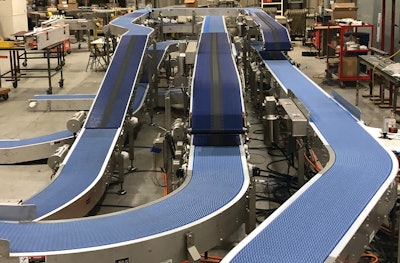
This content was written and submitted by the supplier. It has only been modified to comply with this publication’s space and style.
Multi-Conveyor recently built a complex, yet small-footprint, custom conveyor system that uses a servo transpositor retract and two stacked servo merges to transport bags of chicken from three baggers to two case packers, with X-ray scans in the process.
Some of the challenges on this system were:
- the multitude of product sizes, weights, and rates
- the need for vibratory bag settling sections in some of the conveyors to help distribute product within the bags
- merging and balancing of three lanes to two lanes
- the very limited floor space
- the 3-ft elevation differential from the baggers to the X-rays, which is complicated by the additional elevation changes needed for the servo transpositor and servo over/under merges and related alternate conveyor paths
Some products will require only two baggers and will be delivering product to the two lanes going directly to the X-rays. If one of the baggers goes down, product will be transferred to the third bagger and delivered to the transpositor that will then be positioned to deliver bags to the alternate conveyor path for the now-empty lane of the down bagger. When the down bagger returns to service, the flow to the transpositor will cease.
Some product rates will require three baggers to meet the required throughput. The third bagger will deliver product to the transpositor, which will evenly distribute bags between the two upper level alternate bagger lane conveyors, which resulted in conveyors at 4 different levels. The third bagger flow will then go to its respective over/under servo merge on each lane. The servo belts on the lower level will position product to allow the bags from the upper level to drop into an opening created by the servo belts. Ultimately, the system design met the challenge of getting product from three lanes at 8-in. elevation and merging them to two lanes before delivering them at the 45-in. elevation required for the X-rays.
Multi-Conveyor additionally provided four vibrating modules to settle product in the bags. VFD-driven square rollers were mounted under the plastic belting to vibrate bags as they travel on the conveyor. The bag and case system is PLC controlled and includes 36 VFDs and eight servos.
The Multi-Conveyor controls and conveyors for the bag handling are part of its larger overall system that also includes empty case handling and full case indexing and merging from the two case packing lanes to a single discharge flow.