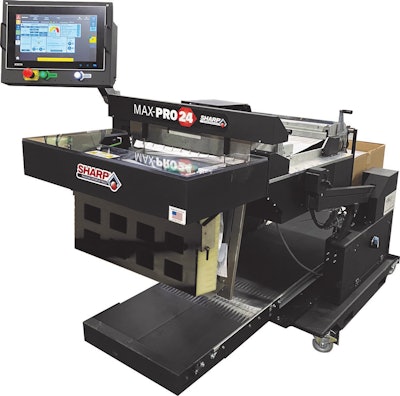
This content was written and submitted by the supplier. It has only been modified to comply with this publication’s space and style.
Pregis’ MAX-PRO 24 continuous bagging system has a small footprint, but can accommodate bags that are up to 24-in. wide and 36-in. long. It handles products that weigh up to 10 lb Its size allows the machine to fit into existing packaging lines while taking up less floor space. Additionally, its innovative label side up, multiple exit conveyor system allows bags to leave the machine to the left, right, or rear, so it can be added into existing production lines more easily.
“When engineering the MAX-PRO 24, our focus was on creating a system that would help users maximize productivity and minimize labor costs. We think the MAX-PRO 24 delivers all that, and more, making it ideal for increasing volume demands being placed on e-commerce operations,” said Mike Menz, division president.
The MAX-PRO 24 includes highly-advanced automated technology, new web handling features that simplify operations, and automated pass-through settings, resulting in lower operating costs. Predictive maintenance via Pregis’ proprietary Maxwell intelligent interface, enables trouble-free operation. The system also includes an easy-to-use bag threading system and a user-friendly HMI control panel that simplifies operation and guides troubleshooting. Its low-force jaw is designed to make the machine safe, simple and cost effective to use
In addition to being simple to operate and easy to integrate into current operations and processes, the MAX-PRO 24 has a number of features that contribute toward reducing packaging costs. Zebra thermal printers permit direct printing onto packages for barcodes, graphics, and alphanumeric fonts. In order to maximize ribbon usage, reduced spacing between impressions has been incorporated, plus printing with alternative registrations and adjusting impression placements. All of these improvements help decrease thermal ribbon consumption by as much as 90%.