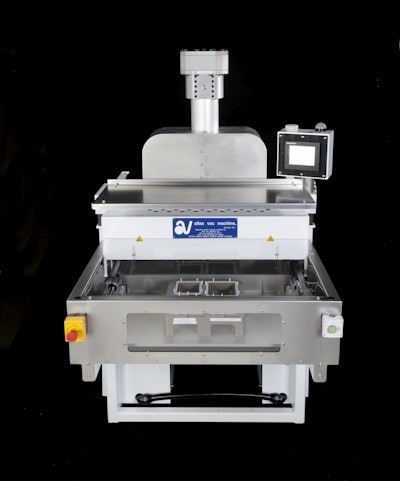
The tray sealer’s down-force “signature curve” reaches full down-force application quickly and is held extremely constant throughout the entire dwell time setting. In addition, higher forces are attainable with new servo-driven models allowing more sealing tool nest area to be utilized per stroke.
The electric press medical tray sealer is designed for precision packaging that requires validation of package sealing protocols to ensure package aesthetics and integrity.
Productivity is increased by up to 33% with this new all electric sealer design because the operator can engage the entire sealing cycle with the push of a button rather than having both hands on the safety sensors. This allows the operator to stage the next package set while the auto shuttle moves and the press is engaging. Safety is ensured through the light curtain system, which automatically detects any interference within it—ceasing press and shuttle motion until the unit is reset.
An optional electric auto shuttle is smooth, precise, repeatable, and fast. This auto shuttle system eliminates ergonomic issues and is standard equipment on the new all electric tray sealer.
The smooth shuttle motion can never be placed out of adjustment by operators attempting to “dial it in” as they do with pneumatic versions. The new electric press and shuttle eliminates the need for compressed air which can be an expensive utility not always in adequate supply.
Direct force control is achieved by a servo drive system in which forces are monitored and controlled using a direct measurement feedback loop.
Heavy-duty components like 1² diameter linear bearing rods are said to produce the heaviest equipment on a per-square-inch of sealing platen area. Because structural integrity and rigidity are the keys to successful sealing, stationary components remain aligned while moving components glide smoothly.
A heavy heater section and a Teflon coated seal platen provide sufficient mass to distribute the thermal energy evenly without hot spots or wide fluctuations in surface temperature even in high package cycling.
PLC controls are available from Mitsubishi or Allen Bradley, with validation protocols, recipes, passwords, operator screens, alarms, data acquisition and other tools available in standard or custom configurations. CE certification is always available for machines designated for EU markets.