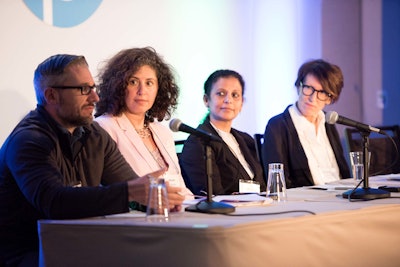
Among the barriers are higher costs, less-than-equal performance, availability of feedstock for commercial scale, and an underdeveloped infrastructure for recycling, composting, and incineration, not to mention the lack of markets for reused materials.
Suppliers offering bioplastic solutions painted a bleak picture of the current state of the industry at the Sustainable Packaging Coalition’s “Bioplastics Converge” conference held in Washington, DC, June 1, 2017. Observations shared include these:
• 685 billion pounds of plastic are produced each year. For every ton of plastic produced, two tons of carbon are released into the atmosphere.
• This takes approximately 190 million barrels of petroleum products used as feedstocks.
• Only about 25% of plastics made is used for packaging, but 75% of plastic pieces produced are packaging materials.
• Only 8% of plastics in North America is recycled. Three percent of plastic waste is collected for recycling worldwide.
• 35 billion water bottles are discarded each year. There is increased public scrutiny on plastics and the growing problem of ocean pollution.
• Plastic use has increased 20 times over the past 50 years and is expected to double over the next 20 years.
And while our infrastructure to collect, compost, recycle, and re-use may not be very robust, at least developed countries have some sort of system. On the other side of the world, India, Philippines and Indonesia are dumping plastic straight into the ocean at the rate of a truckload per minute. By 2025 estimates are this will grow to four truckloads per minute. Besides the islands of plastic refuse floating in our oceans, the sea is also contaminated with tiny plastic particles.
This alarming status report on plastic and plastics in packaging, albeit delivered by suppliers who are offering a bio-alternative, is unsettling to say the least. Each supplier stressed that a future like this is truly unsustainable.
Innovative packaging designs, including “no packaging” options, are being explored by many. The need for bio-based materials and bio-laminations is undeniable.
Major CPGs and packaging materials companies like 7th Generation, Tetra-Pak, Pepsi-Co, and Mars came to share success stories and discuss continued challenges at Bio Convergence, hosted by Sustainable Packaging Coalition.
Rachel Goldstein, Global Sustainability Director for Scientific and Regulatory Affairs for Mars, set the stage by reminding everyone that packaging plays but a part in the sustainability picture. Ingredients sourcing produces the vast majority of carbon footprint for Mars, with manufacturing sites and logistics another big segment according to Goldstein.
Mars’ commitments include sustainable ingredient sourcing, and zero fossil fuel energy use and greenhouse gas emissions by 2040 in production plants and the supply chain.
Mars is also committed to working towards 100% recyclability of packaging by 2025 but recognizes it needs to build partnerships to improve recovery efforts, according to Goldstein. This was a common theme with many of the speakers and makes sense with statistics that show so little plastic is being collected for recycling. Some speakers mentioned the burden of finding and developing after markets for their recycled content.
Mars also is addressing deforestation in the pulp and paper supply chain and wants to optimize packaging to reduce carbon footprint. Clearly bioplastics is one way to do that.
Mars has a variety of pack formats, including multi-layer pouches that include both paper and plastic layer substrates. When it comes to packaging, it’s all about recyclability, recoverability, and carbon reduction, including removing aluminum layers with bio-laminate structures to drive carbon down, said Goldstein.
2025 is the target for Mars’ current recyclability goals, but there are lots of challenges in the various pack formats depending on product packaged and food freshness and safety requirements. Another complexity of sustainable packaging is there is no one solution, as every product and package has its own journey.
Seventh Generation’s Derrick Lawrence says his firm wants to maximize post-consumer recycled (PCR) content of all packaging, and he says the firm intends to pursue bio-based materials when PCR content is not available. Seventh Generation is also committed to “right design” of their distribution packaging.
Lawrence, Seventh Generation’s Director of Packaging Development, talked about their 100-oz laundry detergent bottle made with 80% PCR HDPE, 17% bio HDPE, and 3% colorants. According to Lawrence, they had to turn to bio HDPE because any more than 80% PCR content resulted in cracked bottles.
This theme of bio-laminates sharing more traditional structural layers and combinations of different types of materials seems to hold the most promise.
