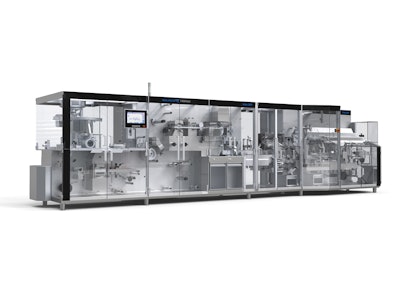
This content was written and submitted by the supplier. It has only been modified to comply with this publication’s space and style.
At interpack, Romaco’s comprehensive portfolio of services are on show, including selected digital tools, such as the service app, e-learning programs and the web-based BlisterMagic platform, and six laboratories for granulation, tableting, film coating, filling, and packing.
The spotlight will be on the Romaco Noack new Unity 600 blister packaging line, which combines high efficiency with a sustainable system concept. The double-lane, high-speed line achieves a maximum output of 600 blisters and 350 cartons per min and enables flexible processing of blister packs up to 145 mm long and 90 mm wide.
Its innovative transfer system eliminates the need for conventional vacuum pumps, significantly improving the energy efficiency of the monobloc, which consists of a blister machine with rotary sealing and a continuous motion cartoner. The vacuum for transferring the blisters to the cartoner and for removing the cartons and leaflets is instead produced in a more climate-friendly Venturi process. Venturi pumps are comparatively small, need less maintenance, and give off much less heat, so the cooling requirements in the cleanroom are greatly reduced.
The blisters are transferred to the cartoner by a carousel-shaped indexing wheel with a downstream stack transfer unit, which ensures the cartoner is only supplied with complete blister stacks.
As a new feature, any gaps are mapped in the software and compensated. Since good blisters are no longer held back, a manual blister top-up magazine can be dispensed with. Furthermore, the highly automated transfer solution allows seamless tracking and tracing of the blisters from the product feeding unit onward.
Due to its good line clearance and short changeover times, the Romaco Noack flexible-format Unity 600 blister packaging line also scores with excellent overall equipment efficiency (OEE).