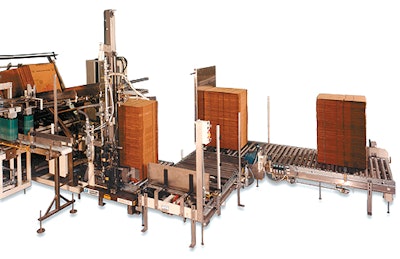
Usually, when a federal agency threatens regulatory action, packaging executives put their hands over their heads and put their chins between their knees. New regulations normally land on them with a crash. But the Occupational Safety and Health Administration’s announcement in April that it will be issuing guidelines for various industries on how to avoid repetitive motion injuries drew applause from at least one packaging engineer. “It will make my job easier,” says John Hunt, packaging equipment engineering specialist at 3M Co., St. Paul, MN.
It is Hunt’s job to convince managers at 140 3M plants around the world that they ought to spend $50ꯠ or $200ꯠ or whatever on new packaging equipment in order to make the packaging line more efficient or safer or, frequently, both. And it is often a hard sell, not only for Hunt, but for other packaging engineers who no longer, as in the old days, can point to mangled fingers and hands damaged by punch presses as a way of persuading corporate executives that new machinery is unavoidable. “Ergonomic injuries are more insidious,” says Hunt. “They’re not as traumatic or visible.”
Yet there are signs of change. In the 2002 Packaging Machinery Purchasing Plans Survey, conducted by the Packaging Machinery Manufacturers Institute (Arlington, VA), 5% cited ergonomics safety as the primary reason for a machinery purchase. This was the first time that category showed up on the survey, according to Hunt. “I thought that was quite dramatic,” he says.
The hidden costs
Some companies that buy packaging equipment for ergonomic reasons are moved by potential healthcare savings. Conservative estimates of the economic burden imposed by work-related musculoskeletal disorders, as measured by compensation costs, lost wages, and lost productivity, range between $45 billion and $54 billion annually, according to the preamble to a bill introduced by Sen. John Breaux (D-LA).
Breaux’s bill would force OSHA to issue an ergonomics standard instead of the voluntary industry guidelines OSHA administrator John Henshaw announced in April. The agency has said the first three guidelines will affect nursing homes, poultry processing plants, and grocery stores.
3M’s Hunt welcomes the guidelines because he believes that the packaging-specific guidelines, whenever they come out—and any timetable is so far uncertain—will make it easier for him to persuade upper management that a plant needs to buy equipment such as case packers. “We feel we at 3M are ahead of a lot of other companies in terms of working to decrease repetitive motion injuries,” states Hunt. “But ergonomics is still sometimes a hard sell.”
OSHA has not announced a schedule for issuing guidelines for industries beyond the first three. Fred Hayes, the standards and safety coordinator for PMMI, says that OSHA may publish guidelines based on job categories, not industries. OSHA clearly picked nursing home workers first because the agency’s year-2000 data on musculoskeletal disorders shows “nursing aides, orderlies, and attendants” among the occupations with most injuries: total injuries were 45괧.
Packaging makes the list
The first packaging occupation to show up on the list, “packaging & filling machine operators,” logged in at 4갦 injuries, meaning it was outside the top 20. But two other packaging-related occupations came soon after: “hand packers & packagers” and “production inspectors and checkers.”
Those three occupational categories combined to total over 10ꯠ injuries. Together that would place them in eighth position among occupations. Nonetheless, Hayes says, “I don’t see OSHA targeting packaging jobs within the next 18 months.”
That may be true. Then again, it may not. It is worth noting that OSHA has said it “will place special emphasis on industries with the sorts of serious ergonomics problems that OSHA and [U.S. Department of Labor] attorneys have successfully addressed in prior enforcement cases, including the Beverly Enterprises and Pepperidge Farm cases.” The Pepperidge Farm case involved a food packaging line.
OSHA officials have said they want to develop guidelines that build on existing industry ergonomics standards. In the case of packaging, however, none exists. The closest standard is B155.1-2000 from the American National Standards Institute (ANSI), which is a PMMI-developed standard and applies to the manufacture of packaging equipment. It includes section 4.3 entitled “Ergonomics/Human Factors.” All that section contains is two very general sentences. It would be of no help to OSHA.
Toward ergonomics, anyway
Of course, even in the absence of OSHA guidelines, packaging lines have been heading in an ergonomically sensitive direction, as the PMMI study indicates. One executive with packaging responsibilities for a household cleaning product manufacturer says large companies have been factoring in ergonomic benefits to equipment buying decisions for a long time, even before the Clinton administration proposed an ergonomics rule.
“It is the right thing to do,” he says, explaining that his company’s legal department would not permit the company to be identified. “We want to make our production environment one that employees feel comfortable in.”
His company recently purchased Brenton Engineering’s (Alexandria, MN) Series 2 Automatic Magazine Loaders for four additional packaging lines at one of its plants. The purchase came after the system was tested previously on one packaging line. AMLs were subsequently installed in three other plants as well. The machines eliminate the need for the company’s operator to lift an armful of knocked-down corrugated boxes off a larger pile delivered by the manufacturer, stagger over to the packaging line, and hand stack that armful of slotted cases in the case erector.
The executive says the rationale for the purchase of the AMLs was “70-percent ergonomics, 30-percent labor savings.” To its credit, the company made those purchases knowing full well that it would not recover its investment—$150ꯠ per machine plus the costs for some changes in the corrugated manufacturer’s plant—in the form of reduced costs for lifting or repetitive-motion injuries.
The unidentified spokesman says the looming Clinton ergonomics regulation played no role in his company’s decision to purchase the Series 2 AMLs. Nor would Bush administration guidelines. “The bottom line is how a company is managed,” he states. Nonetheless, he acknowledges that smaller companies may be unable to afford a $125ꯠ piece of equipment no matter how well the company is managed. These are the companies that would be most affected by any OSHA guidelines.
Any guidelines would be voluntary as long as the Bush administration is in the driver’s seat. But Democrats in Congress want to get their hands on the steering wheel. Sen. Breaux has introduced legislation, which does have some Republican support, to force OSHA to ditch the guidelines approach and return to the Clinton mandatory ergonomics standard. The bill (S. 2184) would force OSHA to issue an ergonomics standard which would “cover all industries where workers are exposed to workplace ergonomic hazards and there are economically and technologically feasible measures to control these hazards.”
Whether OSHA’s bottom line on ergonomics remains guidelines or standards, the net effect will accelerate large manufacturers toward safer packaging equipment while presenting small packagers with a costly dilemma.