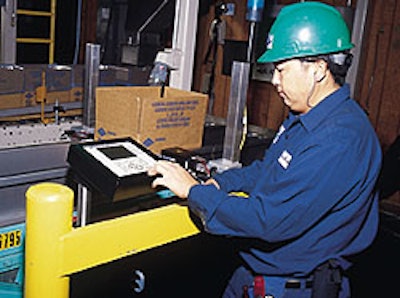
Like many companies, Blue Diamond Growers finds that it makes economic sense to continue to use older packaging machinery as long as the equipment is still effective. But when its aging case coders began to hinder operational efficiency, the Sacramento, CA-based nut cooperative replaced the units. The new case coders have reduced downtime, decreased labor costs, and virtually eliminated ink loss.
Added early last year, the six Model 5000 case coders are supplied by Markem (Keene, NH). They replace older case-coding equipment that used only liquid ink. “We had major problems with keeping the former machines running,” notes Blue Diamond development engineer Rob Brougher. “For some reason, we’d lose whole bottles of ink that would just siphon out of the reservoir, through the printhead, and out onto the floor. Each bottle cost $250. When that happened, the line was down until the mess could be cleaned up, which usually took an hour. We worked with the supplier on it, but they couldn’t figure it out.
“It was extremely messy, too,” Brougher continues. “We were using pans to catch the ink that was draining, and technicians had to wear gloves to change the printheads. They had ink on their shoes and pants, and often smudges would get on the boxes.”
He says, “We had to have a technician there a minimum of four hours a day just to handle print problems on the five machines. The technician spent most of his time trying to purge the units. We reached a point once where we were down for about a month.”
“Toward the end, we had one or two lines down permanently because we couldn’t get the coders fixed,” adds Bob Krull, systems specialist engineer.
While Blue Diamond looked to upgrade from these older coders, it still needed to print cases to ready boxes for shipment. To do so, the company “preprinted boxes with an old roller coder at our print shop that we use for other lines in our plant,” says Krull. “We had to hire labor to do that, and it also cost us a lot of time. And if we couldn’t use all the preprinted cases, we had to try to store them or throw them away.”
New units a “bargain”
Brougher tells Packaging World that the cooperative first found out about the Markem equipment at Pack Expo Las Vegas 1999. “We realized the print definition was better than that of other high-resolution units that we had considered. The graphics were pretty impressive.”
Markem coders are used on five different lines at the Sacramento facility, with a sixth unit serving as a spare. “The 5000 includes two printheads and a controller,” explains Krull. A printhead is mounted to each side of the conveyor so that when the case passes by, it’s coded simultaneously on opposite sides, “either with the same information or different details,” he points out.
“The real bargain with the Markem unit,” Krull states, “is that it prints three lines of high-resolution, large-character type, in a 2.8-inch-high area. And the unit costs $15ꯠ. We needed four printheads per side to deliver three lines of type with our old systems. Normally, high-resolution ink-jet systems only print 1.9 inches high. If we’d gone with somebody else to get this same print with the high resolution, it would have cost us at least $40ꯠ,” he estimates.
The five coders were up and running by April of last year. The lines usually run eight hours a day, five days a week during spring and summer months, and up to two eight- to 10-hour shifts during the busy September-to-March season. The coders are used mainly for 25-lb bulk boxes of almonds. Boxes are sold to industrial and foodservice accounts such as Hershey’s and M&M Mars, says Brougher. Much of the plant’s overall volume of almonds, hazelnuts, and macadamia nuts is exported.
Additional advantages
Besides the purchase cost savings, the Markem units deliver several other key benefits for Blue Diamond. The 2.8”-high print area lends flexibility. “Customers may want their own code dates, a bar code, or certain graphics,” says Krull. “We don’t print many graphic symbols now, but we have produced a kosher symbol and a special graphic for a Japanese customer.” All print is in black, with each print line about 7/8” high.
The coders are also networked to a host PC. They required little time for company technicians to learn to use. “Plus, we no longer need to run four printheads, two on each side of the conveyor, to print cases,” Krull reiterates.
Better yet, the units have virtually eliminated the ink spillage problems. Between wasted ink and cleaning up, he says the company was spending $500 per month. Now, “if there is any spill, all we need is a putty knife and broom to clean it up,” Krull relates. “That’s due to the nature of the ink.” Specifically, the coders use Markem Touch Dry inks, which are nontoxic inks designed to dry instantly.
“It’s hard to put a dollar value on the time it takes to continuously wash the ink off your hands when the ink never comes off completely, and having to wash the ink out of your clothing or replace your clothing because the ink ruined it,” he asserts.
Krull adds, “The print quality is fantastic. With regular ink-jet printing, you have 32 lines of resolution from top to bottom. With this coder, there are 256, so that increases the resolution. The better-quality print is more easily read by scanners, and it ensures that cases are sent down the correct lane, which frees up our technicians.” The equipment codes the large bulk cases, which are filled at rates of about six/min. The plant ships as many as 5ꯠ cases/day.
Brougher estimates that it cost Blue Diamond between $20ꯠ and $30ꯠ a year to keep the old units running. Since making the change, he estimates that the company saves 1ꯠ hours/year in technical service maintenance costs and between $3ꯠ and $5ꯠ in annual repair parts.
And then there’s the service improvements. In the past, Krull says, “the vendor couldn’t resolve our problems, so we were basically on our own. Now, if things go wrong, Markem responds very quickly. They have a great program where if you have a problem with a printhead, you can get [another] one the next day. Very few companies can do that. That’s a real plus, because when one goes down, you need another right away or your line is down. In the past, we had to buy so many spares because we sometimes had to wait one to three months for turnaround [of a replacement printhead].” Of course, with a spare unit, that’s presently not a concern for the nut producer.
Blue Diamond was also impressed when it installed the printers. “I’m the one who installed these,” Krull recalls. “And when we turned them on, every single one of them worked the way it was supposed to work. I don’t think I’ve ever had that happen with any other equipment I’ve installed.”
It’s no wonder, then, that Blue Diamond is satisfied with the coders. “We would like to add more printers in the future,” says Brougher. “And our plan is that anytime we need to replace a case coder, we will do so with a Markem.” He adds that the company is also looking at using other Markem machines to print codes on primary packages.