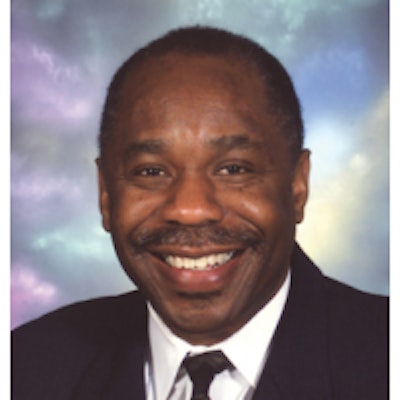
Extrusion blow molding (EBM) produces billions of plastic bottles each year, for such product categories as food & beverage, pharmaceuticals, personal care, laundry, household chemicals, and motor oil & additives. EBM is the: continuous extrusion of a parison; closing of a mold around the parison; blowing of the parison to the contours of the mold; chilling of the mold; opening of the mold; ejection of the bottle; and, trimming of excess plastic (flash). The process is comparatively simple, having obvious similarities to the blowing of glass bottles, yet complex enough that it involves a multiplicity of considerations.
EBM can produce a diversity of bottle shapes and finishes, structural designs that can differentiate a product for competitive advantage. In addition to aesthetics, structure delivers function, an example being squeeze bottles with a measurement compartment at the top; however, if there’s a single functional feature singular to EBM designs it would be handles. The need for handles to facilitate gripping, carrying, and dispensing increases as bottle size increases, a self-presenting correlation; however, what might not be as evident is the trend toward larger sizes, driven by big-box stores (with, to a certain degree, conventional stores following suit).
The diversity of designs that EBM makes possible is seen even at the stock level; however, going with a custom design is an affordable route even for the small-to-medium size brand-owner. The molds are less expensive than those for injection blow molding, due in large part to the lower pressures used in EBM, which, in turn, allows for the molds to be made from aluminum (vs. sturdier, more expensive metals and alloys). There’s an additional benefit, in that mold lead-times are shorter.
Since molds are made to reproduce a given bottle design, it’s important to understand some fundamental design limitations. It’s advisable to avoid sharp corners and far-reaching sections because the parison can be stretched too thin in those areas. Also to be avoided are generously large flat surfaces, as those are given to warping. Incidentally, uniform wall thickness is not always an aim; for, sometimes a bottle needs to be thicker in certain areas. A process control known as parison programming can be used in that regard. One last caveat: avoid going overboard on intricate, complex designs; although EBM can accommodate bottles that are of irregular geometry, it’s possible for projections, appendages, etc., to separate or get damaged simply by the force generated when the mold opens.
Coexisting with coextrusions
Barrier properties sometimes are required of plastic bottles and can be met with coextrusions. As an example, ethylene-vinyl alcohol (EVA), an oxygen barrier, can be incorporated into the parison, most likely sandwiched between protective layers of polyolefin (since EVA is moisture sensitive). When the need is for a UV light barrier, a coextrusion incorporating a black-pigmented center layer might be the answer.
And speaking of UV light in the opposite sense, some applications call for see-through clarity. Polyvinyl-chloride, a longtime option, has come under environmental disfavor. To the rescue has come various copolyesters, that, in addition to clarity, also provide performance traits, among them oxygen barrier and good impact-resistance. And although clarity is not the defining trait for polyolefins, such as polyethylene and polypropylene, there are additives, especially formulated for EBM, that appreciably increase clarity.
Some premium-priced products within the personal care category—shampoos and conditioners, for example—need bottles that project a high-end image. Pearlescent bottles fulfill that need; however, the pigments that impart that characteristic are expensive, so rather than mix them throughout the bottle’s thickness, a more cost-effective alternative is a coextrusion that’s pearlescent only in the outer layer.
Actually, implied with all coextrusions is the need for cost-effectiveness—using the minimum number of layers in the minimum thicknesses, consistent with performance requirements.
Selling sustainability
Plastics are a favorite target for sustainability-tipped arrows, so how much is that fact changed by the use of EBM technology? Limiting the discussion to materials, one topic is recycled plastic, the rationale being the reduced use of virgin resin, and consequently, the reduced use of fossil fuel. But the use of recycled plastic has practical limitations, as a layer in a coextrusion, and more so as a monolithic wall thickness. Recycled plastic might contain various contaminates, which can be a problem with EBM processing; furthermore, any possibility of migration can disqualify its use with ingestibles, such as food, beverage, and pharmaceuticals.
Another topic is bioplastics.There’s at least one commercialized application of a plant-based plastic used in an EBM-produced squeeze bottle for food. Expectantly, the promotion cites renewability, with concomitant reductions in oil consumption and in CO2 emissions, but, those claims are akin to individual frames in a movie reel; they don’t convey the whole story. Any biomaterial’s sustainability profile is separate and distinct from its processibility profile. One example that will serve for many is melt strength; gravity acts upon the parison, and if the resulting sagging is too great, the parison can tear. Even short of that, insufficient melt strength can cause uneven material distribution throughout the walls of the bottle. In compensation, process parameters (melt temperature, extrusion speed, blow time, blow pressure, etc.) might have to be altered; however, the challenge is to do so without negatively impacting cycle-time and productivity.
Expanding the discussion beyond materials, EBM requires energy sources to heat the material and to run the other components of the operation. EBM utilizes water as a cooling medium. More energy-efficient utilization of energy sources and of resources is a reliable path to increased sustainability.
Go with the flow
Bottles are most associated with liquids (of varying viscosities); however, they potentially are suitable for anything that flows. If the method of dispensing is to pour, bottles can compete with flexible packaging and with cartons and boxes, for dry forms such as powder, pellets, and granules.
But no process is perfect. Problems inevitably occur that result in defective bottles. One hardly needs convincing of the value in being able to recognize defects and to understand their probable causes. Troubleshooting EBM will be the topic of an upcoming article.
Sterling Anthony is a consultant, specializing in the strategic use of marketing, logistics, and packaging. His contact information is: 100 Renaissance Center- Box 43176; Detroit, MI 48243; 313-531-1875 office; 313-531-1972 fax; [email protected] www.pkgconsultant.com