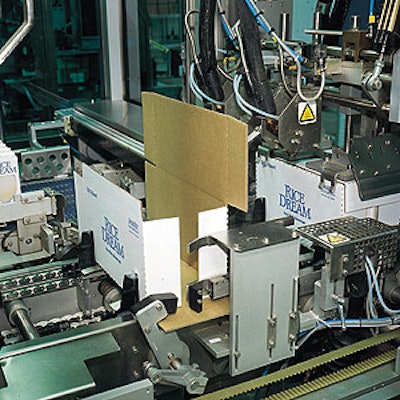
California Natural Products of Lathrop, CA, has no brand to call its own. But as a contract packager handling other brands on 10 aseptic packaging lines in a plant that runs around the clock five or six days a week, this firm is clearly among the high-volume producers of aseptic packages in the United States.
CNP’s newest equipment is found on Lines 6 and 7, both of which rely on TBA-21 roll-fed aseptic form/fill/seal machines from Tetra Pak (Vernon Hills, IL). A variety of low-acid products—teas, soy-based beverages, soups—are packaged on these lines, which are notable because the TBA-21 is one of the first aseptic systems from Tetra Pak capable of forming and filling more than one size. Among the CNP customers that benefit from this flexibility is Imagine Foods of San Carlos, CA. The company markets a variety of soy-based beverages and soups in aseptic brick packs produced by CNP. The versatility of the TBA-21 equipment played a key role in Imagine Foods’ decision to put out a 15-oz carton of aseptic soup.
“Running aseptic packaging equipment has traditionally been an inflexible, dedicated-line kind of business,” says Hans Fastre, general manager at Imagine Foods. This has discouraged food and beverage marketers from launching packages in varied sizes, Fastre says. “For example, we might never have come out with our 15-oz soup if the TBA-21 were not capable of being switched over from 32-oz to 15-oz cartons.” That’s because it would have been hard to justify the installation of a new aseptic line at CNP dedicated to 15-oz containers just because Imagine Foods wanted to try a 15-oz carton.
Imagine Foods is marketing eight varieties of its soups in a 500-mL slim format, which is filled only to the 443-mL level so that it has exactly 15 fl oz; suggested retail price is $1.99 to $2.19. The firm sells the same flavors in a 946-mL (32-oz) size for $2.99 to $3.49.
CNP can fill both sizes on either Line 6 or 7. Changeover, says vice president of operations Kevin Haslebacher, is supposed to take one day. But CNP hasn’t quite gotten there yet, he adds. “We have a learning curve here,” says Haslebacher.
Focus on Line 7
Because CNP’s new aseptic lines are nearly identical in configuration and equipment, Packaging World selected Line 7 as a focal point when visiting CNP in February.
The TBA-21 aseptic form/fill/seal machine sits at the head of Line 7. An intermittent-motion system capable of producing 120 1-L brick packs/min, it forms roll-fed material into a bottom-sealed tube and floods the tube with aseptically processed liquid. Two reciprocating heat-seal jaws continuously pull the foil/paper/plastic packaging material down, first the left jaw assembly and then the right. They do this by stroking up and closing on the tube to form the leading edge of the incoming pack and the trailing edge of the exiting pack. Then they stroke down, pulling the packaging material with them, and cut the finished pack loose onto a short transfer device that leads to another station, where final folding and tucking turns the pack into a true brick pack.
Emerging from the TBA-21, cartons are conveyed beneath a Domino Amjet (Gurnee, IL) laser coder that gives each carton top lot and date code information. “Laser coding equipment may cost 30% more upfront than small-character ink-jet equipment, which we’ve used in the past,” says Haslebacher. “But it pays for itself in reduced maintenance and downtime and by eliminating the need to buy ink.” All small-character ink-jet coders at the plant have been replaced by laser units, Haslebacher says.
Next in line is an accumulation system, a critical component in a line whose filler does not modulate its output based on downstream conditions. As Haslebacher puts it, “The filler is either on, producing 7겨 packs an hour, or it’s off.”
The first-in/first-out vertical accumulator selected by CNP is called the Tetra Helix. It was built under license by Hartness International (Greenville, SC) for Tetra Pak.
“This system brings us clear advantages over the accumulators we’ve used in the past,” says Haslebacher. “First-in, first-out is very important to our particular business, because keeping packages in sequential order aids us in our QC efforts. Another advantage is how quickly this system discharges the packages it accumulates. Previous systems we’ve used were slow to unload, which meant they would always be about half full. So the five to six minutes of package accumulation they offer is really more like three to five minutes. With this system, when they say you have 3 1/2 minutes of accumulation, that’s what you get.
“It’s a simple concept, really. A device called the ‘spider’ walks packages up a spiral conveyor as far as need be. As soon as downstream equipment is ready to take packages again, it walks containers back down. The spider is driven by the spiral conveyor. That’s where all its power and action come from.”
Pour spout applicator
Exiting the accumulator, containers are conveyed into a Tetra Pak machine that applies a plastic fitment to make the package easy to pour from and reclosable in the consumer’s hands. This machine is fed sheets of caps eight across. A strip of eight caps is cut from the sheet and fed into a device that cuts individual caps and sends them down a chute. Along the way, hot melt glue is applied and then a vacuum pick-up head picks each cap and applies it to an incoming carton.
“The sterile contents are sealed in before the package reaches this application device,” Haslebacher says. “The consumer opens the hinged plastic cap and pulls an aluminum pull tab to open the aseptic package.”
An automatic wraparound case packer from Tetra is next in line. It picks case blanks from a magazine, erects them, and then loads cartons that it has previously collated in a 2x6 pattern. Hot melt glue is used to secure the flaps, and then finished cases pass through a Model PA 5000 thermal-transfer label printer/applicator from Diagraph (St. Louis, MO).
Product ID, date, and time are printed in human readable and bar-code formats, and because labels are applied to case corners, the information can be read or scanned from two sides.
“The bar codes help us track product internally as well as helping customers with their inventory management,” Haslebacher says.
Hand palletizing is next—but not for long. Now being installed are overhead conveyors that will whisk cases from Line 7 to a remote robotic palletizing/stretch wrapping area that is impressive indeed (see sidebar, p. 53).
Robotic palletizing isn’t the only area of operations that Haslebacher plans to focus on this year. Additional package sizes also have his attention.
“We’ll continue to work with Tetra Pak as new package sizes for the TBA-21 become available,” Haslebacher says. “This will be market driven I’m sure, and we want to be able to capitalize on the versatility of the machine.”