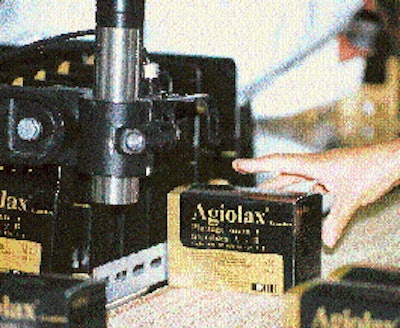
It's a plant manager's nightmare. According to Mexican law, pharmaceutical companies-not retailers-must mark prices on all over-the-counter remedies. That's fine if the price doesn't change often. But in 1995, volatile currency fluctuations forced pharmaceutical manufacturers such as Byk Gulden, located in Naucalpan de Juarez, to frequently re-price finished packages in the warehouse. Byk Gulden had been manually applying preprinted pressure-sensitive pricing labels. But labeling of products after a price change quickly became an expensive proposition, requiring the pharmaceuticals maker to hire many extra people to apply the new labels. Not only was this expensive, it delayed shipments of finished products to distributors. In mid-'95, the company installed two Linx 4200 and one Linx 6000 small-character ink-jet coding units manufactured by Diagraph (St. Louis, MO). The 4200s print the price, lot and expiration date in two lines on to chipboard cartons that contain pouches of medicinal powders. The model 6000 prints four lines of information-including price, lot and expiration date-on rigid plastic containers that hold tablets. The ink-jet coders provide several benefits. Most obvious, the coders reduced labor on the packaging lines: from five to 10 workers per line down to three, according to Eutimio Quevedo, Byk Gulden's director of operations. But perhaps more important to Quevedo is the ability to respond to fast-moving changes in economic conditions. "It used to take three days to manually re-label products in the warehouse," says Quevedo, depending on the number of products needing to be re-priced. "Now it just takes us 12 hours with the coder." Plus, delivery delays to distributors have been reduced. In re-pricing, workers must still manually obliterate the old price with a marker, but the new price is added automatically. The new price is printed near the old, covered one. The coders, which are used in conjunction with portable conveyors, can be wheeled to the warehouse where packages are to be rerun. Quevedo says the reliability of the coders has been "very good" and claims that it's quick and easy to change ink containers. He says it takes about five minutes to change price, lot and expiration date with the portable terminal. A final benefit is that the coders can be temporarily wheeled over to the other packaging lines whose coders are down for maintenance or repair. Despite Mexico's low wages, Quevedo says, "We will pay for the equipment in one year" due solely to labor savings. And finally, he points out, "we can react faster to price changes in the market."