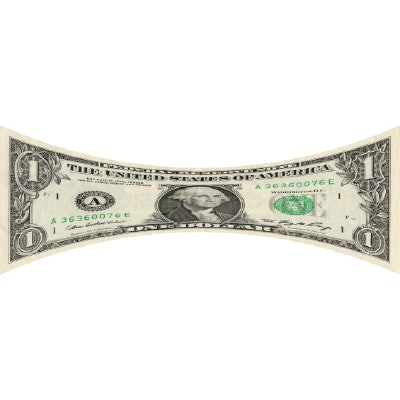
The good news: Consumer packaged goods companies know that stretch film is the most cost-effective method for securing palletized loads.
The bad news: Too few packagers take steps that would make their use of stretch film even more cost-effective. Consequently, the loads enter the supply chain, already having imposed upon the shipper avoidable costs and losses in productivity. The loads also can pose problems for other members of the supply chain.
Typically, stretch wrapping is the last value-added operation performed on a load prior to shipment. Time then to reap the efficiencies that palletizing brings to storage, material handling, transportation, and inventory control. Time then to reap the benefits that stretch film affords over other methods of securing the load to a pallet.
Right? Right, but with this proviso: In these times of economic and competitive challenges, full measures should be sought from all the company’s operations.
Not a commodity
Stretch film is an engineered material, diversified along gauge, tensile strength, puncture-resistance, tear-resistance, optical qualities, cling, etc., owing to the manufacturing process (blown or cast) and to formulations (additives). As with any engineered material, its optimal use is predicated on the proper matching between the material’s properties and the requirements of the application. That translates to choosing a film that gets the load to its final destination, in an acceptable condition, cost-effectively.
Not all procurement policies reflect these realities. Although some policies might not be as myopic as“Stretch film is stretch film,” they still miss the larger picture. A contributing factor is that distributors account for a considerable portion of the sales volume of stretch film, and many of them don’t provide technical advice beyond basic product literature. They stock films from various manufacturers and mostly leave it to the shipper to specify what’s needed.
There also is a familiarity factor that can work against the shipper. Stretch film dates back to the 70s with some shippers having made few revisions in how they order it. Likely, those shippers utilize a single metric, for example, price-per-weight measure or price-per-length measure. While convenient, such metrics don’t capture the aforementioned matching between material and application and therefore don’t reveal the true cost of the film.
On sustainability
A common practice is the use of stretch film in combination with a reduction in corrugated board. Regular slotted containers, for example, are replaced with styles that are more open; or corrugated containers are eliminated altogether, and tier separators and angle boards are used to give the load its geometry. Either way, the less corrugated-intensive load is unitized with stretch film. Yet, sustainability is a relative claim, not an absolute one, and should be quantified. All of that is to say that a shipper unknowingly can be paying too much for its green initiatives.
Is the assumption of sustainability based on weight reduction—film being lighter than corrugated? Such is not a complex consideration compared to what a Life Cycle Assessment (LCA) would entail; even so, decisions based on weight are not without potential pitfalls. The cost benefits—remember that sustainability acknowledges the profit motive—due to weight are reduced if the shipper uses more film than necessary. Also reduced are benefits due to stretch film being less expensive per square area than corrugated.
Throughout public warehouses and private distribution centers (DCs) sit pallet loads that resemble, for all their wrapping, mummified monuments. The shippers seemed willing to erron the side of caution for the sake of load protection, stability, and safety. But why overdo it, when something as simple and affordable as a shaker-table test can give direction on how much film is sufficient?
In those same warehouses and DCs are examples of the opposite extreme: loads that are partially off the pallets, leaning, or otherwise evidencing insufficient (or the wrong type of) stretch film. This is not in compliance with sustainability and is false economy, more than offset by product damage; poor shipper image; additional labor to fortify the load prior to sending it to its next stop; accidents and injuries; and customer dissatisfaction.
Even if the amount of stretch film used is the theoretically minimum-amount needed for a specific application, there remains the issue of disposal. Stretch film can be recycled into products such as plastic lumber and certain grades of bags, both of which are not affected by composition differences among films.
