Tanaka Kapec Design Group addressed several challenges in packaging MTF’s allograft tissue. “It’s interesting that all of the packaging projects that we have been involved in evolve out of human factors or problems,” says Jeff Kapec, TKDG’s vice president and principal.
“Part of the design process for the MTF packaging was understanding how the tissue was used in the operating field,” Kapec says. “For hospital personnel pouring the tissue out from the container, we recognized that because the previous glass and plastic containers were cylindrical, it made them more difficult to handle. We added dimples in the sides and had the container shaped as a rectangle to make it feel more secure in the hands of the scrub nurse who empties the tissue into the basin in the surgical theater. Not only is this a practical approach, but it also creates an experience for them when handling and opening the package, which becomes a delivery system that helps improve the use of the tissue.”
The original cylindrical glass or plastic containers posed packaging difficulties that extended beyond handling. Explains Kapec, “The first thing that occurred to us was that the cylindrical packaging could not be used because there was no way that we could increase the size of it to accommodate the additional tissue volume MTF wanted to pack in the container, and still fit it into the outer blister. We had to get involved in the technology, the blister forming, to understand the maximum draw and width.”
On the materials side, Kapec says, “We needed a material that was FDA-compliant, that was clear as glass so users could see the contents, and that could withstand the lyophilization and sterilization processes. We conducted considerable research that forced us to look at some novel materials.”
