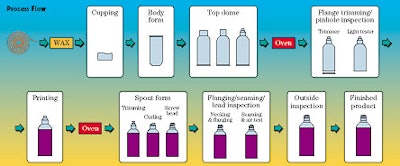
Sapporo Breweries was the first to commercialize the aluminum bottle (see story on page 144) recently developed by Daiwa Can (Tokyo, Japan). But Sapporo isn’t the only fan of Daiwa’s new bottle can. At the Cannex 2000 show in Brisbane, Australia, the package was the overall winner of the Cans of the Year award, sponsored by The Canmaker magazine of England.
Packaging World recently talked with Daiwa at its Tokyo headquarters about the technology used to make this award-winning container, available in 350-, 450- and 500-mL (11.9-, 15.2- and 16.9-oz) sizes. While certain aspects of the manufacturing process remain proprietary, Daiwa shared much of its know-how.
The container is made in one continuous process. Cupping, drawing and ironing steps are essentially the same as for a conventional aluminum can. But rather than necking-in the finish as in conventional can making, the finish is given a dome. This is a drawing process, says Daiwa, but the firm declines to identify how many stages are involved. Then the container is sent through an oven, presumably to anneal or soften the metal in case the steps involved in doming have stressed the metal to the point of brittleness.
Exiting the oven, the container’s flange is trimmed, and every bottle then passes through a light tester that detects and rejects containers with pinholes. Printing is next, done offset in five colors. Next, the container finish is trimmed and “outcurled,” which gives the bottle its smooth finish and pleasing mouth feel. Then the 28-mm neck is threaded in what Daiwa calls a drawing process. Finally, the aluminum bottom is seamed on, and the container goes through a high-pressure air tester to check for leaks. Following a visual inspection, the process is complete.
Feeling pressure from PET
In development at Daiwa for about three years, the aluminum bottle is an attempt to curb the rapid growth of polyethylene terephthalate in the Japanese beverage market.
“PET for beverages has been growing substantially,” says Shigeo Imayama, manager of planning and promotion for international operations at Daiwa Can. “That puts those of us in the aluminum can business under extreme pressure. We believe this new development can be a very good tool to compete with PET because of barrier properties and recyclability.”
Currently two lines, each producing 500 bottles/min, are running in Daiwa’s Tokyo plant. Imayama says both will be upgraded shortly to produce 700 bottles/min.
The technology used for container shaping, intriguing as it is, is only half of what makes this container so significant. Also important is that these cans do not undergo the coating process that aluminum cans typically require. The inside coating, of course, prevents acids or other components in food and beverage products from attacking or pitting the inside of an aluminum can. The outside coating, meanwhile, enhances ink adhesion and facilitates the ironing process that gives the can its shape.
The problem with coating technology is that it involves solvent emissions and/or waste water issues, both undesirable from an environmental standpoint. For at least the past five years, everyone from Hoogovens to Alcoa to British Steel to Toyo Seikan has tried to develop alternatives that are “greener.” But few have been successful, usually because the cost of the alternative technologies has been prohibitive.
Success with lamination
Daiwa Can, apparently, has been successful in developing film lamination as an alternative to conventional can coating. Its bottle can is made from aluminum coil that has had PET film laminated to both sides. Film thickness is considered proprietary. Daiwa is also rather guarded about the method of lamination it uses, saying only that the film is added to the aluminum “by means of heat lamination.”
The significance of this laminating process is that it eliminates the emission of volatile organic compounds (VOCs) because there are no solvent-based coatings to be cured. The bottle can represents Daiwa’s first successful large-scale application of this new technology.
When asked to comment on the cost of its laminating technology compared to available alternatives, Daiwa Can elects not to. Industry insiders, however, wonder why laminating a discrete layer of PET film was chosen when extrusion, a more direct process, could eliminate costly handling steps like PET film winding, film transport and film unwind.
For now, specific questions about how Daiwa manages to produce its unique package profitably will have to remain unanswered. But there seems little doubt that Daiwa believes the bottle can is worth investing in. According to Imayama, by the end of this year, six more lines for producing bottle cans will have been added.