• Will cabinet-free packaging machines be next? Gerhard Schubert GmbH showed a system at interpack that did away with the well known and sometimes scorned electrical/pneumatic control cabinets. With IP65- and perhaps even IP69-rated sensors, motors, drives, cylinders, power supply, logic box, and HMI screens, an entire machine might be wired together with plugs and cables, with all of the components mounted at the point of use with the possible exception of the electrical disconnect and fuses, although there is no theoretical reason that these, too, could not also be self contained. For the machine builder, this allows a very modular design and a smaller footprint. And the detailed engineering can largely be done by the component suppliers. Which raises the question of what do we need an electrical controls engineer for anymore? One drawback of this approach is cable management. Bundled cables create many hard-to-clean crevices where dust and bugs will love to congregate. I saw some terrible cable management schemes on the floor. Those machine builders might want to study machinery OEMS that focus on pharmaceutical operations to see how they do it.
Cabinet-free packaging machines?
In the last edition of this newsletter, we featured a handful of new developments that Packaging World Blogger and Contributing Editor Keith Campbell found at interpack 2014. Here’s three more.
Jul 23, 2014
Machinery Basics
Annual Outlook Report: Workforce
Hiring remains a major challenge in packaging, with 78% struggling to fill unskilled roles and 84% lacking experienced workers. As automation grows, companies must rethink hiring and training. Download the full report for key insights.
Download Now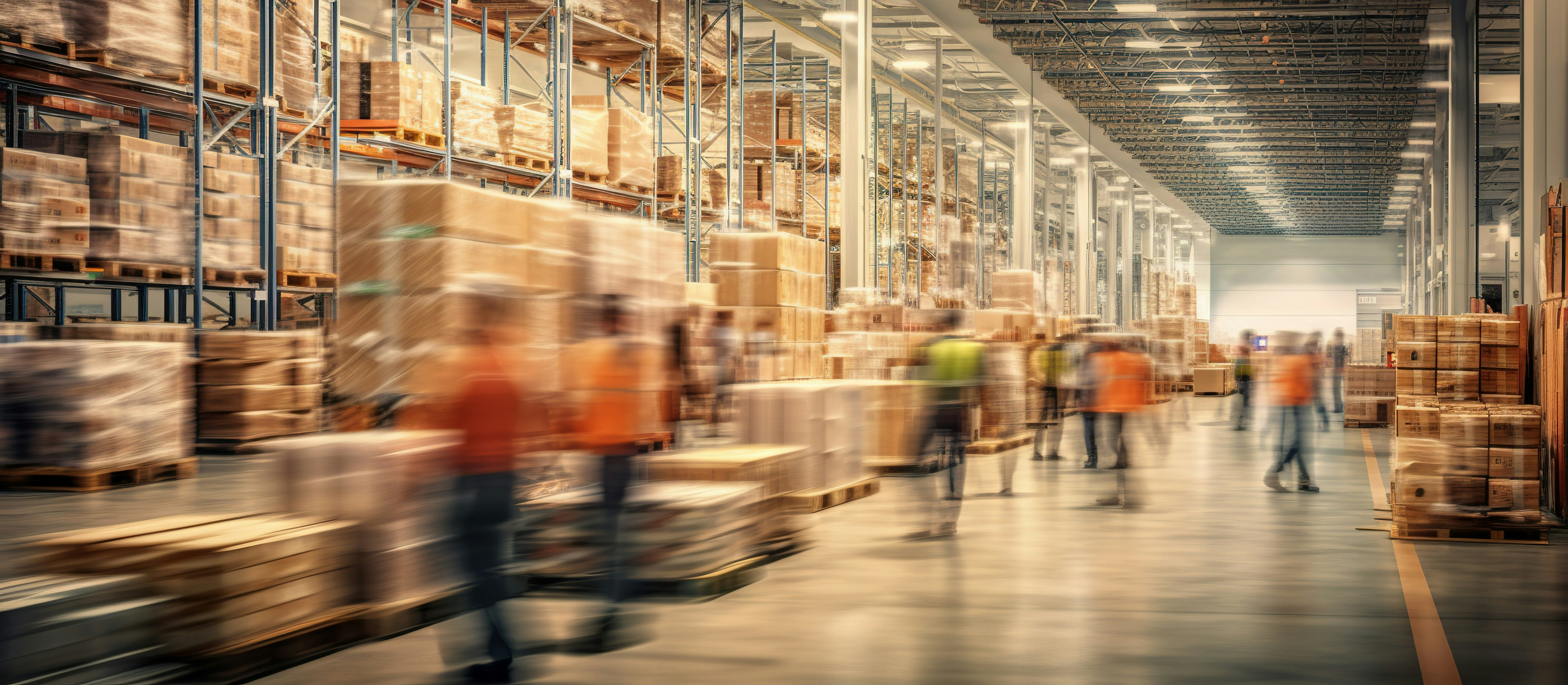
Annual Outlook Report: Automation & Robotics
What's in store for CPGs in 2025 and beyond? <i>Packaging World</i> editors explore the survey responses from 118 brand owners, CPG, and FMCG <i>Packaging World</i> readers for its new Annual Outlook Report.
Download