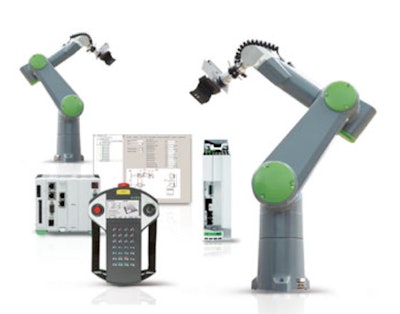
The general principle of this new feature is to pick & place the highest number of products per minute, while at the same time only moving as fast as necessary. This means using vision systems, advanced algorithms, and multi-robot control to look at products moving down a conveyor belt, take into account the position and workspace of each robot, and intelligently plan the movement of each robot to maximize productivity and minimize mechanical stress on the system.
Foreign objects are now included in the path planning, which includes other robots and products moving on a conveyor belt. “Look Ahead Path Planning” enables the KeMotion system to automatically react to upcoming events and use the most intelligent strategy to increase productivity. This feature is designed to be easy to use without the need for additional programming.
KAIRO, the easy to use robot programming environment from KEBA, is interpreted online in the KeMotion control system. Up to 30 program lines are planned in advance, which means the control system can say exactly where a robot will be seconds before its tool center point actually reaches the position. In addition, speed and acceleration are taken into account to avoid undesired peaks in the dynamic process of individual robot axes. Any changes in motion paths required for external events, such as machine stopping or tracking, takes place in the interpolation cycle.
“Look Ahead Path Planning” enhances this already sophisticated planning by taking into account foreign objects, such as other robots and products on a conveyor belt. Higher productivity with less mechanical stress and less energy consumption are achieved as a result of integrating the timing of these foreign objects into the path planning.