PepsiCo’s Sri Narayan-Sarathy, Senior Principle Scientist, says, “packaging contributes significantly to our carbon footprint.” She shared PepsiCo’s corporate vision, “performance with purpose.” This vision promises top-tier financial performance by integrating sustainability into the business strategy in the long term.
PepsiCo, like Mars, takes a holistic approach that includes sustainable farming initiatives, improvements in water use efficiency, and 20% reduction in greenhouse gas emissions from production and logistics. By 2025 the firm plans to send no waste from direct operations to landfill, to design packaging that is recoverable and recyclable, and to support increased recycling rates.
Packaging specific, PepsiCo is working to develop the next generation of materials, mostly renewable, bio degradable materials suitable for industrial composting conditions.
Elizabeth Comere, who serves as Director Environment for Tetra Pak U.S. and Canada, said Tetra Pak, Inc. USA, has been using bio-based polymers since 2012, including bio-based HDPE (high density polyethylene) and LDPE (low density polyethylene) that come from a non-food material derivative of sugar cane for beverage caps. To add to the complexity of the sustainability equation, according to Comere, sugar cane needs to be harvested and processed in a sustainable way as well, and Tetra Pak is working with a certifying organization called Bonsucro. These bio-based caps have identical appearance, functionality, and recyclability as former caps, a key deliverable necessary for bioplastics, and Tetra Pak has increased from a half billion bio-based caps in 2012 to 2.7 billion caps in 2015.
Bio-based coating of beverage carton wall layers, again in combination with more traditional plastics, has also been a success at Tetra Pak. In 2015, fifteen billion beverage cartons had bio-based PE coating.
A combination of fiber and bio-based materials bring cartons up to 88% renewability. The idea at Tetra Pak is to innovate the package without compromising the recyclability of cartons, said Comere.
Today, fifteen years after McDonough and Braungart published Cradle-to-Cradle: Rethinking The Way We Make Things, and ten years after Packaging World’s own The Field Guide To Sustainable Packaging, many major global corporations are committed from the very top down throughout the organization to cost-efficient, sustainable business practices. And it’s become clear that packaging is only a portion of their focus.
Suppliers are offering a wide array of innovative bio-based products sourced from sugar cane, corn, potatoes, etc., to help CPGs meet the packaging portion of their sustainability goals. But the challenges are daunting. There have been great strides in down-gauging flexible packaging, for instance, which is generally seen as a positive step to reduce material consumption. Unfortunately, our current infrastructure still sends those films to the landfill. Right now, closed-loop recycling of films is not viable.
Transitioning from rigid materials to flexible materials changes the value of the recycling equation. A flexible package loses value as soon as it’s opened. Mars is working on film solutions, says Rachel Goldstein, and it looks like bio-polymers will play at least a part in the laminate structure.
Tetra Pak’s success with sugar cane feedstock for caps is hampered by supply challenges, Comere shared with the audience, making it difficult to scale up to full commercial production. For the bio-cap Tetra Pak only found only one supplier who could meet scorecard standards and had a hard time getting a consistent supply. Comere echoed that Tetra Pak agrees there is also a significant infrastructure gap for collection and recycling and more development is needed.
Emerging markets pose unique problems of their own. India, claimed by some reports to be responsible for 60% of plastics dumped into the ocean, is banning plastics in major cities and remains a huge challenge for CPGs. India needs a composting infrastructure for sustainable packaging to succeed.
Ultimately, sustainable packaging has to make financial sense, and this is still the primary barrier holding back more progress. Some suppliers have shelved phase-two launches due to weak adoption of phase one bio materials. Even Seventh Generation, totally committed to being green, may be able to charge conscientious consumers a premium, but also has to take on the added burden of having to educate the public about bio-polymers, not an easy story to tell, said Derrick Lawrence.
Performance issues remain as well. Some attempts at a more sustainable package fail to deliver food quality or safety requirements. Often production needs to be tweaked. Bio-polymers can be moisture-sensitive, and some CPGs are struggling with that issue as well.
If the bio-based package cannot deliver equivalent properties at the same or reduced cost, all the science in the world is not going to put that package into production.
Having to find a market and build a supply chain for recovery, recycling, and reuse of bio-polymers is a tall order, even in the developed world. This, perhaps, is the most disappointing aspect of the current state of affairs for sustainable packaging.
But the suppliers and CPGs who belong to the Sustainable Packaging Coalition are committed to continue experimenting. The combination of traditional materials and bio-polymers in a multi-layered lamination structure yields untold combinations, and scientists are constantly at work trying to find that magic combination.