A shipper can enhance its green credentials and generate a modest revenue stream by recycling its on-site stretch-film wastes. The shipper also can promote the practice down the supply chain, especially if members include the retail industry. Walmart’s system of bales of film sandwiched between corrugated board exemplifies retail’s commitment to diverting the film from landfills.
Criteria and technology
To regard stretch film as low-tech is to forfeit opportunities to customize the material’s capabilities to a specific application. Besides, to the traditional comparisons between cast and blown has been added a new family of films called metallocene, promoted as a superior hybrid, given price and performance. Whether such a promotion is justified, time will tell. What needs no waiting is the recognition that the efficient, cost-effective use of stretch film has a technology component.
The application criteria include, logically, such load characteristics as weight, size, shape, uniformity, stacking patterns, and value. Also to be factored into the equation is the supply chain profile, in terms of the conditions and physical forces under which the load will be handled, stored, and transported. Other criteria are of more recent vintage; for example, the growing trend of using scanning technologies at the pallet-load level places a premium on a stretch film’s clarity.
Criteria also stem from internal operations. An example is the noisy unwind of blown film, a tradeoff against the film’s positive properties; but the tradeoff might need to extend beyond the film. Depending on the location within the facility, the screeching of the film, along with other ambient noises, can combine for hazardous levels. Long-term hearing loss is a possibility. In the immediate sense, background noise can interfere with safety sounds, notably the warning alarms of forklift trucks. There are ways to avoid the cost-related consequences, but not if the underlying conditions go unrecognized.
Equipped for the job
Notwithstanding all the discussions to this point, stretch-film capabilities only can be fully exploited through the proper matching with stretch-wrapping equipment. One example illustrates this best: A film’s capacity to be prestretched is a key determinate of its load force (how tightly it retains the load), its yield-per-roll, and ultimately, the cost to wrap a load at a specified load force—all of which are dependent upon the equipment’s ability to perform the prestretch consistently and at productive rates. In other words, the cost-effectiveness of stretch film can’t be derived independent of costs associated with the acquisition, operation, and maintenance of the equipment that applies it.
Stretch-wrapping equipment will be the topic of the next column in April.
Before becoming a packaging consultant, Sterling Anthony worked for Fortune 500 food, healthcare, and automotive companies, and has taught packaging at the university level. He welcomes your comments by phone, 313/531-1875 or by e-mail, [email protected]. His Web site is www.pkgconsultant.com.
The bad news: Too few packagers take steps that would make their use of stretch film even more cost-effective. Consequently, the loads enter the supply chain, already having imposed upon the shipper avoidable costs and losses in productivity. The loads also can pose problems for other members of the supply chain.
Typically, stretch wrapping is the last value-added operation performed on a load prior to shipment. Time then to reap the efficiencies that palletizing brings to storage, material handling, transportation, and inventory control. Time then to reap the benefits that stretch film affords over other methods of securing the load to a pallet.
Right? Right, but with this proviso: In these times of economic and competitive challenges, full measures should be sought from all the company’s operations.
Not a commodity
Stretch film is an engineered material, diversified along gauge, tensile strength, puncture-resistance, tear-resistance, optical qualities, cling, etc., owing to the manufacturing process (blown or cast) and to formulations (additives). As with any engineered material, its optimal use is predicated on the proper matching between the material’s properties and the requirements of the application. That translates to choosing a film that gets the load to its final destination, in an acceptable condition, cost-effectively.
Not all procurement policies reflect these realities. Although some policies might not be as myopic as“Stretch film is stretch film,” they still miss the larger picture. A contributing factor is that distributors account for a considerable portion of the sales volume of stretch film, and many of them don’t provide technical advice beyond basic product literature. They stock films from various manufacturers and mostly leave it to the shipper to specify what’s needed.
There also is a familiarity factor that can work against the shipper. Stretch film dates back to the 70s with some shippers having made few revisions in how they order it. Likely, those shippers utilize a single metric, for example, price-per-weight measure or price-per-length measure. While convenient, such metrics don’t capture the aforementioned matching between material and application and therefore don’t reveal the true cost of the film.
