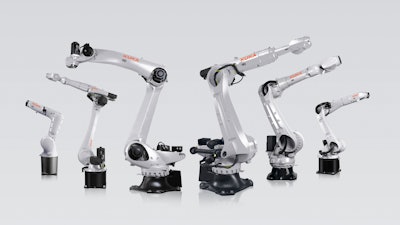
This content was written and submitted by the supplier. It has only been modified to comply with this publication’s space and style.
With the utmost cleanliness and safety in mind, KUKA has expanded its robotic portfolio with the addition of Hygienic Machines (HM) and Hygienic Oil (HO) robots. This wide array of products allows today’s food processing companies to apply robots to tasks considered difficult, if not impossible, to automate.
KUKA’s HM portfolio includes robots such as the AGILUS HM and others, all of which feature corrosion resistant surfaces like stainless steel flanges and other key components. Robot arms use food-compatible lubricants in all axes and have smooth surfaces for easy cleaning, this is where KUKA’s HO portfolio comes into play.
For fully automated palletizing/depalletizing, KUKA will demonstrate its KR IONTEC medium payload robot mated with a robotic pick-and-place solution. The KR IONTEC, a highly flexible robot with the best work envelope in its class, will be integrated with 3D-vision to detect stationary items with rectangular surfaces and determine their position, orientation and size for picking. Once the box locations are identified, the KR IONTEC, which is suitable for a vast array of industrial applications including handling, packing and palletizing, will complete the next pick action for fast, efficient stacking.
Designed to simulate a real production environment and automation solutions for each step – moving material from receiving and sorting to packing and distribution – the KUKA end-to-end automation cell will include the company’s KR 3 DELTA Hygienic robot, KR 6 SCARA and KR 6 AGILUS robots and KUKA.VisionTech advanced vision software. The KR 3 DELTA hygienic robot provides outstanding performance and value for pick-and-place applications for the food, packaging, electronics and pharmaceutical industries, while the KR 6 SCARA is strong, fast, highly efficient and delivers maximum economy. KUKA will pair both robots with its KUKA.VisionTech.
KUKA’s six-axis KR 6 AGILUS adapts to any installation position and is designed for particularly high working speeds, boasts a 10-kg payload and comes in a wide range of variants for challenging applications such as clean rooms and potentially explosive environments. KUKA’S KMR iiwa that combines the sensitive KUKA LBR iiwa lightweight cobot with a mobile, flexible platform will work with the three cell-based robots and complete the fully automated end-to-end solution.
As with all the company’s automation solutions, those that will be shown at Pack Expo are backed by KUKA’s expert service and support for training, complete system engineering and simulation, readily available spare parts, robot refurbishment and more. All of which are easily accessible through the my.KUKA.com site, and KUKA maintains corporate offices and production operations, along with integration partner facilities, conveniently located throughout North America to provide responsive customer service and support.