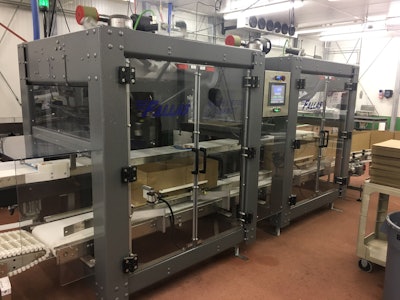
Recent shortages in labor—both skilled and unskilled—have been a major catalyst for automation in many packaging companies, and Lisanatti Foods of Oregon City, OR, is one of them. As Jeff Lisac, President of the food manufacturing company shares, in his home state, this challenge has been compounded by rising minimum wage rates.
“With labor costs going up, minimum wage is raised every six months in Oregon,” he says. “By 2020, it’s probably going to be about 15 to 18 dollars an hour.” This, he says, is what forced the company to turn to robotic automation of its case-packing operations—a move that not only allowed the company to save on labor costs, but also increase productivity and packaging quality as well.
Lisanatti was founded in 1976 by Phil and Norma Lisac as one of only two providers of imitation mozzarella for the pizza industry. Today, the family-owned business is focused on producing high-end, health-focused vegetarian cheese alternatives made from soy, rice, or almonds. Lisanatti supplies chunks, shreds, and slices under its own name as well as for three private-label brands, supplying product to foodservice companies, to food manufacturers as an ingredient, and to more than 6,000 retail stores in the U.S. and several hundred in Columbia.
Its point of differentiation, says Lisac, is the process it uses, which results in a product that has a much closer body and feel to traditional dairy cheese. “There are a lot of companies out there that make good products,” he says. “I just believe with the texture and profile of our products, we have an edge over most of our competitors.”
Given its range of customers and product types, the company handles several packaging formats. For wholesale, it supplies a 30-lb bag-in-box format for frozen bulk cheese, and 4- and 5-lb bag-in-box packs for fresh or frozen shredded product. On the retail side, Lisanatti offers 8- and 12-oz pouches of shredded cheese, and 8-oz vacuum-packed chunks that go into 12-, 18-, and 24-ct boxes. The bags for its shredded products are preprinted, while the chunks receive machine-applied labels. Lisanatti also offers a soy cheddar slice product that is co-packed.
The company has one manufacturing line and five packaging lines. Before Lisanatti automated case packing, the process was done manually, with operators having to tear down and set up equipment at the end of each packaging line every time they had to pack a different product. This involved changing over the case erectors, sealers, and labelers to accommodate different package formats and configurations, a process that could take an hour to an hour and a half. By Lisac’s estimates, the company lost up to 15 hours a week in productivity due to changeovers. Also, depending on the product, the number of operators required for the job changed as well. For example, two operators were needed to pack 8-lb bags running at 30/min, while four were required for an 8-oz product at 70/min.
“We had wanted a case packer for many years, but we never found one that was versatile enough where we could buy just one and feed all our lines into it,” says Lisac. “Most of the equipment out there involves elaborate setup from one size to the next, and it takes too much time and too many adjustments.”
The other drawback was cost. “We looked at automating our packaging line in the past, but financially, we just couldn’t justify it,” Lisac says. In 2017, with labor costs getting out of control, Lisanatti felt it had no choice but to investigate automation in earnest.
Among its requirements for the equipment were a small footprint, the flexibility to handle different products, package formats, and case sizes, and speeds to 120/min. On the recommendation of Curt Garrett, President of Garrett Packaging Systems, a Fallas Automation distributor, Lisanatti selected a robotic case-packing system from Fallas, the R700 Adabot.
The R700 Adabot is a modular system that can operate up to four robot cells using a single automation controller—hence “add” a ’bot. For Lisanatti’s purposes, it chose a Double Adabot, or two delta pick-and-place robots, to ensure the system met the required speed while still running at only 75% to 85% capacity, providing room to grow. “And if we need more speed later, we can just purchase another robot, which is really a time and money saver,” says Lisac.
The case packer handles product from four packaging lines, with the outfeed conveyor of each line feeding one main infeed conveyor. “The conveyors that feed the main infeed overlap each other, and there are bridges that you either raise or lower to determine which line is going to feed the machine,” Lisac explains. “Now, you can’t feed the machine all the different products at the same time, but within a matter of 15 minutes, you can shut one line down and open the next line up.”
