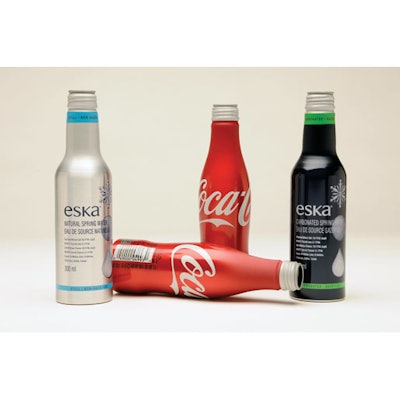
New Coil-to-Can (C2C) technology from Exal Corp. and Alcoa Rigid Packaging allows for the manufacture of eye-catching, resealable, shaped aluminum bottles at substantially higher line speeds and with 30% to 40% less weight than previously achievable, making them a viable option for higher-volume beverage applications (see packworld.com/article-28201). “The marketing world loves the aluminum bottle,” says Ed Martin, business development manager for bottle manufacturer Exal. “A lot of people like what you can do graphically, as well as with shaping. But from the standpoint of cost and sustainability, there are some challenges to the bottles because of the way they have been made using impact extrusion.”
C2C is a hybrid technology developed by Exal through an investment of eight years and many millions of dollars that combines the speed of traditional canmaking with the shaping abilities of the aluminum-bottle impact extrusion [IE] process. For enhanced sustainability, C2C also allows the bottles to be made from up to 65% post-consumer recycled aluminum alloy, compared with the 99.7% pure virgin aluminum required for IE. Alcoa supplies the raw-material aluminum coil used to make the container.