The ultimate selection between cyclic olefin copolymers or polymers (COCs or COPs) came from the design firm’s work in cosmetics, where the plastic provides a visual clarity without breakage concerns. “We worked with COC material in a cosmetic application, and were aware of new syringes being made with COP,” Kapec says. “So we started searching and selected the COP from Zeon Chemicals, which were being formulated in Japan, but the company has a large U.S. presence. Zeon ships resin to Inoac for injection blow-molding in the rectangular shape, which proved to be the key to better handling and containing the larger amount of allograft tissue sought by MTF.
TKDG was also involved in the design and procurement of closure suppliers. “We looked at a variety of different closure methods, but we had to account for the operating room and ease of opening of the container without spilling contents because you cannot waste any of this donated tissue,” Kapec says.
The design firm worked with MTF to evaluate multiple closure styles. Says Kapec, “We needed to make sure that the stopper would not get caught up and jammed, that it would be easy to remove once the crimp seal was removed. Nurses couldn’t be fighting to open it. We looked at a variety of materials and closures that were available and made the selection based upon ease of use.”
Redesigned container for allograft tissue addresses usability issues
Tanaka Kapec Design Group addressed several challenges in packaging MTF’s allograft tissue.
Sep 29, 2011
Machinery Basics
New ebook focused on cartoning equipment
Read about the various types of cartoning equipment, how to select the right one, and common pitfalls to avoid. Plus, read equipment advice from CPGs for ultimate cartoning success.
Read More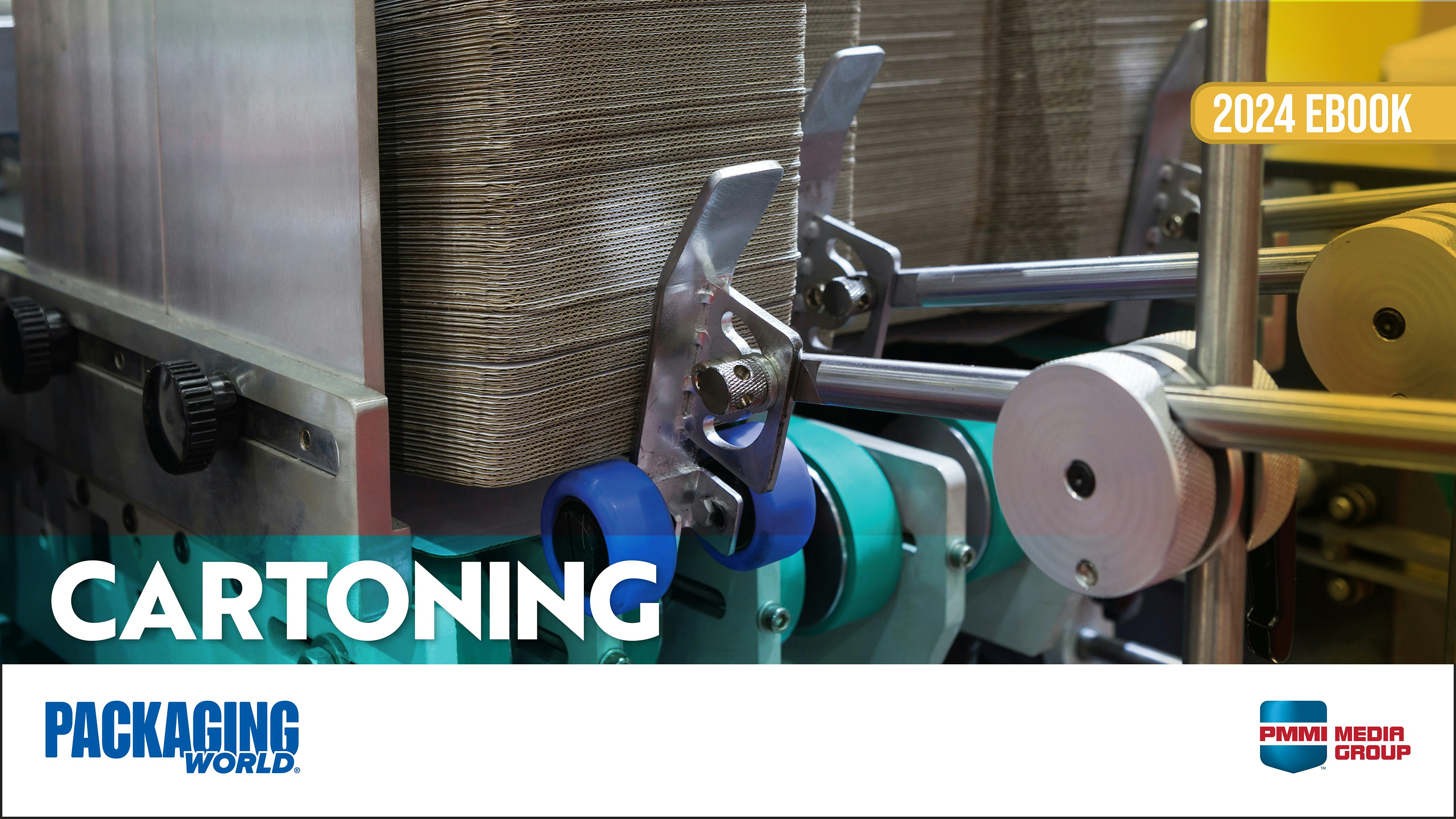
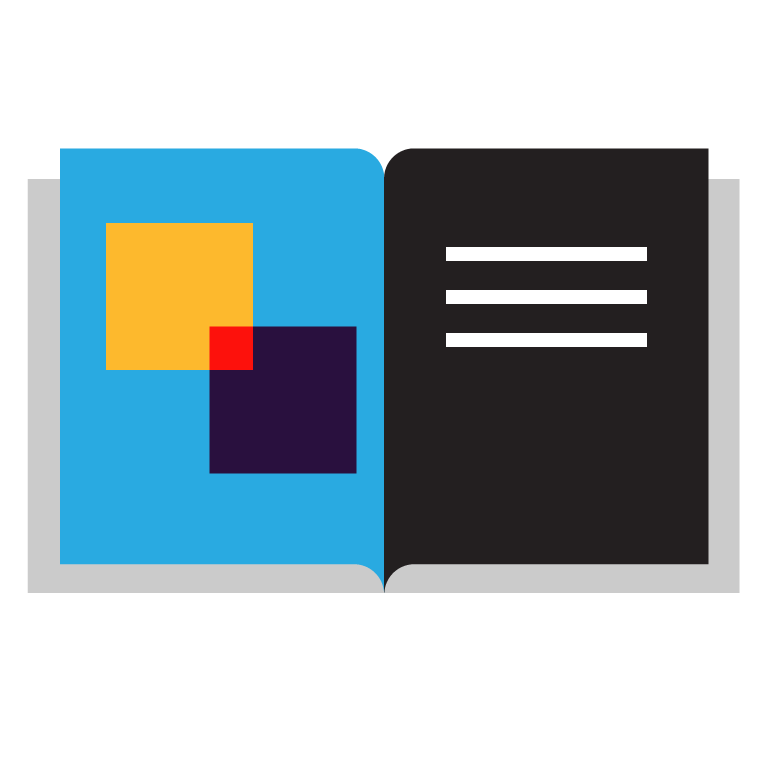