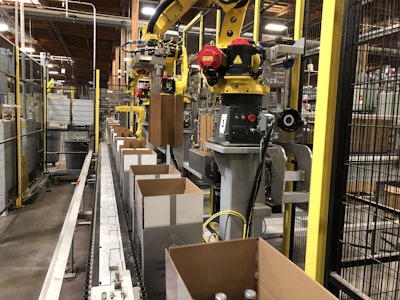
Nestled alongside the Columbia River in eastern Washington, Columbia Crest winery opened its doors in 1983. Since then, it has grown from a small winery in a relatively unknown wine region to one of the most significant wineries in the U.S. and a major force behind Washington state’s emergence as a world-class wine region. Now owned and operated by Ste. Michelle Wine Estates, Columbia Crest has a facility that spans 900,000 sq ft and houses four packaging lines that together produce more than 6 million cases of wine annually.
In its early days, Columbia purchased all of its empty glass bottles in kits, with bottles supplied prepacked in corrugated cases with the partitions already inserted. In 2007, when it made the switch to bulk glass for one of its lines (there were three at the time), it needed a way to insert the partitions after case packing. While there weren’t a lot of companies at the time that supplied equipment for this process, it did ultimately find a mechanical partition inserter that handily met its needs—for a while.
Over the years, as demand grew for its wines, Columbia updated the packaging equipment upstream from the partition inserter to accommodate increased production. Eventually, as Vice President – Operations for Ste Michelle Wine Estates Eric Brinkworth explains, the mechanical inserter became a bottleneck, unable to keep up with the increased line speeds. Another major issue was the time it took to change over the machine for different partition sizes—Columbia produces six- and 12-ct cases of 750-mL and 1.5-L bottle sizes on the line.
With the installation of its fourth line in 2014, Columbia Crest had opted for a robotic partition inserter from Pearson Packaging Systems, rather than a mechanical one. Having had great success with this option, it looked for a similar solution to replace its mechanical inserter. For this application, it needed a compact footprint and flexibility for different case configurations. “What we look at when we purchase equipment is what we currently run for case configurations, but then we also try to look ahead and predict what other potential case configurations we may need in the future,” explains Brinkworth. “Then we try to have the machinery set up to have the flexibility to run different case configurations—whether it be bottle sizes, such as 375 or 750 milliliters or 1.5 liters, or six or 12 packs—for future potential needs.”