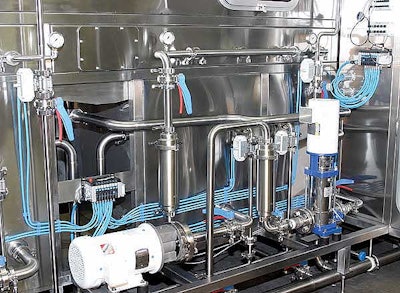
At Drink More Water in Gaithersburg, MD, a new washer/filler/capper for 3- and 5-gal polycarbonate bottles of purified drinking water has brought bottling speeds from 140 to 750 bottles/min. The increased capacity lets DMW run a single shift five days a week instead of scheduling five 18-hr days each week.
DMW president Bob Perini says the controls architecture on the AQT machine, made by Aquatyzer Engineering, heavily influenced his decision to buy it.
“It’s a very coherent electronics and pneumatics package,” says Perini. “The PLC controls everything by communicating over a ProfiBUS network with sensors, variable-frequency drives, and pneumatic valves and cylinders. Because the communications network is connected to our LAN, I can access the PLC’s software program any time I want right from my desktop computer in the office. It lets me see faults that may arise, and I see it in real time. Troubleshooting is so much easier than it was on our earlier machine.”
The PLC on the new machine is a Siemens S7300, and the pneumatic system is supplied by Festo. There are three pneumatic valve manifolds, each containing eight valves. Each valve drives a cylinder somewhere in the complex AQT machine, thus permitting it to perform its function. Aquatyzer vice president David Tye says the controls architecture on the current machine is a vast improvement over earlier models.
“In this class of machine, gears, cams, and belts running off of a common drive gave way some time ago to a broader use of PLCs and discrete I/O,” says Tye. “With the PLC in the picture, you ran all the switches and sensors back to the PLC with point-to-point wiring. But now even that has become outdated. On this machine, for example, it’s replaced by a controls architecture based on serial communication along a network. You run a twisted pair of wires from a PLC through a number of devices, and all the paired wires do is transmit data back and forth between the PLC and the devices.”
In the washer/filler/capper at DMW, there are six nodes along the ProfiBUS network. The nodes are the three pneumatic valve manifolds, two variable-frequency drives, and the HMI.
Each pneumatic valve manifold has a built-in ProfiBUS communications interface. Output signals travel from the PLC and along the ProfiBUS network to the valve manifolds, thus triggering the valves. These route pneumatic pressure to actuate the cylinders, thus driving the machine. A sensor on the cylinder sends an input back through the CPV manifold and, by way of the ProfiBUS network, back to the PLC. This feedback confirms that the desired actuation indeed took place.
Worth pointing out is that the small footprint of the Festo pneumatic valve manifolds allows them to be placed in almost any location on the machine. Also significant is that they have an IP65 rating. That makes them suitable for use in an environment where dripped, sprayed, or splashed moisture is common. As a result, Aquatizer is able to forego the use of a protective cabinet and mount the manifolds right on the machine. Not only does this cut installation time and cost, it gives operators easy access to the valve manifolds. They can’t be washed down, but they’re sufficiently water-tight for use in DMW’s water bottling plant.
Long live the network
From a machinery builder’s standpoint, says Tye, this machine’s networked controls architecture is definitely the way to go.
“If this were point-to-point communication rather than serial communication over the ProfiBUS network, you’d need at least 16 wires running from each 8-valve manifold to the PLC,” says Tye. “The other beautiful thing is that it’s not just discrete information being sent back and forth along the Profibus network. It’s not just ‘turn on’ or ‘turn off.’ You’re also getting data back from the devices saying, ‘I am/am not in good working condition.’ This opens up opportunities for real-time diagnostics and troubleshooting.”
Even the HMI is on the Profibus network. Just like the elimination of point-to-point connections between pneumatic valve manifolds and the PLC, having the HMI on the ProfiBUS network simplifies things and speeds up installation by eliminating the need to create a separate RS232 connection between the HMI panel and the PLC, says Tye.
While the controls package on the rinser/filler/
capper brings significant benefits to machinery builder Aquatyzer, the day-in, day-out beneficiary is Perini. He says the increased filling speed, the improved labor-cost picture, and the instant access to real-time machine-operations information assure him that he made the right investment.
“Let’s just say I have no buyer’s remorse,” he adds.
See sidebar to this article: Servo pneumatics brings piston-positioning information