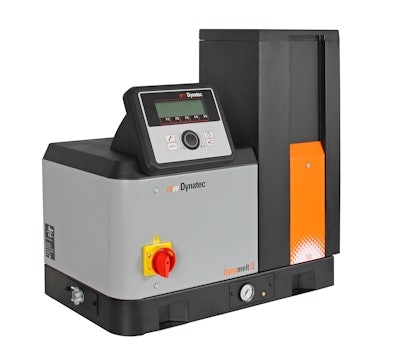
Featuring the company’s patented Melt-on-Demand System, the unit improves operating efficiency, long-term reliability, and sustainability. The Dynamelt S consumes 20% less energy on average than similar competitive units, according to the company. An advanced piston pump design permits low-air pressure operation, resulting in a significant reduction in overall air consumption. The Melt-on-Demand System has been enhanced with a precision heat control zone in the manifold block. The independently-heated manifold optimizes energy efficiency while facilitating faster warm-up times. The corner-mounted hose manifold is covered in a heat insulating jacket, both for user safety and reduced energy consumption.
The primary filter is said to provide 15 times more surface area to offer easier and safer filter changes (filter comes out with the filter nut), reducing downtime. The larger filtration surface lasts longer, requiring less frequent changes and maintenance.
A new feature is advanced diagnostics (through a new ergonomic control panel), contributing to quicker troubleshooting and less downtime. The temperature sensors are easily accessible on the rear manifold of the machine, contributing to reduced maintenance. The new control panel can be positioned on the front, side or remotely away from the unit for easy viewing, and all system parameters can be viewed on one screen for quick evaluation. Nine corner-mounted manifold connections provide flexibility, ease of installation and savings on the length of hoses and power consumption.
Instead of a PTFE coating, an exclusive Nano ceramic coating is used on the inside of cannon barrels. This coating is said to be five times more durable than PTFE and contains no PFOAs or flourachemicals. The Dynamelt S is finger safe to prevent electrical shocks to operator and maintenance personnel. A master power disconnect switch also contributes to safety and negates the need for an OEM to add a disconnect switch with separate lock-out.