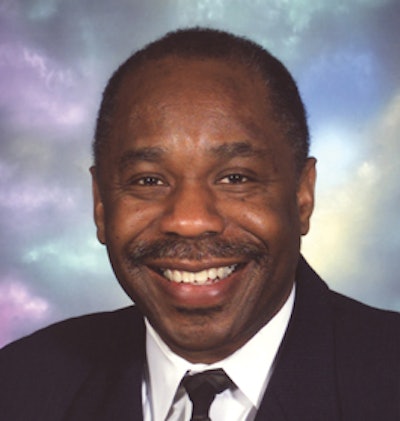
How far could a rider go on a horse that couldn’t carry the weight, over the planned distance, through the anticipated conditions? Not far enough. That horse would collapse and the rider would take an inglorious spill. Now, substitute a pallet for the horse and packaged goods for the rider, and the result is the same. When pallets fail, goods are damaged, costs rise, and productivity drops, as does customer satisfaction; yet, pallets remain the proverbial afterthought.
A big reason is standardization: in the U.S., the 48x40 inch GMA pallet dominates, although not internationally (the 1200x1000 mm pallet is used throughout Europe and Asia). So it’s common for packaging professionals to regard the pallet as a given, and to develop the packaging to make optimal utilization of the pallet’s footprint. Whereas each package development project generates new packaging specifications, such is not the case with the pallet.
Of course, it’s impractical to devise a new pallet specification in conjunction with each new packaging specification, if the pallet covered by an existing specification will be used. It’s definitely practical, however, to evaluate the existing specification for adequacy, and to improve it as needed.
Assume a 48x40 wooden pallet. The typical specification will include a drawing designating the type (i.e. block or stringer). It also should specify: the type of lumber; the thicknesses of the lumber; whether deckboards are abutted and if not, the dimensions between them; and, the type of fastener. A pallet supplier can quote and build in accordance with a specification of such detail. Unfortunately, being within specification does not guarantee performance if the specification does not reflect an understanding of the interactions among the components. The following are some examples.
A pallet designed to be lighter in weight will have a lower price and will save on transportation costs, but possibly at the expense of strength, stiffness, durability, and ultimate performance. If spacing of the deckboards is too generous, parts of the load might go unsupported, thereby destabilizing it. Hardwood provides greater nail-holding but is more prone to splitting, making the length, size, and number of nails important factors. Regardless of the wood species, nails applied in a staggered cluster hold better than ones applied across a straight line.
It’s advisable to include certain quality-assurance requirements in the specification. One of them should be the moisture content of the lumber. Too much moisture will: add to the weight of the pallet; cause warping; reduce the wood’s nail-holding capabilities; and invite fungus, bacteria, and insects—among other undesirable effects. Another requirement should address the type and limits of lumber defects. Depending on the size and location of a knothole, for example, the strength of the board can be reduced by more than half.
And, there are tolerances to be specified. Standardization in pallets does not entail the same exactness as machined parts; nothing made of wood does. Not all 48x40 pallets are 48x40. Pallet shops differ in the precision with which workers measure, cut, and assemble the lumber. But, automation in warehouses and distribution centers require tighter tolerances, as any visit to an AS/RS (automated storage/ and retrieval system) facility will underscore.
If all of the preceding discussion were limited to new pallets, decision-making would be complex enough; however, adding to the complexity is the reality that many pallets are refurbished, thereby adding to the variability of the equation. Moreover, the CPGC that knows what percent of its damaged shipments is due to pallet failures is the exception. It follows, then, that so too is the company that collects the data that would be the basis for that knowledge.
The potential for plastics
Plastic pallets are growing in usage, and fundamental knowledge about them is useful to the packaging professional. To gain it, one must shift through the back-and-forth recriminations between plastic pallet suppliers and wood pallet suppliers.
Suppliers of plastic pallets concede that their product is more expensive. For that higher price comes benefits exclusive to plastic, a partial list being: no load damage from either splinters or nails; greater standardization/ tighter tolerances; a flat, continuous load-carrying surface; increased design options; sterilizable for preventing cross-contamination; impervious to organisms and insects; and aesthetics.
Besides price, other debits include: fewer supply sources; potential price swings tied to oil; not easily repaired; and, more of a fire hazard.
Some advice--which should not be taken as advocating plastic pallets--is to analyze claims for what they don’t say. A case in point is the claim that a plastic pallet costs more than a wood pallet of the same weight. The reality is that a wood pallet would have to weigh somewhere between 25-30% less than the typical wood pallet, in order to weigh the same as a plastic pallet. Such a wood pallet would lack structural integrity. Wood pallets weigh more, period, and cost-per-weight is not a meaningful metric.
Critical thinking also should be applied to claims about the sustainability of plastics vs. wood. No justice can be done to the topic in the remaining space of this article; nonetheless, a few observations are in order. One is that each side bases its arguments on Life-Cycle Analysis, thereby proving, once again, how malleable (unfortunately) that tool is. Another is that sustainability as it relates to pallets might not be as driving a concern to a CPGC. Without suggesting that sustainability should not be a factor, it’s realistic to say that it might not head the list.
Plastic pallets do have an advantage over wood pallets in tagging (RFID and barcodes). The tag can be incorporated onto the pallet at the time the pallet is molded. In determining the importance to assign to such an advantage, the CPGC should form an opinion as to the future of tagging technology, particularly the role of retailer mandates as a driver. Additionally, if a switch to plastic pallets is decided, the conversion schedule should be meticulously thought out. Then too, manufacturers of high-value products (pharmaceutical and medical devices come to mind) might option for plastic pallets, mostly for the tracking capabilities tagging bestows.
Pallet management
In today’s hotly-competitive business environment, CPGCs of all sizes seek to outsource whatever allows them to more profitably concentrate on the core business, hence, the need to team up with the right pallet management partner.
The leased pool is a program for reusing pallets. Pallets are leased to the CPGC, are loaded, and are sent through the supply-chain. Empty pallets are collected and sent to a central storage location, where they stay until being sent to another CPGC. The blue, block, wood pallet is the most citable example. Aside from pools for wood pallets, other pools specialize in plastic.
Another program is buy/sell. Pallets are sold to the CPGC, but the ownership is not permanent. At the end of the supply-chain, the pallets are purchased by a pallet management company that repairs them, as needed, before reselling them to yet another CPGC. Pallets beyond repair are used for parts.The program specializes in wood stringer pallets, commonly called white pallets, because they are not painted.
Which program is better is a case-specific determination. One consideration is the physical differences between block and stringer pallets; block is heavier and taller, which impacts transportation costs and storage space utilization. More important is the overall quality of the pallets received. Is the management company reducing operating costs by delaying repairs and maintenance? Another consideration is whether the company’s major retailers prefer a particular program. Yet another is the amount of bargaining power that can be wielded in dealing with the pallet management partner.
For related reading, see the September 11, 2009 Packaging Insights article, E pluribus unit load.
Sterling Anthony is a consultant, specializing in the strategic use of marketing, logistics, and packaging. His contact information is: 100 Renaissance Center-176, Detroit, MI 48243; 313-531-1875 office; 313-531-1972 fax; [email protected].