Pat, your recent insights article should raise a lot of heated discussions and opinions. As a control supplier, we are constantly involved in this argument as we have many potential OEMs tell us that they see a lot of value in our products whether it is performance, price, communications, size or a combination but they can't use us because their end users always spec Company A. Our view is that the standardization approach of many end users is based too much on events from the 80's and 90's when machine control systems needed lots of disparate product to handle the automation tasks, and the maintenance staff had to manage multiple types of devices to keep the machines running. End users are being pushed today to reduce costs, improve productivity, reduce operators, get machines connected to the IT world for various needs for data, be more flexible as products are changing faster in smaller batches than before and are therefore pushing OEMs to be more innovative. They then throttle back the possible innovation that can come from considering other solutions and specify the control products to be used because they perceive that to be less risk due to support issues. The OEM is therefore restricted in their options to innovate.
Who should spec an automation platform?: August 27, 2008
Editor's note: Several weeks ago in this newsletter I published some thoughts on whether it's best for packaging machinery builders or their end-user customers to decide which controls platform should be controlling a packaging machine. I also asked readers for their thoughts on this subject. In the next few weeks, I'll publish a few of the comments I received. This one comes from Graham Harris, president of Beckhoff Automation.
Aug 26, 2008
Machinery Basics
2024 PACK EXPO Innovations Reports
Exclusive access: Packaging World editor-curated reports revealing PACK EXPO's most groundbreaking technologies across food, healthcare, and machinery sectors. Each report features truly innovative solutions selected from hundreds of exhibitors by our expert team. Transform your operations with just one click.
Access Now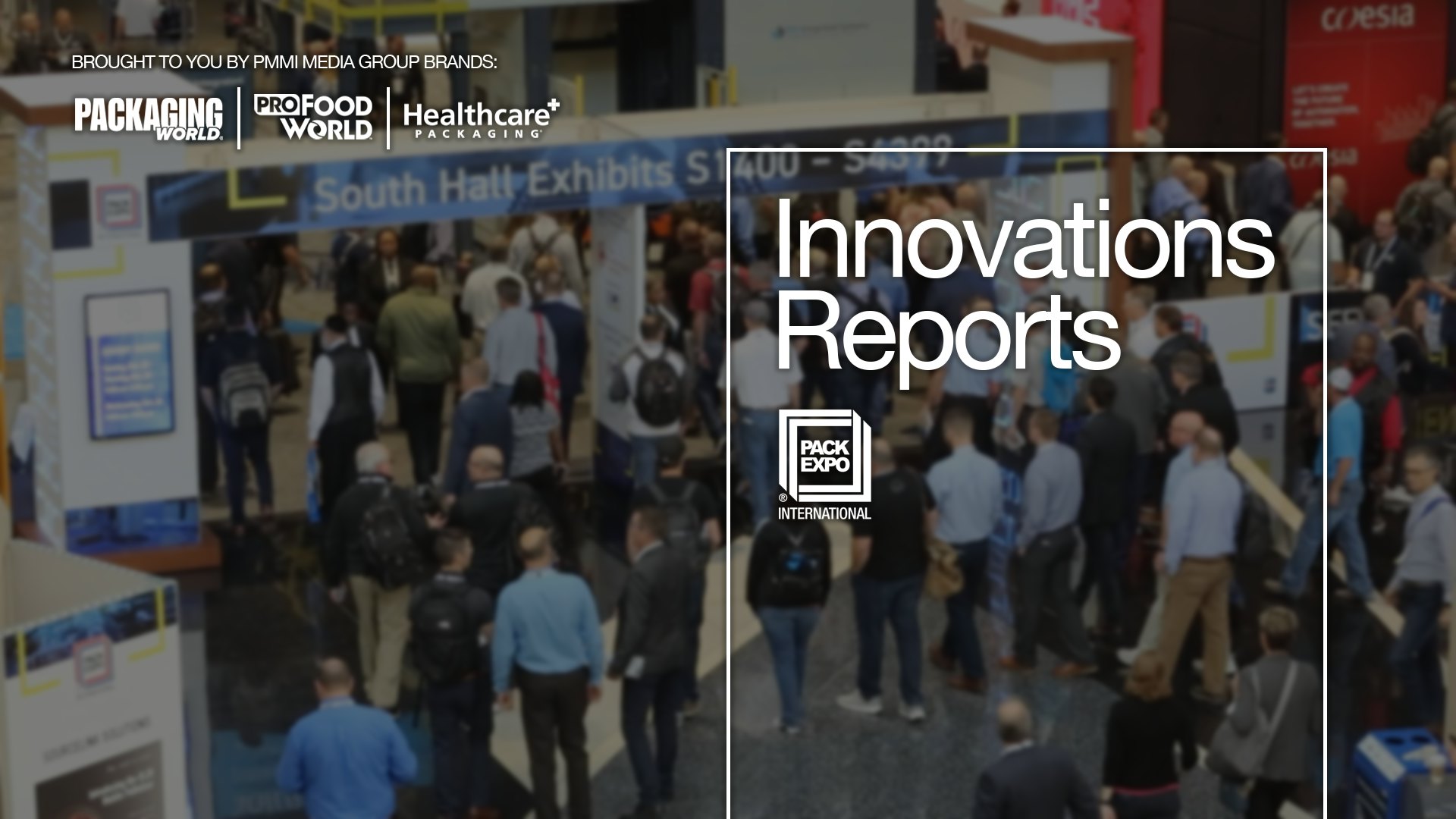
Conveying Innovations Report
Editors report on distinguishing characteristics that define each new product and collected video demonstrating the equipment or materials as displayed at the show. This topical report, winnowed from nearly 300 PACK EXPO collective booth visits, represents a categorized, organized account of individual items that were selected based on whether they were deemed to be both new, and truly innovative, based on decades of combined editorial experience in experiencing and evaluating PACK EXPO products.
Take me there