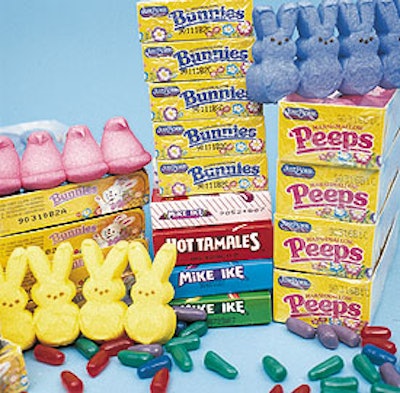
Confectionery company Just Born has long relied on ink-jet coders for date codes on cartons of its popular marshmallow Peeps. But only recently did the firm move from embossing technology to ink-jet coding on its 2.12- and 8-oz cartons of Hot Tamales, Mike and Ikes, and newly introduced Zours. These sell in theaters, convenience stores, supermarkets and other retail outlets for about $1.30 per 8-oz carton and 60¢ per 2.12-oz box.
The ink-jet coders selected by the Bethlehem, PA-based company were supplied by Domino Amjet (Gurnee, IL). Each A100 printer is mounted on one of the customized filling systems assembled in-house by Just Born.
Reggie Heffelfinger, plant maintenance technical supervisor, says the Domino coders have helped the company cut labor costs significantly. “There’s just less mechanical labor involved,” he says, compared to the previous embossing equipment, which required manual changing of the steel embossing characters between each shift. “It saves us at least a half hour every shift.” He adds that the embossing units were hard to find and expensive. Heffelfinger notes that the A100 coders have paid for themselves since they were installed in 1999.
Quick changeovers
The A100s apply codes that typically indicate the year, month, day, and shift the package was sealed. The machine number is also included.
Heffelfinger says each of the A100s is changed over two to three times daily. So ease of changeover is critical. All the operator does is select from a list of preloaded programs or recipes in a preset menu.
Heffelfinger explains that the maximum amount of time spent to change over the Domino A100 coders is 10 minutes, and that would only be for custom work. “You just go into a message menu on a control panel and enter the different text, hit print, and away you go,” he says.
Another time saver for the candy manufacturer is a maintenance agreement it struck with Domino when the coders were installed. Among the plan’s benefits is preventive maintenance performed by the supplier every 2ꯠ hours of operation.
“Domino comes in and works on machines when they’re not in use,” Heffelfinger explains. “We reinstall them during the weekends when we’re not running and remove units on other lines and put them off to the side for maintenance. That way, we don’t have to disrupt production,” he says.
For Just Born, the agreement reduces the need for in-house labor. “We were looking for something where our maintenance people could avoid repetitive work and focus on more proactive tasks. We wanted them to get more involved with the plant’s major projects rather than cleaning and servicing ink-jet printing equipment, which gets monotonous. This helps them learn new things compared to working on the same thing every day,” he says.
Each A100 is mounted on a customized rotary filler. First, prepared candy is delivered to the line in a storage hopper. It’s emptied onto a conveyor that takes it to a computerized combination scale. The proper amount of candy is funneled into cartons that have been erected by the filler. Running at approximately 100/min, each 8-oz carton’s leading flap is detected by a photoeye, which triggers the A100 coder. It prints the date code on the lead flap of the carton. When coding on the 2.12-oz packs, the coder can run at 525/min.
The carton flaps are then glued and closed with hot melt. Finished cartons are conveyed past a checkweigher and metal detector. Next, they move through a wraparound case packer. Cases are then conveyed into a vertical lift, which delivers them to a robotic palletizer from Fanuc Robotics (Auburn Hills, MI) that was installed within the last year.
Just Born occasionally conducts tests on its lines for different brands and sizes, Heffelfinger says. Because the Domino coders are so easy to change over, they make it easy to try new products, Heffelfinger says. “We’ll just come in and run a test on a brand new product and see what problems we run into. In that case, it’s really nice to have that kind of equipment flexibility.”