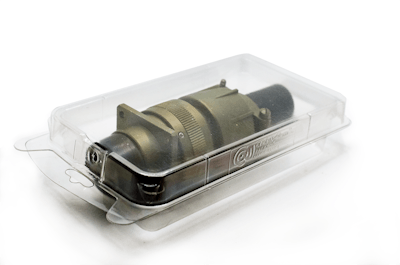
Offering more than 7 million SKUs, Swedesboro, N.J.-based Powell Electronics is among the largest distributors of custom-made electronic components and value-added services. Its products include electronic connectors, switches, sensors, and related electromechanical products—all of which are very sensitive parts with extremely delicate handling requirements.
According to company CEO Ernie Schilling Jr., for more than 20 years, Powell searched without success for a protective packaging solution for its fragile parts, experimenting with a number of different packaging materials and formats. But a chance encounter with custom plastics supplier Jamestown Plastics at a sporting goods show several years ago resulted in Schilling finding the ideal packaging solution for the company’s needs, a patented reusable and recyclable clamshell container, the Clamtainer, which he says just “clicked.” He adds, “I immediately saw that the Clamtainer solved our issue.”
Clamshell uses ‘the deadbolt’ approach
Powell Electronics is a national company with global distribution and represents nearly 150 manufacturers. The company employs a staff of over 200 people at 11 U.S. locations, supplying industries that include the military/aerospace, telecommunications, transportation, medical imaging and instrumentation, and the U.S. government, among others. Products are delivered to these customers in shipping cases with the components individually packaged. According to Schilling, the parts are inspected at both shipping and receiving and are oftentimes stored for many years, as in the case of military preparedness, or are sent to third-party contract manufacturers.
For years, Powell experienced damage of its parts during shipping in the form of bent pins, or contacts, and loose parts when the packaging failed to remain closed or maintain its structure. “Parts were splashed in the larger shipping box,” says Schilling. “Because each connector is custom, and we support over 7 million SKUs, the dimensions [of the packaging] were almost impossible to match perfectly every time. It was an enormous undertaking to match a part to a shipping container without advance forecasts or estimates. We received over 1,500 returns per year due to bent pins or failed packaging. What was so offensive is that the returns were for dollars against tens of thousands of dollars but had the effect of killing our quality rating with our customers.”
![]() | Check out this column from Sterling Anthony, “Advice About Vacuum Thermoformed Packaging.” |
To address the damage, Powell tried multiple paperboard cartons, however there were strength issues as well as inspection issues, as operators had to open the cartons at shipping and receiving to inspect the parts. The company also tried various polypropylene films stretched over paperboard as well as vacuum packaging and trays. “All lacked the flexibility and universal ‘adaptability’ of the Clamtainer,” Schilling reports.
According to Jamestown Plastics CEO and inventor of the Clamtainer Jay Baker, the patented clamshell container is the only one of its kind that is sold as a standalone product to consumers, in addition to being supplied to brand owners as a packaging solution. Part of its appeal to both is its sustainability features. “We like to say of the motto, ‘reduce, reuse, recycle,’ that there has never been a clamshell application that hits on all three of those more resoundingly than the Clamtainer,” Baker says.
The bulk of the Clamtainers produced by Jamestown are 100% recycled-content and 100% recyclable PET. The container can also be made from BioPET—a blend of bio-based and petroleum-based plastics—ocean-bound rPET, recycled polyvinyl chloride (rPVC), and plant-based polylactic acid (PLA). According to Jamestown, the Clamtainer uses less plastic than traditional clamshell packaging, which means less space is needed in trucks and distribution centers, and shipping costs are decreased due to reduced dimensional weight.
One of the aspects of the Clamtainer that most differentiates it from the traditional clamshell, however, is its patented Click-It Closure. As Baker explains, the core of the invention is a post and hole mechanism, positioned inside the Clamtainer on the vertical side. Called the “Click-it” due to the clicking sound it makes when it’s closed, the locking mechanism involves snapping the post into the hole—an action that can be done with one hand and allows for reclosure, making the container reusable.
