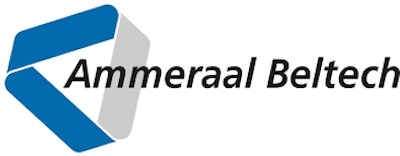
This content was written and submitted by the supplier. It has only been modified to comply with this publication’s space and style.
Ammeraal Beltech, a global provider of conveyor belting solutions and a brand of AMMEGA Group, will showcase efficient, safe and customizable belting solutions at PACK EXPO International 2024 (November 3-6) Booth S-3076. Ammeraal Beltech is designing belts to meet the demands of smarter, faster, and highly precise operations. With an established reputation for developing innovative and customizable solutions for various applications, Ammeraal Beltech is the leading manufacturer of process and conveyor belting.
“As manufacturers look to improve efficiency, lower costs, and reduce the physical demands on warehouse employees, these needs also translate to conveying equipment. Our goal is to continually support manufacturers, including startups and smaller emerging brands, with solutions to advance their business,’’ said Niels van den Boogert, Vice President/General Manager, Conveying Solutions, at AMMEGA.
In the high-speed, high-precision, and often harsh environments of today’s increasingly sophisticated warehouses, any equipment failure doesn’t just result in unexpected maintenance downtime but potential danger to the facility and operators. These operations demand belt attributes like superior material strength, friction resistance, and impact resistance. Manufacturers need to ensure worker convenience and implement solutions tailored to reduce physical strain associated with workplace injuries and lost time. This also includes low-noise solutions which can help to minimize noise pollution and the need for uncomfortable hearing protection. The Ammeraal Beltech team will be showcasing a variety of solutions at this year’s PACK EXPO International designed to address these concerns, such as:
- uni Direct Drive Spiral System™ – The patented design of the uni Direct Drive System delivers the smoothest unforced engagement in the market. It ensures consistent operation, even in the most challenging environments. As the uni Direct Drive System is positive driven, it operates with greatly reduced belt tension. This increases belt life and reduces sensitivity to environmental factors such as ice buildup, grease and contamination. It reduces maintenance, cleaning associated with friction issues, and technical adjustments. Partners benefit from the extensive knowledge of our US and Global Spiral Belt Support Team, who are on hand to assist with the design of your Direct Drive System Spiral.
- uni 253 and 255 – the new side-flexing conveyor chain – is important news for the bakery, beverage, and glass container manufacturing industries. This chain belt was recently released to expand the uni modular chain product line to address multiple industry needs. In bottling, where higher speeds mean faster wear, the thicker top plate will outlast traditional slat top chain, while also providing a smoother surface to minimize product loss during production. In bakery, the thicker top plate provides a longer lifetime of the chain belt when contacting heavy metal pans. The plastic or nylon belt chain will also provide less wear on the pans mitigating pan replacement costs compared to stainless steel chain.
- Uni ITB (Industrial Thick Belt) – AMMEGA will showcase the latest addition to its modular belting lineup. This belt can withstand abrasive environments where wear and impact resistance are crucial for productivity and streamlined operations.
- Green Belting – Quality tapes, fabrics and belts, dedicated to meeting the ever-changing demands of the industry. The solution-driven products are designed to improve processes, reduce costs, and improve bottom line.
- ZipLink® – Belts with easy to install features, eliminate the need for specialized labor and support, resulting in better efficiency. ZipLink is an ultimate solution for costly machine downtime across a variety of industries, including food and beverage. Ziplink belts provide customers with easy to install features that eliminate the need for specialized labor and external support, resulting in better efficiency. The belt no splice area provides a more ideal environment for production speed increase. Additional benefits include no extra thickness spots or metal parts that have the potential to damage machinery and products. Additionally, it can be customized with a variety of top-cover materials to best suit manufacturers’ needs.
- RAPPLON® brand of High-Performance Flat Belts – A proven solution since 1957, these belts are known for their quality and precision.
- Ammeral Beltech’s coating solutions can be made of various materials that influence the suitability of belts across different applications.
Ammeraal Beltech designs conveying solutions that are “Built American Proud” in keeping with AMMEGA Group’s commitment to become the belting partner of choice. Ammeraal Beltech sources American-made materials, employs local experts, and locally manufactures belts for U.S. customers. “We pride ourselves in being a one-stop belt shop and our solutions are high-quality, reliable, and brought to American customers quickly through a sustainable supply chain,” said Boogert.
Meet Ammeraal Beltech’s experienced team at PACK EXPO International 2024—Booth S-3076–to learn more.