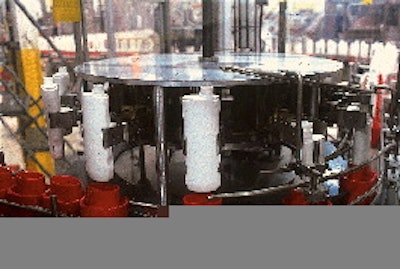
Due to the success of the rapidly growing liquid body wash category, Chesebrough-Pond's, Greenwich, CT, needed to boost output at its Raeford, NC, plant. At the same time, eight different package shapes and sizes needed to be accommodated-up from four previously-without cutting into line efficiency. Worse, there was little time to spare. "This was truly a crash project," says Paul Redwood, packaging systems manager. "From start to finish the project team had 20 weeks from when they said go."
While a brute force increase in filling capacity would have addressed the speed issue, it wouldn't have addressed the proliferation of container sizes on the line. Instead, Chesebrough-Pond's engineers chose to maintain the existing filler and instead revamp the line with an automated puck handling system. The pucks are individual plastic holders that carry unstable bottles throughout the packaging line. While only three of the bottles are actually unstable enough to require pucks-tottles in three sizes for Lever 2000 body wash by sister company Lever Bros.-it was decided to use pucks on all containers on the line to simplify line changeover.
"The pucks come with the same outside dimensions so we don't have to change or adjust any starwheels, timing worms or guides," says Redwood. "And we had the pucks manufactured with platforms in them so that we end up with a common container neck height going into every machine. That way we don't have to make height adjustments during changeover." The polypropylene pucks are designed and injection-molded by Integrated Puck Systems (Ivyland, PA).
A new Omega Design (Exton, PA) unscrambler/puck inserter and de-pucker was added to handle the pucks. The line was also upgraded with a new bottle orienter, capper and washdown-grade, closed-top sanitary conveyors. Interestingly enough, the filler was not upgraded, though Redwood says that will probably happen in the future. The redesigned line began operation in July '96.
Speed with flexibility
Because the pucks provide stability during container handling, C-P was able to boost line speeds by about 25%. "We no longer have to operate our machines so slowly," observes Redwood.
Just as critical, however, is changeover time, which has been slashed by two-thirds, though the company wouldn't specify the exact time involved. Virtually all machines were designed to accommodate tool-free changeover. In fact, changeover is so simple that many of the line's operators play a bigger role than usual during changeover, says Redwood. "The beauty here is that we have full involvement of some operators during changeover. We also involved operators and mechanics up-front during line design, installation and startup. They took ownership of the line and it just took off."
The line packages a variety of bottle shapes and sizes, holding from 6 to 18 oz. Containers, extrusion/blown of high-density polyethylene, are supplied by C-P's in-house blow molding operation as well as by various suppliers. Some containers are supplied pre-labeled with pressure-sensitive labels and the rest are labeled in-line. All take snap-fit PP closures with snap-hinge lids. Body washes are bottled for several brands, including Caress, Dove, Vaseline and Lever 2000.
The internal dimensions of each puck are designed to fit each container, with fins that grip the bottles and platforms that elevate them to a common container neck height. Pucks for each bottle are molded in a different color to aid in identification during changeover. Redwood says about 2귔 individual pucks are required to fill the line for each container style.
Shoehorn fit
Redwood says it was a challenge cramming additional puck handling equipment into an already tight floorplan. "We had to shoehorn everything in. Credit goes to our CAD designer in working with the many iterations that the project team put him through to get the right footprint," says Redwood.
The operation starts out as cases of bulk bottles are emptied into a hopper that feeds the Omega unscrambler/puck loader. Bottles are elevated up into the centrifugal sorting bowl, where they are delivered to a drop chute. At the bottom of the chute, bottles are picked off by bottle grippers on a rotary turret. Sensors on the turret detect whether the containers are upside down; if so, the pockets flip the containers right side up by rotating them 180°.
Up to this point, the machine is basically Omega's standard un-scrambler. One difference from a regular unscrambler is that after bottles are uprighted, they are lowered into the pucks being conveyed alongside the rotary turret at that point. An Omega-designed cam-actuated shuttle chute prevents C-P's Vaseline containers with offset necks from interlocking in the drop chute.
Once loaded into pucks, containers enter a rotary orienter that correctly orients bottles with offset necks so that the bottle openings are in the same place each time for volumetric filling. Orienting is also used for pre-labeled bottles.
Next bottles pass through the rotary volumetric filler, followed by capping. Once capped, containers are ready for de-pucking.
First, containers enter a timing screw next to the depucker's rotary turret that's very similar to the turret of the puck inserter. The pucks are turned 90° so that the bottle grippers can grip the narrow edge of the containers for better overall throughput. The grippers hold the containers while stripper rails divert the pucks downward and away from the bottles. For tottles only, the depucker inverts them 180° so that their caps face the conveyor with the unstable end in the air; all other bottles are not inverted. The containers are then released onto a takeway conveyor for downstream coding, labeling and case packing (see sidebar, page 44).
"The technical challenge here is that we had containers coming in at one level and we had to deliver them onto another discharge conveyor at a different elevation," says Redwood. Plus, due to the varying platform heights inside the pucks, the grippers on the depucker were grabbing the bottles at different heights for each bottle size.
"Bottles ended up being too far down or too far away from the conveyor they discharge onto," says Redwood, resulting in occasional fallen containers. The solution was to engineer cams to lower bottles to a common discharge height. The cams also synchronize the speed of the discharge conveyor with that of the turret for a smoother transition.
Once containers are removed from the pucks, the pucks recirculate back to the pucking station via an overhead conveyor that conserves floorspace and provides an accumulation buffer so that the unscrambler always has a constant supply of new pucks.
Supplied by CarryLine (Sarasota, FL), the anodized aluminum extruded conveyor was selected especially for its interchangeable chain links. "With most conveyors, you have to replace the entire belt if one section of chain wears," says Redwood. "With this, you just snap out the worn link and snap in a new one."
One dramatic difference in changeover is that the pucks have to be swapped out each time a container's shape changes. Still, Redwood claims this is included in the reduced changeover time. Old pucks can simply be conveyed into a bin. New pucks must be placed onto the conveyor by hand. Pucks are currently steam-cleaned manually, and Redwood says automated puck washing equipment is being considered to speed this process further.
Operating for about 10 months now, the revamped line is well on its way to paying back its investment. "Our minimum internal standard for return-on-investment is less than two years," says Redwood. "We easily exceeded that."
But more important, the line is designed to be changed over without requiring a great deal of skill or fuss. Or, as Redwood puts it, "We told our suppliers we wanted everything to be 'NT cubed': no tools, no time and no tweaking."
Finally, Redwood credits the entire project team for making this work. "The energies and efforts invested by the project team to start up on time and without disrupting the supply chain were critical to the success of this project," says Redwood. The project team won Chesebrough-Pond's 1996 Quality in Action award, an internal honor bestowed on only one team in the plant each year.