“I’ve done a lot of demonstrations at trade shows of the Click-it Closure,” says Baker. “I use this analogy: I say, ‘Okay, so when you go to bed at night, do you close your door, get out a nail and a hammer, and drive a nail through your door into your door jamb, and then pry it back out again the next morning? Or do you use a deadbolt? Well, the Click-It Closure mechanism is the deadbolt solution in the Clamtainer space. Everything else is a version of a nail and a hammer.’
The Click-it Closure locking mechanism is positioned inside the container on the vertical walls of the clamshell.
“In order for the Clamtainer to fail, you either have to shear the pin off or you have to tear through the sidewall, where the hole is, which takes an incredible amount of force. It’s really surprising. And the other unique thing about the closing mechanism that makes it so resistant to opening when it’s dropped is that the forces that are blowing open that blueberry container are pushing that hole—because it’s on the side of the container not on the lid—harder against the pin. So the forces are working somewhat in your favor as you compress it, because it’s pushing against the pin, it’s not pushing the pin away from the container.”
Another notable advantage with the Clamtainer, Baker adds, is that the first step in packaging is the last. Meaning, once an operator places the product into the container and snaps it closed, the packaging process is complete. No additional tools or sealing operations are required, which he says results in “incredible efficiencies.”
Clamtainer implementation reduces costs, damages
After being introduced to the Clamtainer, Powell Electronics began testing the packaging in 2019, expanding every year to include additional sizes and material types to accommodate parts valued over $1,000, as well as low-cost parts. “The goal was to use the Clamtainer technology on everything, we just needed to calibrate the material costs and dimensions,” says Schilling.
For Powell’s massive and varied assortment of SKUs, Jamestown custom designed a number of Clamtainers to hold the company’s highest-volume products. Powell is also using a number of stock square and rectangular containers. Explains Baker, to optimize the range of containers used by a company, Jamestown will either use the company’s actual products or its CAD files to find commonalities in sizes and then create groupings. “So that’s what we did with Powell,” he says, “and the project was relatively straightforward.”
![]() | Read how Pentel is reimagining blister packs as plastic-free. |
Schilling explains that Powell’s warehouse operators use a decision tree to select the right-size container. “Before we were hybridizing and collaging the original factory packaging with tape and cardboard to craft thousands of semi-unique packages, all in an attempt to preserve the parts,” he says. “Now we access the value of the part on the pack list and choose a corresponding Clamtainer to meet the part and size.”
Among the advantages of the Clamtainer is that warehouse staff can now inspect the part after the packaging process, as the container is clear, which means Powell no longer needs a more expensive Quality Control staff.
“But the real savings is in time to package and the elimination of the quality returns,” says Schilling. “The previous packaging had assembly required and other soft costs. With the Clamtainer, parts pullers are now able to pull products 10-times faster, while the personnel used to do the final packaging are ‘exponentially less expensive.’
“The Clamtainer eliminates all the soft costs and is comparably priced to the box, plastic, and foam alternatives. The Clamtainer-ized materials can also travel through all of our automated carriers without fail.”
The Clamtainers are sized to securely hold Powell Electronics’ parts, protecting the pins, or contacts, on the parts from damage.
In terms of the package’s ability to be reused, Schilling says one of the best potential applications for the Clamtainer is its ability to be incorporated into a system for factory automation, expanded packaging, and secondary uses. “It offers our customers the ability to forward parts to third-party assemblies, contract assemblers, and end customers,” he says. “They need not repackage them.”
Since launching the new packaging, Schilling says no news has been good news. “We wanted no customer response, RMA [return merchandise authorization] reduction to zero was our goal,” he says. “What has been fantastic is the corrective action process on requested returns. It has virtually eliminated RMAs from bent pins, and when they are requested, we are able to vet the return for root cause … customer, third party, etc. We win every packaging debate, and the root cause is most often attributed to the customer’s internal handling.” PW