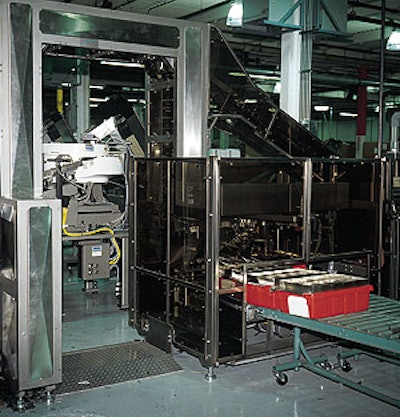
Internal “customers” can be as important as external ones. That thinking led Sanford North America Corp., Bellwood, IL, to rewrite how liquid marking pens are loaded into bulk bins by shifting to automatic bulk loading. The arrangement facilitates storage, handling, and subsequent manual unloading of the markers from the bins to various blister packaging machines throughout the plant.
Engineering manager Marc Colavitti says that bulk packaging inefficiencies in the past meant operators spent 10 to 15% of their time scooping markers manually into bins. With the new system, that’s done automatically. Also, production personnel know that there are exactly 540 Liquid Sharpie markers in each bin, all oriented in the same direction. The equipment dramatically reduced the amount of repetitive motion required of operators who load bulk containers, he adds. It also prevents them from having to reduce packaging output caused by markers that were randomly oriented.
The automatic loading of bins is part of a totally custom assembly and packaging system started up last September for Sanford’s new Liquid Sharpie permanent markers. It operates in continuous motion 24 hrs/day and is capable of speeds to 200 markers/min.
Up to 300 markers/min
It followed the June startup of a similar, but faster, system for Sharpie Ultrafine markers capable of speeds to 300/min that counts 750 markers into each bin. A third system, which can operate at speeds to 200/min and counts 360 markers into each bin, started up in December for Sanford’s Accent and Expo brand markers.
The packaging part of the operations, comprising marker conveyor, bulk loading, cartoning, and casing operations, were designed by PMI Cartoning (Elk Grove Village, IL). “Bulk loading was completely custom designed from the frame up,” Colavitti remarks. “PMI provides solidly made cartoners and case packers, but its true strength is customizing an application like this.”
These systems mark Sanford’s foray into automatic bin loading. “It was hard to figure out how to get the markers into a tote without scrambling them all up,” admits Colavitti, but figure it they did, with PMI’s assistance. After the eight months of development on the first-of-its-kind system, the second system was easy, Packaging World is told. During PW’s visit, black ink markers, by far the most popular item, were run on the Liquid Sharpie line. Other inks include red, green, and blue.
Markers are assembled from components by a highly automated, 44-station, modular system. Markers transfer from the positive control of the assembly system to that of the packaging infeed, a transfer point that was absolutely crucial, says Colavitti.
This transfer was also a major challenge, he adds, due to the different orientation of the two systems. Sanford engineers determined there was no direct way to make the transfer and still maintain positive control in the process. Instead, Colavitti explains, they devised a “waterfall” transfer system in which the markers are temporarily released from the assembly operation and then positively picked up by the packaging infeed conveyor. The point of integration also provides a sampling point. It is programmed to deliver a product sample every 10 minutes, and once daily, 100 markers are diverted for quality control testing.
Transported two-up in an upright position through the assembly system, each marker releases from the assembly machine’s grippers one after the other to provide a jam-preventing gap as they slide down a chute one after the other and enter a serpentine chute made of aluminum. This section keeps the markers horizontal as they travel down to a starwheel located near floor level. The counterclockwise-rotating starwheel picks the markers one-at-a-time at the 9 o’clock position and rotates them to the 3 o’clock position where they are transferred into a conveyor-mounted metal clip. The starwheel is mechanically timed to the clip conveyor.
Clip conveyor considerations
The clip is a stationary steel clamp that captures the marker after the starwheel transfer. Custom made of spring steel, the clip is designed not to mar the pressure-sensitive labels on the marker barrel, Colavitti says, because a high quality appearance for the premium marker is essential. The clips are mounted on 2½’’ centers.
The clip conveyor transports markers in an enclosed conveyor section that forms an overhead bridge. The bridge provides a walkway for operators to move freely between the assembly and packaging operations. It halves the walking distance compared with a straight-line conveyor, Colavitti says.
“The bridge is critical,” notes Colavitti, “because it allows one operator to handle the entire system.”
Sanford had the system designed to accept a standard bin size. The plastic bins are sourced from Orbis (Mentor, OH). Colavitti says that they are easier for operators to unload than the deep, one-row bins they had used before. The high-density polyethylene bins measure 21’’x 13’’x6’’ and include a corresponding lid.
Loading is automatic after an operator places a reusable stainless-steel grid atop the standard bin and then places the bin at the gravity-flow infeed. The grid forms a 2x5 pattern of 10 slots through which the markers are filled.
Bins move in a squared U-shape from the gravity flow infeed through the loading sequence and to the gravity flow outfeed conveyor several feet opposite the infeed conveyor. Each marker is knocked from the clip by a pair of interconnected, pneumatically actuated levers that are above each end of the marker. Markers are collated in a bucket-equipped assembly and are loaded into the bin through each pair of slots as 54 markers per slot or 540 total per bin. During loading, the bin is indexed linearly via servo motor after each set of slots is filled. This straight-line travel during loading, Colavitti says, “drastically” simplified operations.
Side storage
Sanford wanted to store the bins on their sides so markers would be “primed” with ink to write smoothly the first time a consumer uses one. Colavitti found that foamed pipe insulation, cut in half lengthwise, filled the headspace void perfectly to keep the markers in place before the lid is placed and secured by a twist tie. Ergonomically designed, each bin weighs less than 20 lb when full. The bins are stored until needed for blister packaging.
In addition to bulk loading for packaging, the system controls are programmed to revert to bulk loading in the event of a problem while cartoning (see sidebar). A programmable logic controller runs both the cartoner and the bulk packing operations. Another PLC is onboard the PMI case packer.
For Sanford, automated bulk loading marks a new era in production efficiency.
See sidebar to this article: Integrated cartoning and casing