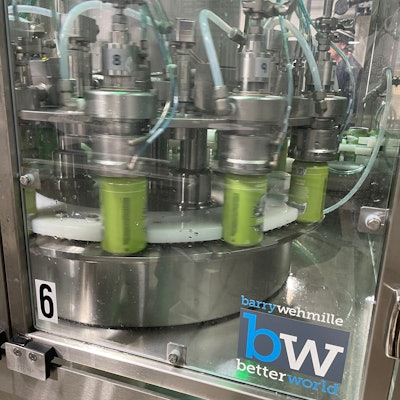
Spanning the range of familiar formats that constitute the craft brew universe—and all within a couple of walkable blocks in Cleveland—are Market Garden Breweries. Founded in 2010, Market Garden Brewery is a taphouse and gastropub that serves beer mostly on tap and has a full menu for in-person occasions. Its nearby Nano Brew Cleveland cousin is more of neighborhood bar and burger joint, but it’s also a specialty pilot brewery—a laboratory for mad scientist brewmasters. And most interesting to us at Packaging World, in a beautifully repurposed older building behind the main taphouse parking lot, Market Garden Craft Brewery represents the production wing of the business. In that facility, always-improving packaging lines provide the scale, speed, and volume to supply wide swaths of Northern Ohio, Central Ohio, and most recently, Western Pennsylvania. New equipment acquisitions, capped off by a new rotary filler/seamer, have the brewery growing its reach and business, even as the wider craft brew industry contracts around it.Depalletizing of bright stock cans is done on a GR-X overhead depalletizer in the warehouse. Cans are single-filed and conveyed through a wall into the packaging hall.
Co-founder Andy Tveekrem’s auspicious beginnings as one of the nation’s pioneers in craft brew, and current status as an industry stalwart and advocate, have equipped Market Garden to navigate a changing and challenging landscape. Early in his career he was brewmaster at venerable craft brew trailblazers Great Lakes Brewing Co., then Frederick Brewing Co., then Dogfish Head, before coming home to Cleveland with Market Garden in 2010. Today, he’s past President of the Master Brewers Association (2021-2022) and active in their local District Midwest. For our purposes, in his role as Brewmaster at Market Garden, Tveekrem has been active in improving packaging equipment.
Filling/seaming update
“But when I looked at some of the canning equipment [available for small volumes] going back to 2014, I was mildly horrified at what I saw. That’s why got excited when I heard Pneumatic Scale Angelus (PSA) [a BW Packaging company] was coming out with the CB50 filler,” Tveekrem says. “It’s a company that’s known for, and maybe invented, the double seam. I figured they're going to engineer it correctly, and that seaming would not be an issue. They’ve taken the same seaming chucks and equipment that they use on their high-speed, 2,000 per minute lines, and applied them for the smaller brewer.”
By 2018, the Market Garden was focusing on canning operations. For about a year, the brewery acted as a beta tester for the now-ubiquitous CB50, which is a 50 can-per-minute (CPM) six-head in-line filler with single-head in-line seamer.
“We've had a really good relationship ever since,” Tveekrem says. “We provide them a lot of data on how the equipment's running, the oxygen content, and the fill heights. They would have their people come up [from the nearby Akron, Ohio area] to do test runs, and even have potential customers come by and look at it.”
The existing CB50 had been a workhorse, and PSA has been keeping it up with upgrades and improvements as they came to market. Before long, PSA brought a 100 CPM in-line filler to market. Soon after that, PSA set its sights on a newer version of the CB100, an isobarometric counter-pressure rotary fill/rotary seam version. Market Garden once again volunteered to beta test the 100 CPM line, but Tveekrem had his heart set on that not-yet available dual-rotary CB100R, so he would have to wait for the first one to roll off the line. Just knowing that that CB100R was coming down the pike later in 2023, Market Garden began upgrading its upstream and downstream equipment in earlier in the year.
“We had already gotten rid of the bottling line, but what we still had left was an older canning line with a half-high depalletizer,” Tveekrem says. “It was clunky and slow, and once we got rid of the bottling, it was absurd to have just half a room with this weird configuration. We had cobbled it together over the years, so it was really squeezed in tight.”
In a bid to future-proof production, Tveekrem and team designed the new line to accommodate speeds much higher than the incoming filler’s max line speed of 100CPM, all the way to 300 CPM. The company will be ready if growth requires even newer, faster filling operations. Market Garden enlisted Peter Viiberg, local integrator and owner of Vee-Pak, Inc. (VPI) to help specify the ancillary equipment that would surround his new filler, with an eye on buying locally when possible.
