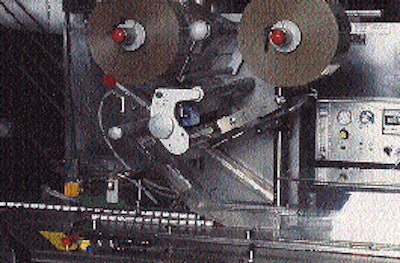
To switch rollstock or to replace the forming box, Saputo doesn't even need hand tools. And the programmable controller automatically sets up the machine for size changes. "No tools are required even to replace the forming box," says George Znoj, senior project engineer. "Just four knobs hold the forming box in place, and they are hand-tightened and loosened. Plus quick-release levers on the film reels permit easy loading and unloading of film rolls. The repeat length is programmed in so the machine automatically sets up for cutting on the right index length." This is critical at Saputo because the machine may run as many as 10 to 12 different labels per shift, says Znoj. Overall, he says, this wrapper can be changed over in five to ten minutes because film threading is easy, as is adjusting the film angle on unwind that's necessary when sizes are changed. If quick changeover helps minimize downtime, so do some of the other machine features. Individual temperature controls on the seal jaws and controls on the gas flow will trigger alarms or shut off the machine when readings are out of spec. If product feeding misses a flight, the machine senses it and doesn't cycle the wrapper. There is also a sensor that reads a misaligned product. Despite all the features that minimize downtime built into the wrapper, this machine isn't a new challenge to the Saputo operators or maintenance staff. "Certainly there are other machines that offer a lot of features," says Lino Saputo, Jr. "But you'd need to send operators for advanced degrees to learn how to use them. That's not the case with this machine." c