Case sizes range from 8 x 11 x 3 in. to 11½ x 17 x 13 in. According to Lisac, changeover from one case size to another involves selecting a program on the case packer’s user interface, making four or five box-size adjustments, and moving a couple of rails and stops.
With the exception of the shred line, which uses preprinted film, each packaging line has its own labeler. Once products are packaged and labeled, they are conveyed through a metal detector, over a checkweigher, and into the Adabot. Here, the leading, or first, robot in the cell fills a waiting case with half of the product, after which the case is conveyed to the trailing robot, which loads the rest of the product. For example, for a 12-ct case, the first robot would load six packs, and the second robot would load the remaining six.
The end-of-arm tooling for the robots is a vacuum hose fitted with a silicone suction cup engineered to accommodate Lisanatte’s product and packaging in particular. “The choice of tooling was critical for our product specifically,” says Lisac. “We don’t cut to exact sizes, we sell exact weights, which means, when we cut it through our cheese harps, we have to give away a certain amount of cheese to make sure we don’t get hit by state weights and measures. So, all of the eight-ounce blocks are inconsistent in shape.
“That creates a problem with label placement and with proper indexing, because the packs hit each other and go crooked. Another problem is that the chunk product is packed on a vacuum machine that heats and forms the film. Until the package is a day or two old, the corners are still very sensitive. So all the conveyors supplied by Fallas and the robot’s suction cups have to handle product pretty gently or it will create a leaker. If you ding or scratch a corner or drop a package, it’s immediately rejected because we just assume, because of experience, that it’s going to be a leaker.
“Flexible bags are actually easier to handle, but they’re harder to load. It doesn’t matter if you flex them and move them, because they’re pretty sturdy, but they’ll fall crooked into the case when loaded, and the cheese will then fall crooked in the bag. Therefore, precision picking and placing is required when the Adabot is loading the pouches into the case.
“Having the packaging machine handle both flexible bags and hard-chunk cheese was pretty difficult. We had to have several different suction cups to facilitate all the different packages.” Since it began using the Adabot in June 2017, however, Lisanatte has learned how to use one head for three of the products, changing it out only when running the 5-lb bags.
To say Lisac is pleased with the decision to automate would be an understatement. According to him, it has “revolutionized” the company’s entire production system, beginning with the ease with which it can now move from case-packing one product to another, without having to tear down and set up a new system each time. Because of this, the company also has the flexibility to produce shorter runs, when needed. For example, if an order is not able to be completed due to a machine malfunction or time constraints, Lisanatte can go back and run a line for 15 minutes to an hour just to fill the purchase order, and can then switch back to another product.
The addition of automation also resulted in five operators being moved to other areas of the line, which Lisac says has led to higher quality control, as there are more eyes on the product. He adds, “People are actually a little bit more motivated now, because they don’t have to do as much manual labor. They get to monitor and look at things and work in conjunction with the robots. It’s been an amazing process.”
Lisac estimates that quality has also been enhanced 30% to 40% by having a machine pack the products rather than humans. To ensure the machines run at capacity, Lisanatte increased its case sizes to accommodate the packaged product perfectly. This has resulted in a lower leak rate, a better fill rate, and lower case-weight rejects.
Lisac also says that with the speed and versatility of the machine and the money and labor the robot has saved the company, Lisanatte will be able to pay off the system within 18 months with the savings alone. He adds, “There is one other thing that’s intangible, and until you work with Fallas, you can’t really tell how great it is. Those guys promised me a turnkey case packer with my production line, and literally we were running almost at speed the first week we turned it on. That’s unheard of.
“I’ve been doing this for 37 years, and I’ve bought a lot of machinery, and everybody swears it’s turnkey. And I’m telling you, I’ve never seen anything turnkey in my 37 years. We always have to modify something that doesn’t work, or something is wrong. This equipment was delivered, set up, and in the first week, we were running almost at speed. About three months later, after we had dialed it in properly, we had it to the point where we were getting more speed out of it than they even thought we could.”
See all case studies in Part I of the Robotics Special Report.