Upstream upgrades
Once in the packaging hall, cans are lowerated from mezzanine level to floor height.
“It’s nice, with soft rubber fingers that gently convey the cans downward. We run mostly 12-, and some 16-ounce cans. It's able to do 19.2-ounce cans, but we haven't tried that—we’d have to make some adjustments first. In theory, we could even do slim or sleek cans, but we’d have to buy some downstream change parts that we don’t need quite yet,” Tveekrem says.
Single filed, lowerated cans are then conveyed through another new set of equipment—an AFM shrink sleeve applicator and attendant steam shrink tunnel from the same OEM. Outside of a handful of mainstay beers, Market Garden tends to be a higher mix/lower volume operation, so shrink sleeving, both in-house and in-line, is an important new trick. Market Garden previously didn’t have shrink capabilities at all, much less in-line. Shrink sleeves had to be applied to bright cans elsewhere, then brought into inventory in the warehouse. That’s done in-line today, with rollstock supplied by local Blue Label Packaging Co., a Columbus firm with digital printing capabilities.
“Also, we’re seeing a lot of direct-print cans. It's now becoming more viable because the prices are steadily coming down,” Tveekrem adds. “So that's promising too.”Shrink sleeving rollstock from Blue Label Packaging Co. on an AFM shrink sleever.
Still, economics dictate the use of traditional printed cans when at all possible. Recently lowered minimum order quantities (MOQs) from can suppliers have Market Garden moving in that direction where it makes sense. When running printed cans, the shrink sleeve applicator and heat tunnel can simply be turned off. Cans are conveyed through the equipment untouched and at speed.
“Our highest volume beer throughout the year is our Shandy, so last year we started getting printed Shandy cans,” Tveekrem says. “Now, since the volumes for the amounts that you have to commit to keep dropping, we're looking at getting four more of our core brands in printed cans and backing off on the sleeves as much as possible. The sleeves look nice, but they’re just an extra burden to have to apply.” Shrink sleeving is just one more operation where mistakes and scrap can happen, and sleeve rollstock is an additional input cost. “And then there's the whole issue of not being able to recycle them, which is kind of a big thing,” he adds.Shrink sleeves being 'shot' onto awaiting bright cans, pictured here traveling into the steam tunnel.
After the steam tunnel, roughly 400 cans’ worth of accumulation on a winding, double-backing length of Dorner lightweight conveyor helps build up some buffer in the system ahead of filling operations. Also prior to filling, a Carleton Helical Technologies inverter/reverter orients each can for an ionized air rinse, and while temporarily inverted, a Keyence inkjet coding/marking station adds “best by” and “packaged on” date codes. Depending on the product, a third line of text is available for printing—possibly an ABV% to keep from surprising folks with, for instance, a 12% ABV barleywine product.
“The Keyence sales rep is also your application engineer, so when the ‘sales’ guy comes by to see how things are going, he can also make suggestions and get the thing working even better,” Tveekrem says.
Setting aside the canning line inputs, the beer itself is pressure piped into the packaging hall. Immediately before entering the filler, the beer is analyzed in-line via a nifty Anton Paar Beverage Analyzer. The equipment for dissolved oxygen (DO), CO2, liquid density, and calculates the precise alcohol by volume percentage. This isn’t a common step for craft breweries at Market Garden’s volume, demonstrating the company’s commitment to quality.In-line, non-invasive analysis for dissolved oxygen (DO), CO2, liquid density, and alcohol by volume (ABV) percentage.
“It's a unit I found at an auction from Anheuser-Busch. It’s a pretty impressive cluster of in-line instruments and a display,” Tveekrem says. “We snapped it up for pretty good price and integrated it. Beyond the primary metrics, you can also get calories and other fun details. It’s all the stuff you would want to have in your off-line analysis, but you also have it in-line.”
Speaking of off-line analysis, Market Garden does that, too. A QC station resides in the center of what’s lovingly called the line’s “horseshoe” central operating areas, surrounded three sides by the shrink sleeving, inverting/codling/marking operations, and filling/seaming operations, respectively. It’s used for off-line dissolved oxygen and CO2 checks via a Pentair Haffmans analyzer/piercer, and employs data entry and seam analysis via a OneVision Corp. seam inspection system.