On sustainability
A common practice is the use of stretch film in combination with a reduction in corrugated board. Regular slotted containers, for example, are replaced with styles that are more open; or corrugated containers are eliminated altogether, and tier separators and angle boards are used to give the load its geometry. Either way, the less corrugated-intensive load is unitized with stretch film. Yet, sustainability is a relative claim, not an absolute one, and should be quantified. All of that is to say that a shipper unknowingly can be paying too much for its green initiatives.
Is the assumption of sustainability based on weight reduction—film being lighter than corrugated? Such is not a complex consideration compared to what a Life Cycle Assessment (LCA) would entail; even so, decisions based on weight are not without potential pitfalls. The cost benefits—remember that sustainability acknowledges the profit motive—due to weight are reduced if the shipper uses more film than necessary. Also reduced are benefits due to stretch film being less expensive per square area than corrugated.
Throughout public warehouses and private distribution centers (DCs) sit pallet loads that resemble, for all their wrapping, mummified monuments. The shippers seemed willing to erron the side of caution for the sake of load protection, stability, and safety. But why overdo it, when something as simple and affordable as a shaker-table test can give direction on how much film is sufficient?
In those same warehouses and DCs are examples of the opposite extreme: loads that are partially off the pallets, leaning, or otherwise evidencing insufficient (or the wrong type of) stretch film. This is not in compliance with sustainability and is false economy, more than offset by product damage; poor shipper image; additional labor to fortify the load prior to sending it to its next stop; accidents and injuries; and customer dissatisfaction.
Even if the amount of stretch film used is the theoretically minimum-amount needed for a specific application, there remains the issue of disposal. Stretch film can be recycled into products such as plastic lumber and certain grades of bags, both of which are not affected by composition differences among films.
A shipper can enhance its green credentials and generate a modest revenue stream by recycling its on-site stretch-film wastes. The shipper also can promote the practice down the supply chain, especially if members include the retail industry. Walmart’s system of bales of film sandwiched between corrugated board exemplifies retail’s commitment to diverting the film from landfills.
Criteria and technology
To regard stretch film as low-tech is to forfeit opportunities to customize the material’s capabilities to a specific application. Besides, to the traditional comparisons between cast and blown has been added a new family of films called metallocene, promoted as a superior hybrid, given price and performance. Whether such a promotion is justified, time will tell. What needs no waiting is the recognition that the efficient, cost-effective use of stretch film has a technology component.
The application criteria include, logically, such load characteristics as weight, size, shape, uniformity, stacking patterns, and value. Also to be factored into the equation is the supply chain profile, in terms of the conditions and physical forces under which the load will be handled, stored, and transported. Other criteria are of more recent vintage; for example, the growing trend of using scanning technologies at the pallet-load level places a premium on a stretch film’s clarity.
Criteria also stem from internal operations. An example is the noisy unwind of blown film, a tradeoff against the film’s positive properties; but the tradeoff might need to extend beyond the film. Depending on the location within the facility, the screeching of the film, along with other ambient noises, can combine for hazardous levels. Long-term hearing loss is a possibility. In the immediate sense, background noise can interfere with safety sounds, notably the warning alarms of forklift trucks. There are ways to avoid the cost-related consequences, but not if the underlying conditions go unrecognized.
Equipped for the job
Notwithstanding all the discussions to this point, stretch-film capabilities only can be fully exploited through the proper matching with stretch-wrapping equipment. One example illustrates this best: A film’s capacity to be prestretched is a key determinate of its load force (how tightly it retains the load), its yield-per-roll, and ultimately, the cost to wrap a load at a specified load force—all of which are dependent upon the equipment’s ability to perform the prestretch consistently and at productive rates. In other words, the cost-effectiveness of stretch film can’t be derived independent of costs associated with the acquisition, operation, and maintenance of the equipment that applies it.
Stretch-wrapping equipment will be the topic of the next column in April.
Before becoming a packaging consultant, Sterling Anthony worked for Fortune 500 food, healthcare, and automotive companies, and has taught packaging at the university level. He welcomes your comments by phone, 313/531-1875 or by e-mail, [email protected]. His Web site is www.pkgconsultant.com.