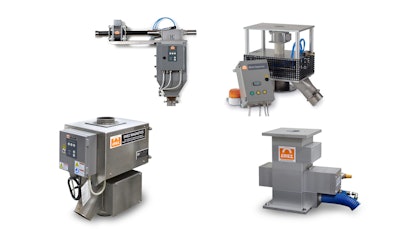
This content was written and submitted by the supplier. It has only been modified to comply with this publication’s space and style.
This equipment can be positioned in various locations throughout the process—from bulk or raw material unloading through final package inspection—to safeguard against dangerous metal contamination.
The CF Press and Extruder Mounted Metal Separator is installed directly above the material feed throat of an extruder, injection molding or blow molding machine.It provides precise detection and removal of aluminum, brass, copper, mild steel, stainless steel and other metal contaminants from a slow, downward-moving column of material. Its robust, heavy-duty design allows material feed systems to be mounted directly on top of the metal separation unit. This equipment functions well with high levels of regrind and larger size recycled plastic materials.
TheCFP Press and Extruder Mounted Metal Separator is installed directly above the material feed throat of an extruder, injection molding or blow molding machine. It provides high sensitivity detection and removal of aluminum, brass, copper, mild steel, stainless steel and other metal contaminants from a slow, downward-moving column of material. Its design allows material feed systems to be mounted directly on top of the metal separation unit. The air activated slide and evacuation venturi assures the complete removal of metal contaminants. It is best suited for virgin materials with less than 15 percent regrind.
The FF Gravity Flow Metal Separator is used to detect and reject metal contaminants under free-fall conditions. It detects and removes aluminum, brass, copper, mild steel, stainless steel and other metal contaminants--even when it is encapsulated in plastic pellets or shredded rubber. The reject mechanism can be rotated 360 degrees for operational flexibility. It is available in transit pipe sizes ranging from 1.2 inches to 9.8 inches.
ThePN Pneumatic and Vacuum Metal Separator removes aluminum, brass, copper, mild steel, stainless steel and other metal contaminants--even when it is encapsulated in plastic pellets. A specially designed quick reject mechanism operates effectively at vacuum or pressure conveying speeds up to 3936 fpm and 29 psi, without any interruption to the material flow. The reject mechanism operates rapidly to minimize the loss of good material. Contaminated material is discharged into a reject container that is emptied automatically.