New rotary filler/seamer
“We really didn't need a faster filler for the capacity,” Tveekrem says. “At our barrelage of around 8000 barrels per year, we could have gone along at 50 per minute for probably another decade. It was really a quality-improvement decision. With the linear, open atmosphere filling machines, there's only so much you can do with them [from a dissolved oxygen pickup standpoint]. Also, we wanted to get into counter pressure and then getting it all rotary—on the seamer too—was a big plus. It’s where I think packaging should be; it’s certainly where we were with bottling back in the day. We wanted better dissolved oxygen (or complete lack of it), and better, more consistent fill heights across the all the filling heads. We knew this machine could deliver that. Running higher carbonation levels in various beers/ciders is also a big benefit for us. You can’t do that with in-line filling.”
Even though speed wasn’t a motivation, it has been a nice perk. It used to take a full week to run a full bright tank of shandy, now Market Garden can do that in two days of regular shifts, no extra hours.
“Being able to run at your rated speed consistently is a really nice thing,” he adds. “And as you can see, it's just a beautiful piece of equipment with a nice Allen-Bradley HMI package.”
The Rockwell controls package includes logic to self-adjust if it detects that the system is under filling over a certain number of cycles. Volumetric fill information for each unit fill, taken at each filling head, is recorded in real time. That means automation can catch and correct for overs and unders, or operators can intervene and manually adjust a low-filling head to, for instance, add 2 mL to each fill.PSA is known for seaming. Here, a three-head seamer spins lids onto cans.
“It'll start ramping up and adjust itself, which is kind of cool,” Tveekrem says. “Also, it features what they call under-turret gassing, pushing inert gas through slots just at the point of the lid being indexed onto the can. A lot of lines will have an actual tunnel where the cans are coming through and they're flooding that whole tunnel with gas. This is doing it right there at the point of the lid going on. That system is integrated into the CIP, so when we’re doing our cleaning cycle, that’s where cleaning solution can be introduced through those ports. We’re kind of crazy about CIP around here, which I think PSA likes about us. We can anticipate some cleaning issues other breweries probably don’t.”
Immediately following filling, cans pass through a Heuft x-ray low-fill inspection/detection station as yet another means of QC. If you haven’t noticed, there’s a remarkable and rare amount of QC going on throughout the packaging line. Inverter/reverter system with ionized air rinsing and inkjet date coding operations being accomplished in the short period while the cans are inverted.
End of line
Upstream equipment improvements tend to push bottlenecks downstream, and this packaging line upgrade was no exception. After the new filler/seamer was dialed in, increased speeds necessitated an upgrade in can handle-application. A new applicator from Roberts PolyPro, a ProMach brand, now adds can handles at 12 at a time in a 2x6 configuration for two six-packs. With a few change parts, the equipment can also handle or 3x4 for three 16-oz. four-packs.Twelve-at-a-time can handle application on a new Roberts PolyPro system.
Meanwhile, an off-line Switchback (acquired by Mpac) tray erector that resides in the warehouse uses hot-melt adhesive to erect printed 24-pack trays, sending them through another window in the wall via skate conveyor into the packaging hall. At an adjacent pack-out station, operators hand-pack the trays with multi-packs, or sometimes, with loose cans. Can handle multi-packs tend to go to retail, and loose cans, often 16-oz. formats, are frequently bound for sports stadiums and event arenas. Tray erection on Switchback equipment in the warehouse.
What’s next?
Tveekrem and Market Garden have been discussing two pieces of equipment—a pasteurizer and a cartoner. Pasteurization could expand the company’s regional reach, but the sheer size of the equipment makes it impractical for now. The cartoner idea, though, might have legs. Two factors have kept Tveekrem and Market Garden from pulling the trigger. The size of the equipment itself, and space the cartonboard inventory would consume, is one constraint. The one-time capital outlay for the equipment, plus the ongoing expense for a consumable like cartonboard, is the other.
“And of course, every time you print something new, maybe for a new variety or format, there's another printing plate, and there’s another cost,” Tveekrem says. Regardless, he’s pretty gung-ho on cartoning next.Operators pack out 24-count trays of can handle-applied 6-packs.
“It's great billboarding. You can you build these nice little cubes or boxes, and it’s great branding out on the shelf that looks more professional,” he says. “But also, if you do multi-packs with three cans of four different of beer, which we do, it could really help with that. We pack them all by hand right now. You can get the lanes situated such that one person's filling this lane, and another person's filling that lane—it’d be a whole heck of a lot easier to just run it into the machine and have it box it all up for you.”
And remember, even though the filler/seamer is still new and humming along at a cruising speed of 100 CPM, the line is really built for 300 CPM. Any new equipment, like a cartoner, would surely follow suit. While the brewery might not have much production space left to grow into, it still has plenty of runway in front of it to grow in terms of volume and throughput. That ace up Market Garden’s sleeve makes for a promising future. PW