tool in keeping machines centerlined.
Engaging the operator
Autonomous maintenance—defined as maintenance performed routinely by machine operators rather than the maintenance staff—has also been greatly improved. “We wanted to get the production operators more involved in what’s going on out on the plant floor and free up our maintenance people to spend more time doing highly demanding maintenance tasks as opposed to checking for a leaky gear box or a loose chain,” says Braydich. “The mobile devices help in this regard because they let a supervisor message an operator directly if, for example, a certain feed belt’s tension should be checked. There’s no need for the operator to retrieve a piece of paper or find an HMI screen or laptop to receive this message from the supervisor.”
Braydich says that Campbell’s use of wireless handhelds might not have been possible a few years ago. “The reliability of wireless connectivity has gotten so much better,” he points out. “The wireless network infrastructure operating in our facilities was put in for our SAP Enterprise Resource Planning system, not for the purpose of optimizing manufacturing through wireless handhelds. Fortunately, the IntelaTrac solution was able to piggyback on that infrastructure, so we were able to leverage it and gain additional functionality.”
Braydich envisions that one day, Preventive Maintenance tasks will be communicated automatically to Campbell’s mobile workforce via their handheld devices. “All the PMs to be executed are stored in the PM module of our ERP,” he explains. “Why not have the PM requirements flow automatically from ERP to the mobile devices carried by maintenance personnel and technicians? They could execute the whole PM and then update the ERP system on the handheld so that the ERP could then automatically schedule the next PM.”
It’s functionality like this that has made Braydich such a big believer in the power of mobile workforce support technology.