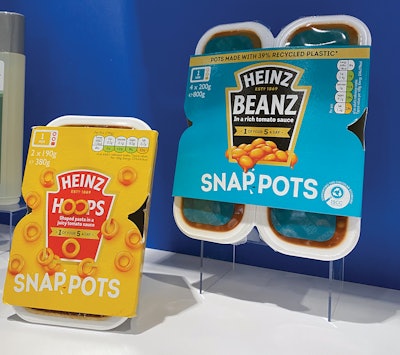
Heinz and Tesco in the UK are collaborating with Berry Global in a first-of-its kind project to permit the advanced (chemical) recycling of flexible film packaging dropped off by customers at Tesco’s in-store collection points. Also on the team are recycling technology experts Plastic Energy and SABIC, and together the team has launched a pioneering trial with the development of new Heinz Beanz Snap Pots that incorporate 39% ISCC PLUS-certified recycled flexible film.
According to Berry, the flexible films collected in Tesco’s stores are taken to Plastic Energy and physically segregated for conversion by pyrolysis—the thermal decomposition of materials at elevated temperatures in the absence of oxygen—into an optimal oil feedstock. This feedstock, which Plastic Energy calls TACOIL, is combined with virgin material by SABIC to produce an alternative feedstock for making food contact-approved plastic pellets. These pellets are sent to an ISCC-certified Berry Global site and combined in a coextrusion of PP/EVOH/White Masterbatch/PP-based adhesive. Then comes thermoforming, also by Berry. After Heinz fills and lids the pots, they undergo thermal treatment at 121˚C for about 30 minutes to render them shelf stable at ambient temperatures.
“This is a prime example of an innovative advancement in circular packaging design made possible by collaboration across the entire value chain,” says Berry’s Galvez. “This approach helps capture and reuse plastics that currently go unrecycled, to keep materials in use and out of our oceans and landfills.”
The 50/50 joint venture between London-based Plastic Energy and Saudi-based SABIC is fascinating to say the least. It’s called SPEAR (SABIC Plastic Energy Advanced Recycling BV), and it’s being executed with a Top Sector Energy Subsidy from the Ministry of Economic Affairs in the Netherlands. That country, specifically the town of Geleen, is also the site of the new production facility. SABIC and Plastic Energy have worked together with leading customers and converters to produce and commercialize certified circular polymers since early 2019. But with the Geleen facility in commercial operation, SABIC can significantly upscale the production of certified circular polymers to provide customers with greater access to sustainable materials that have been recycled, repurposed, and produced in a way that can provide a drop-in solution that helps protect the planet’s natural resources.