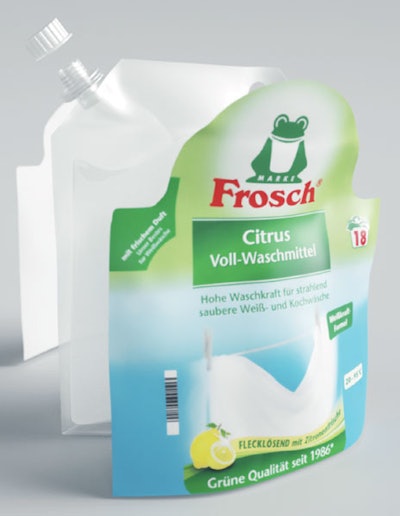
Flexible packaging has always had a good sustainability story versus rigids, given that it has a lighter weight, generates fewer CO2 emissions, and results in a higher product-to-package ratio, among other advantages. The sticking point has always been the non-recyclability of multilayer pouches. But new material technology is making the use of mono-material, recyclable polyethylene for flexible packaging a reality.
For German cleaning products company Werner & Mertz GmbH however, it wasn’t enough to move from a multilayer pouch to one made from PE only for its laundry detergent. It also wanted to ensure that as much of the pouch as possible was free of ink and adhesives. What it came up with—a single-layer PE pouch with detachable, decorative panels—won the company, along with supplier partner Mondi, a Diamond Award Finalist spot in The Packaging Innovation Awards.
“Other mono pouches are made of two layers of one material. One is printed and glued onto the second layer. The print is on the inside to secure it from damages,” explains Werner & Mertz Packaging Developer Alexander Schau. “There are two reasons for the special construction of our pouch. First, we want to keep most of the material—up to 80 percent—unprinted to ensure high-quality recycling. Only a very thin film is printed and can be used for the colored recycling stream.
“Second, we wanted to prevent adhesives. The outer film is printed backwards. This creates a damage-secure surface on the outside. Afterwards, it is welded onto the main body just on the outer edges of the film. No adhesives are needed.”
The impetus for the four-year-long development project was Werner & Mertz’s commitment to sustainability and its efforts toward creating packaging that fits the circular economy model. “We believe that plastic packaging can be kept in a real circular use like glass,” says Schau. “For PET and PE rigids, we’re close already, but so far, we haven’t reached this for our flexibles due to multi-material mixes. It is our clear task to roll out recyclability over our complete packaging portfolio.”
In 2015, the company challenged several flexible packaging suppliers to come up with a 100% recyclable pouch, “but only Mondi was willing to take this challenge and develop, in a partnership, this outstanding result,” says Schau.
The main pouch body and the detachable front and back panels are devoid of barrier and are made from Dow’s Dowlex NG 5056 G low-density polyethylene resin. A spout and cap, also made from 100% PE, are heat-sealed to the clear pouch body along with the 0.05-mil reverse-printed panels during manufacturing by Mondi.
Reads Werner & Mertz’s competition entry form, “The two detachable printed panels (films), carry the decorating print design and product information. By just printing on the outer film, we can assure a good detectability in near infrared during sorting. No additional label material, such as paper, is disturbing the detection process.