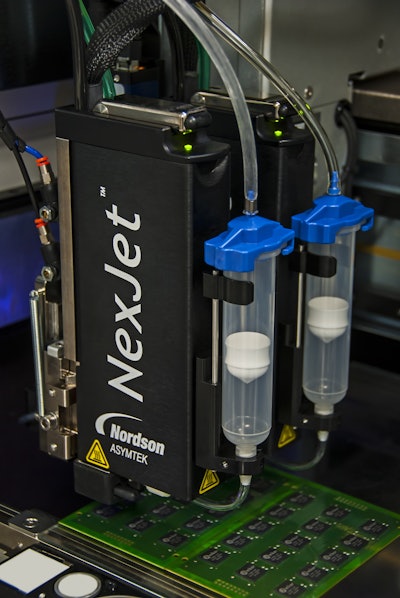
This content was written and submitted by the supplier. It has only been modified to comply with this publication’s space and style.
This high-volume system's multitasking capabilities can increase throughput by 60 to 85 percent for flip-chip underfill, chip encapsulation, and thermal compound applications.
Dual-action dispensing enables dispensing of two fluids with a combination of jet and/or valves operating independently. This saves steps and time in applications that require two different materials to be dispensed on the same part, such as dam and fill encapsulation and hybrid applications that require both conductive and non-conductive die attach epoxy. Dual-action dispensing is also recommended for high-mix production when several product types are manufactured during the same shift.
When flow-out times are longer than the time to dispense all first-pass lines, a single lane dispenser loses valuable production time. The Spectrum S-922N dual-lane system allows parallel processing on two lanes for continuous dispensing, eliminating lost time in non-dispensing activities such as material flow-out and substrate loading/unloading. It also suits applications with high heat requirements or long pre-heat cycles. Dispensing can be done in one lane while substrates reach temperature set-point in the second lane. The system is configured with up to six stations of heat, three stations per lane. The six heat stations ensure precise and consistent substrate heating at specified ramp rates for efficient and highly reliable dispensing.