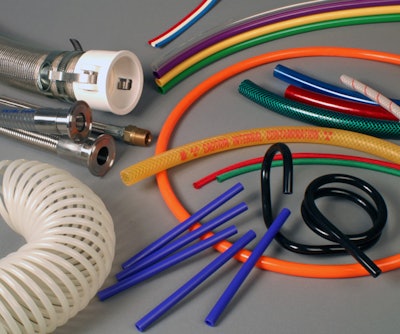
These products, made to an engineer’s or buyer’s specifications, offer improved ingredient compatibility, lower procurement and inventory carrying expenses, a refined appearance, and reduced assembly time and labor costs.
The following tubing customization methods are offered:
• Custom extrusions, where additives are blended with raw materials for improved performance characteristics such as low temperature flexibility, improved elasticity, and anti-static properties; special colors can also be incorporated
• Hot Bond® thermally bonded tubing for a neat, contained ribbon of tubing without the use of damaging adhesives or cable ties
• Heat-formed shapes that eliminate problems such as kinking and proper fitting attachment
• Coiling to give traditionally straight or semi-rigid tubing easy movement and retraction
• Fabrication such as printing, striping, repetitive cutting, slitting, and hole punching
• Overbraiding and jacketing for heat and friction protection, plus added pressure capabilities
• Hose assemblies to reduce on-site inventories and labor
• Dip molded tubing for consistent interior dimensions, even flow, and the elimination of fittings and clamps
NewAge Industries customizes flexible and semi-rigid tubing materials such as PVC, polyurethane, nylon, fluoropolymer, thermoplastic rubber, and other thermoplastic and thermoset compounds. Custom tubing is used for foodservice equipment, automotive parts, and medical device industries.