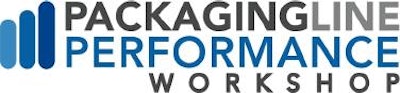
Paul Zepf of Zarpac Inc., a leading packaging industry
authority in Overall Equipment Effectiveness, shared his OEE process
improvement list at recent Packaging Performance Workshops (see below
for more information).
Based on Zepf's 35 years of related industry experience, these are the
Top 10 sources of OEE losses he has identified at packaging operations:
1. Losses due to lunch period time, lunch overage times, production run down before lunch and production run up after lunch.
2. Losses due to break period time, break overage times, production run down before breaks, and production run up after breaks.
3. Losses due to meeting period time, meeting overage times, production
run down before meeting (if applicable), and production run up after
meetings (if applicable).
4. Losses due to shift changes, production run down before shift changes and production run up after shift changes.
5. Losses due to extent and frequency of major changeouts.
6. Losses due to minor changeouts.
7. Losses due to purge at the end of a given production run.
8. Losses due to the difference in speed actually run on the production
line versus what should have or could have been run based on the
original design of the line and its tested capability.
9. Losses in hierarchical order of the downtimes of each machine.
10. Losses due to wastage, including all material costs, labor costs,
ergonomic costs, bins or cart costs, holding area costs, transfer
costs, and disposal costs.
We plan to provide the next 11 along with other OEE insights from Zepf in upcoming issues of Packaging Insights.
For further information, visit www.zarpac.com and check out the next
Packaging Line Performance Workshop
sponsored by Packaging World, ELAU, Hartness Intl., and Multivac. The next workshops
are slated for June 24-25 in Los Angeles and Sept. 16-17 in New
Brunswick, NJ.
-Rick Lingle